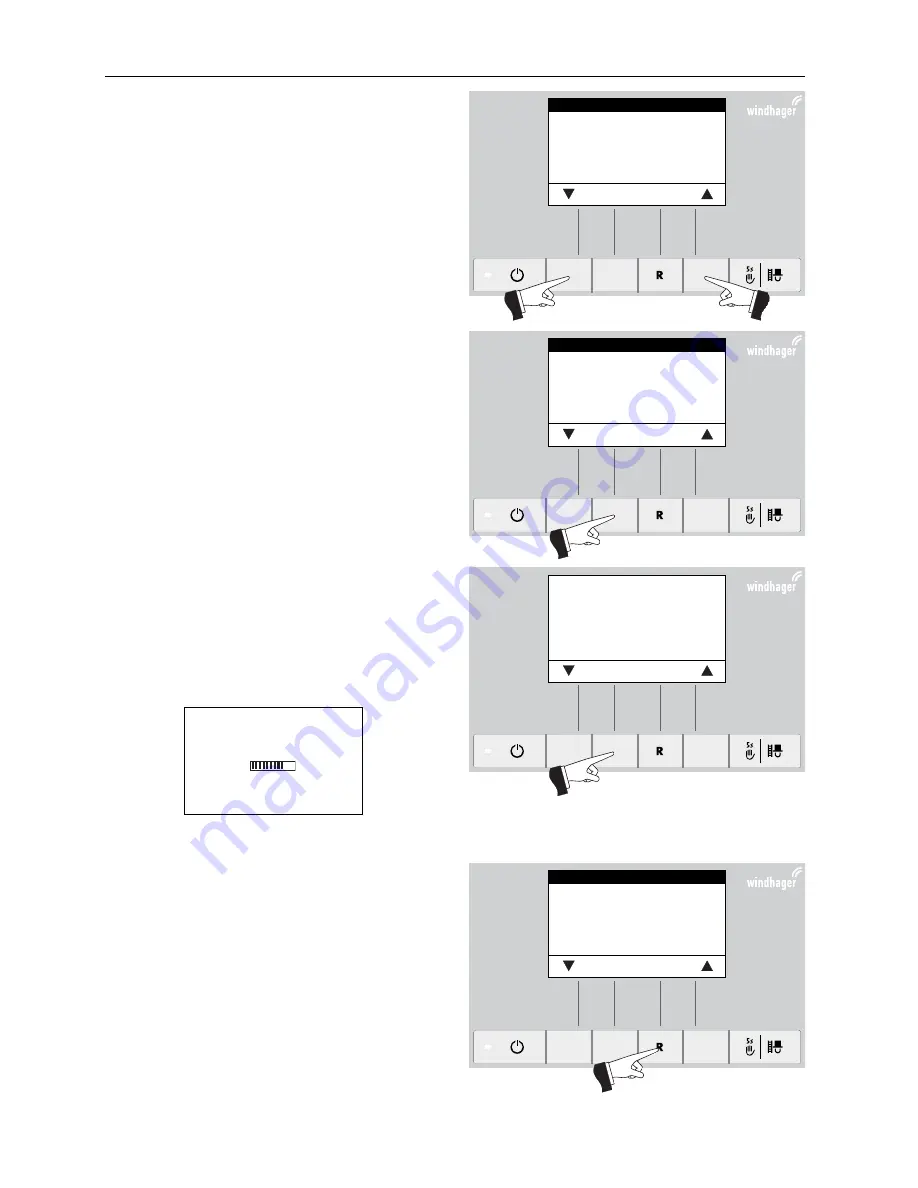
26
2.
Operation
Use the arrow keys to mark the sub-menu item “Con-
firm stage 1 cleaning“ or “Confirm stage 2 cleaning“ –
Fig. 54.
Fig. 54
Confirm stage 1 cleaning
Confirm stage 2 cleaning
Pellet consumption
Time
Feed operating mode
Time profile feed
Choose
Back
Confirm the marked sub-menu item “Confirm stage 1
cleaning“ or “Confirm stage 2 cleaning“ by pressing the
Choose
button – Fig. 55.
Pressing the Yes button resets the boiler cleaning –
Fig. 56. The display shows “Parameter is saved” for a
few seconds (Fig. 57) and then changes back to the pre-
vious level – Fig. 58.
Fig. 55
Confirm stage 1 cleaning
Confirm stage 2 cleaning
Pellet consumption
Time
Feed operating mode
Time profile feed
Choose
Back
Fig. 56
Was stage 1 cleaning performed
according to the instructions?
Confirm
Yes
Back
The menu item or sub-menu item is exited by pressing
the Back button (Fig. 58) or after a delay of 10 minutes.
Fig. 57
Fig. 58
Confirm stage 1 cleaning
Confirm stage 2 cleaning
Pellet consumption
Time
Feed operating mode
Time profile feed
Choose
Back
Parameter is saved
(Animated symbol)