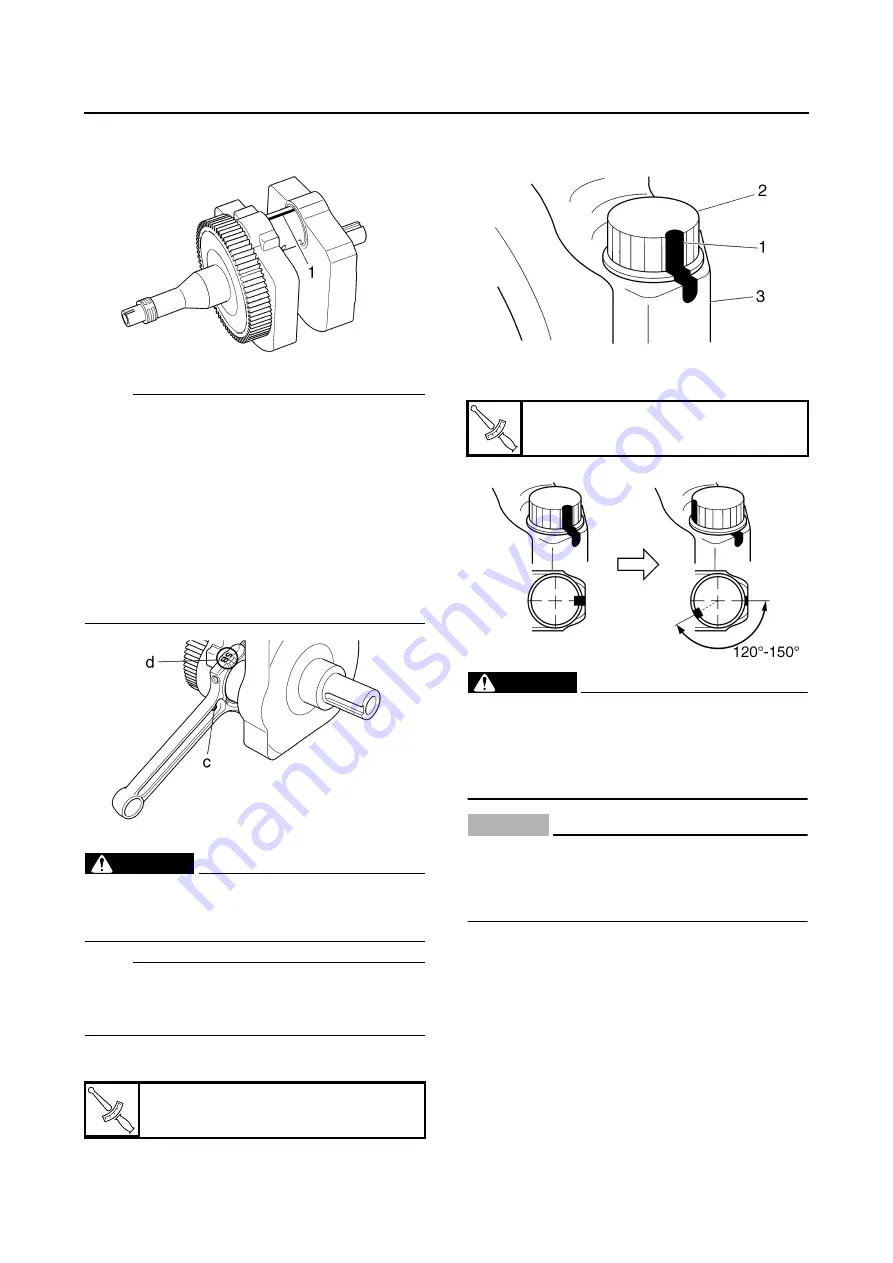
CRANKSHAFT
5-88
c. Put a piece of Plastigauge
®
“1” on the crank-
shaft pin.
d. Assemble the connecting rod halves.
NOTE:
• Do not move the connecting rod or crankshaft
until the clearance measurement has been
completed.
• Lubricate the bolts threads and nut seats with
molybdenum disulfide grease.
• Make sure the projection “c” on the connecting
rod faces towards the left side of the crank-
shaft.
• Make sure the characters “d” on both the con-
necting rod and connecting rod cap are
aligned.
e. Tighten the connecting rod bolts.
WARNING
EWA12890
• Replace the connecting rod bolts with new
ones.
• Clean the connecting rod bolts.
NOTE:
The tightening procedure of the connecting rod
bolts is angle controlled, therefore tighten the
bolts using the following procedure.
f. Tighten the connecting rod bolts to the spec-
ified torque.
g. Put a mark “1” on the connecting rod bolts “2”
and the connecting rod cap “3”.
h. Tighten the connecting rod bolts further to
reach the specified angle 120°–150°.
WARNING
EWA12900
When the bolts are tightened more than the
specified angle, do not loosen the bolt and
then retighten it.
Replace the bolt with a new one and perform
the procedure again.
CAUTION:
EC5YU1008
• Do not use a torque wrench to tighten the
bolt to the specified angle.
• Tighten the bolt until it is the specified an-
gle.
i. Remove the connecting rod and big end
bearings.
Refer to “REMOVING THE CONNECTING
RODS” on page 5-87.
j. Measure the compressed Plastigauge
®
width
“e” on the crankshaft pin.
If the crankshaft-pin-to-big-end-bearing
clearance is out of specification, select re-
placement big end bearings.
T
R
.
.
Connecting rod bolt (1st)
15 Nm (1.5 m·kg, 11 ft·lb)
T
R
.
.
Connecting rod bolt (final)
Specified angle 120°–150°
Summary of Contents for 2005 MT-01
Page 1: ...2005 SERVICE MANUAL MT 01 T 5YU1 AE1 ...
Page 7: ...GEN INFO 1 ...
Page 9: ......
Page 24: ...SPEC 2 ...
Page 26: ......
Page 61: ...LUBRICATION SYSTEM CHART AND DIAGRAMS 2 35 1 4 3 2 ...
Page 63: ...LUBRICATION SYSTEM CHART AND DIAGRAMS 2 37 3 2 1 1 A A B B B B A A ...
Page 64: ...LUBRICATION SYSTEM CHART AND DIAGRAMS 2 38 1 Oil pump 2 Oil strainer crankcase 3 Oil pipe 1 ...
Page 65: ...LUBRICATION SYSTEM CHART AND DIAGRAMS 2 39 3 4 2 1 A ...
Page 77: ...CABLE ROUTING 2 51 A A B D D E F G C 1 2 3 3 4 4 5 6 7 8 9 ...
Page 79: ...CABLE ROUTING 2 53 A A A A A B C D D E F A A 1 1 2 2 5 3 6 8 10 10 11 A G H I K J 4 7 9 9 9 ...
Page 83: ...CHK ADJ 3 ...
Page 120: ...CHAS 4 ...
Page 195: ...ENG 5 ...
Page 199: ......
Page 214: ...ENGINE REMOVAL 5 15 25 10 11 28 26 12 29 27 14 30 26 24 2 21 19 18 18 19 23 22 20 9 13 ...
Page 279: ...CRANKCASE 5 80 ...
Page 296: ...FUEL 6 ...
Page 298: ......
Page 312: ......
Page 313: ...ELEC 7 ...
Page 327: ...CHARGING SYSTEM 7 12 1 AC magneto 2 Rectifier regulator 4 Battery 8 Main fuse ...
Page 329: ...CHARGING SYSTEM 7 14 ...
Page 339: ...SIGNALING SYSTEM 7 24 ...
Page 381: ...FUEL INJECTION SYSTEM 7 66 ...
Page 385: ...FUEL PUMP SYSTEM 7 70 ...
Page 389: ...MUFFLER COOLING SYSTEM 7 74 ...
Page 398: ...IMMOBILIZER SYSTEM 7 83 Example fault code 52 a b a Light on b Light off ...
Page 399: ...IMMOBILIZER SYSTEM 7 84 ...
Page 400: ...ELECTRICAL COMPONENTS 7 85 EAS27970 ELECTRICAL COMPONENTS 4 3 5 7 6 8 9 10 12 13 14 15 1 2 11 ...
Page 402: ...ELECTRICAL COMPONENTS 7 87 3 4 6 5 8 7 9 11 12 13 14 15 16 17 18 1 2 10 ...
Page 424: ...TRBL SHTG 8 ...
Page 426: ......
Page 433: ......
Page 434: ...YAMAHA MOTOR CO LTD 2500 SHINGAI IWATA SHIZUOKA JAPAN ...