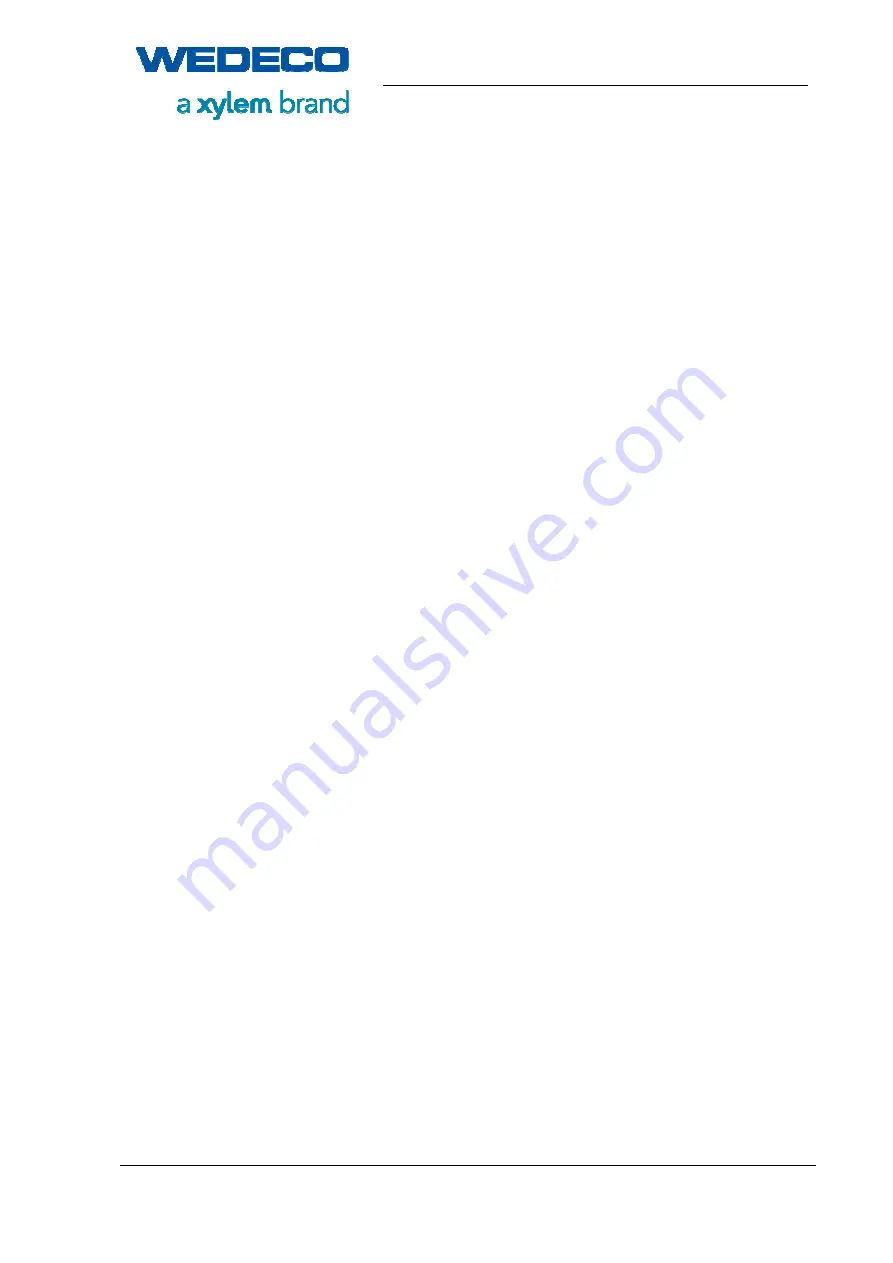
Manual Ozone Generating System
SMOevo
PLUS
Safety
Manual_SMOevoPLUS_eng_01.2019.doc
page 20 of 179
3.3.4 Technical Ventilation System
Ensure that rooms housing ozone systems are equipped with a technical ventilation system
guaranteeing an air exchange of at least three times per hour. A suction ventilation system
with a suction opening located directly above the floor must be installed. The ventilation
system must turn on automatically when a gas detector responds to the potential danger.
3.3.5 Door Switch
The ozone generating system is equipped with a door switches located in the electrical
cabinets. Once a cabinet door is opened during operation, the ozone system will turn off
immediately.
Do not remove or bridge the door switch at any time!
3.3.6 Protective Covers
All system components of the converter, all electrical equipment and the system control are
installed in a cabinet secured by a lockable door to prevent contact with the components
which could lead to severe injuries.
Protective devices may not be removed or bridged during operation of the system!
If removal of any protective devices is required during maintenance or repair work, ensure
that these devices are refitted and checked immediately upon completion of the maintenance
and repair work. Only use the original mounting material of the protective devices!
3.3.7 Safety and Warning Signs
All the safety and warning signs placed on the ozone system must be clearly legible.
Ensure that damaged type plates and warning signs are replaced immediately.