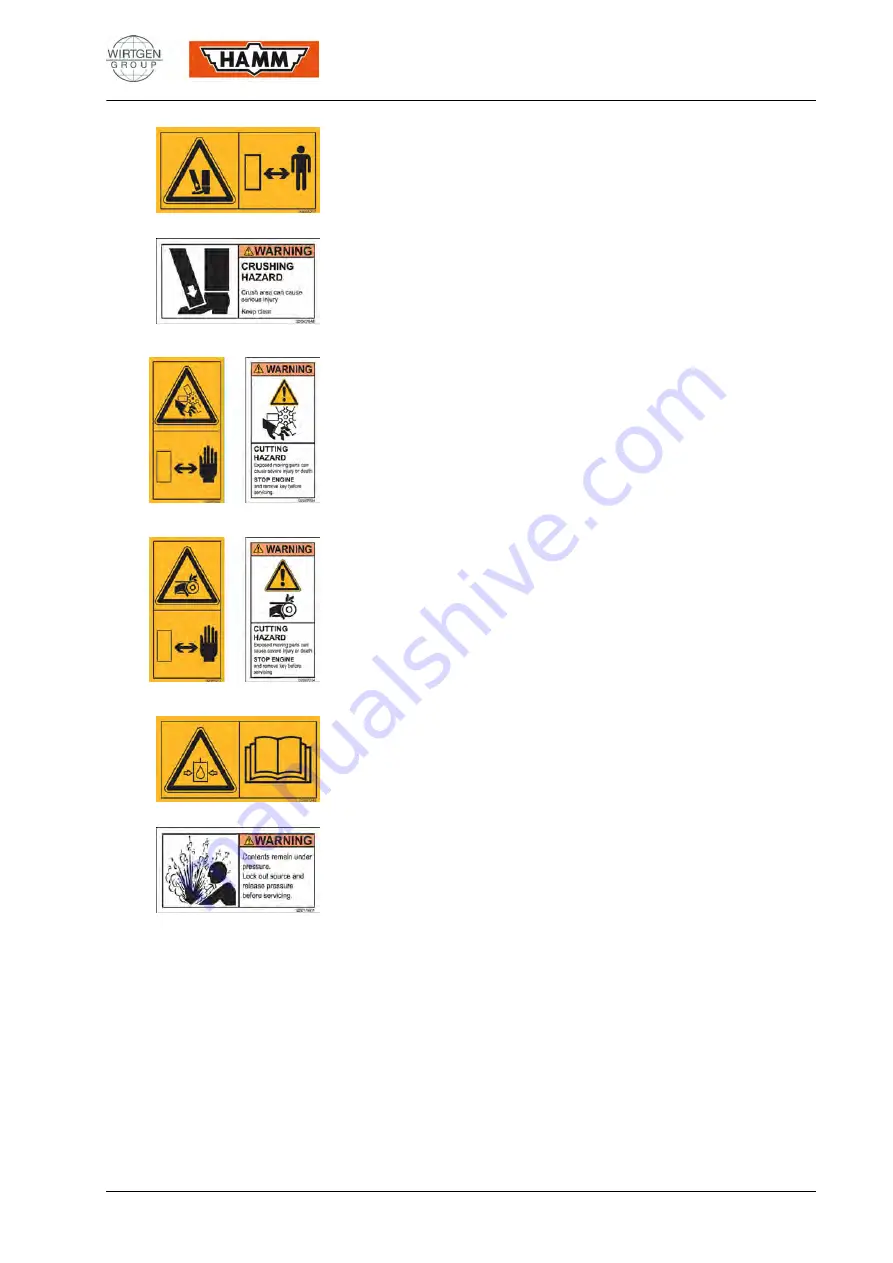
General
Stickers on the machine
© HAMM AG 2011
2153734_02_BAL_GRW280_H195_en
37
Edge pressing assembly
Risk of crushing! Pinch point can cause serious injuries or fatality. Keep
away. Prior to maintenance and adjustment works, shut down machine
and remove ignition key.
Fan blade
Hazard due to rotating parts! With the machine running, serious injuries
or fatality may be caused. Prior to maintenance work, shut down engine
and remove ignition key. Wait until all machine components have come
to a standstill.
V-belt
Risk of trapping! Open belts or chains. With the machine running,
serious injuries or fatality may be caused. Prior to maintenance work,
shut down engine and remove ignition key. Wait until all machine
components have come to a standstill.
Accumulator
Tank under pressure. System contains accumulator. Prior to starting
service work, read operating and service manual.