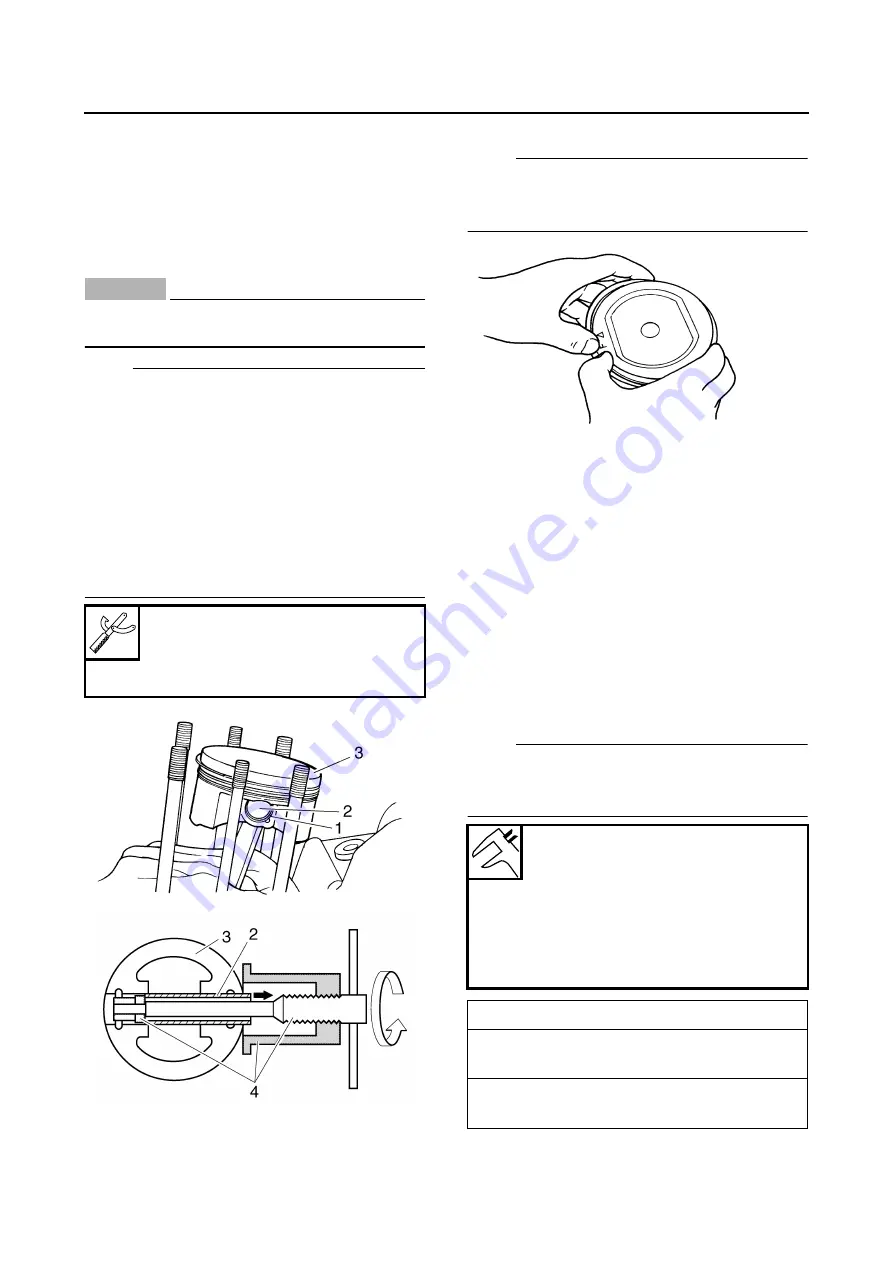
CYLINDERS AND PISTONS
5-42
EAS24380
REMOVING THE PISTONS
The following procedure applies to all of the pis-
tons.
1. Remove:
• Piston pin clips “1”
• Piston pin “2”
• Piston “3”
CAUTION:
ECA13810
Do not use a hammer to drive the piston pin
out.
NOTE:
• Before removing the piston pin clip, cover the
crankcase opening with a clean rag to prevent
the piston pin clip from falling into the crank-
case.
• For reference during installation, put an identi-
fication mark on each piston crown.
• Before removing the piston pin, deburr the pis-
ton pin clip’s groove and the piston’s pin bore
area. If both areas are deburred and the piston
pin is still difficult to remove, remove it with the
piston pin puller set “4”.
2. Remove:
• Top ring
• 2nd ring
• Oil ring
NOTE:
When removing a piston ring, open the end gap
with your fingers and lift the other side of the ring
over the piston crown.
EAS24410
CHECKING THE CYLINDERS AND PISTONS
The following procedure applies to all of the cyl-
inders and pistons.
1. Check:
• Piston wall
• Cylinder wall
Vertical scratches
→
Rebore or replace the
cylinder, and replace the piston and piston
rings as a set.
2. Measure:
• Piston-to-cylinder clearance
▼▼▼
▼
▼ ▼▼▼
▼
▼ ▼▼▼
▼
▼ ▼▼▼
▼
▼ ▼▼▼
▼
▼ ▼▼▼
▼
▼▼▼
a. Measure cylinder bore “C” with the cylinder
bore gauge.
NOTE:
Measure cylinder bore “C” by taking side-to-side
and front-to-back measurements of the cylinder.
Then, find the average of the measurements.
Piston pin puller set
90890-01304
Piston pin puller
YU-01304
Cylinder
Bore
97.000–97.010 mm (3.8189–
3.8193 in)
Taper limit
0.050 mm (0.0020 in)
Out of round limit
0.050 mm (0.0020 in)
“C” = maximum of D
1
–D
6
“T” = maximum of D
1
or D
2
- maximum of D
5
or D
6
“R” = maximum of D
1
, D
3
or D
5
- minimum of
D
2
, D
4
or D
6
Summary of Contents for 2005 MT-01
Page 1: ...2005 SERVICE MANUAL MT 01 T 5YU1 AE1 ...
Page 7: ...GEN INFO 1 ...
Page 9: ......
Page 24: ...SPEC 2 ...
Page 26: ......
Page 61: ...LUBRICATION SYSTEM CHART AND DIAGRAMS 2 35 1 4 3 2 ...
Page 63: ...LUBRICATION SYSTEM CHART AND DIAGRAMS 2 37 3 2 1 1 A A B B B B A A ...
Page 64: ...LUBRICATION SYSTEM CHART AND DIAGRAMS 2 38 1 Oil pump 2 Oil strainer crankcase 3 Oil pipe 1 ...
Page 65: ...LUBRICATION SYSTEM CHART AND DIAGRAMS 2 39 3 4 2 1 A ...
Page 77: ...CABLE ROUTING 2 51 A A B D D E F G C 1 2 3 3 4 4 5 6 7 8 9 ...
Page 79: ...CABLE ROUTING 2 53 A A A A A B C D D E F A A 1 1 2 2 5 3 6 8 10 10 11 A G H I K J 4 7 9 9 9 ...
Page 83: ...CHK ADJ 3 ...
Page 120: ...CHAS 4 ...
Page 195: ...ENG 5 ...
Page 199: ......
Page 214: ...ENGINE REMOVAL 5 15 25 10 11 28 26 12 29 27 14 30 26 24 2 21 19 18 18 19 23 22 20 9 13 ...
Page 279: ...CRANKCASE 5 80 ...
Page 296: ...FUEL 6 ...
Page 298: ......
Page 312: ......
Page 313: ...ELEC 7 ...
Page 327: ...CHARGING SYSTEM 7 12 1 AC magneto 2 Rectifier regulator 4 Battery 8 Main fuse ...
Page 329: ...CHARGING SYSTEM 7 14 ...
Page 339: ...SIGNALING SYSTEM 7 24 ...
Page 381: ...FUEL INJECTION SYSTEM 7 66 ...
Page 385: ...FUEL PUMP SYSTEM 7 70 ...
Page 389: ...MUFFLER COOLING SYSTEM 7 74 ...
Page 398: ...IMMOBILIZER SYSTEM 7 83 Example fault code 52 a b a Light on b Light off ...
Page 399: ...IMMOBILIZER SYSTEM 7 84 ...
Page 400: ...ELECTRICAL COMPONENTS 7 85 EAS27970 ELECTRICAL COMPONENTS 4 3 5 7 6 8 9 10 12 13 14 15 1 2 11 ...
Page 402: ...ELECTRICAL COMPONENTS 7 87 3 4 6 5 8 7 9 11 12 13 14 15 16 17 18 1 2 10 ...
Page 424: ...TRBL SHTG 8 ...
Page 426: ......
Page 433: ......
Page 434: ...YAMAHA MOTOR CO LTD 2500 SHINGAI IWATA SHIZUOKA JAPAN ...