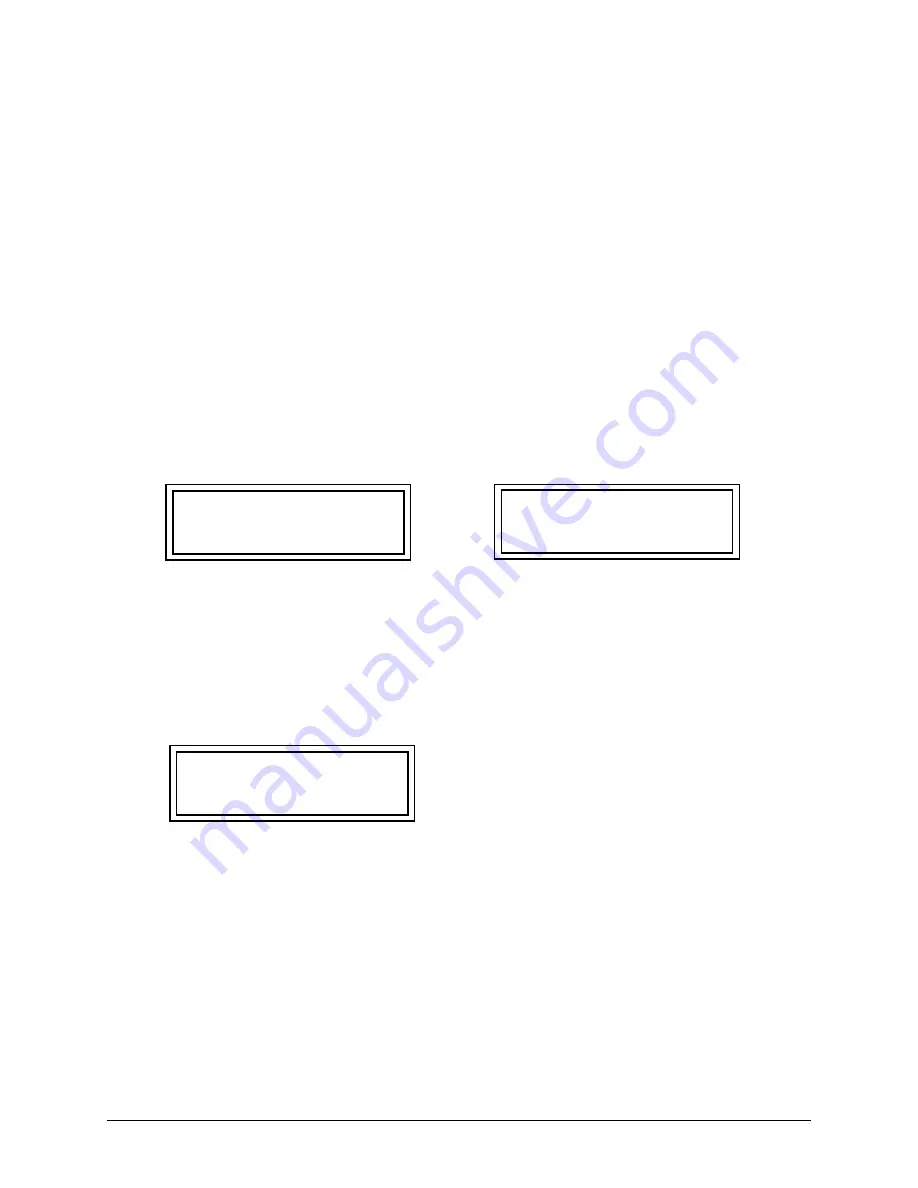
49
November 2008
Part No. 920559 Rev H
APPENDIX A1
OVATION QCAT SELF-TEST PROCEDURE
The following are instructions for testing the CAT (Customer Activated Terminal) on the dispenser.
1.
QCAT SYSTEM SELF-TEST
The following paragraphs provide instructions for testing and setting the address of the QCAT. During the
self-test, the system is designed to pause 25 seconds for a response to self-test prompts. When the 25 second
time limit expires, the system automatically advances to either the next self-test or returns to the on-line
mode.
1.1. ENTERING SELF-TEST MODE
Step 1
Power down the QCAT.
Step 2
Power up the QCAT while holding down any key on the keypad until the alternating message
below appears on the display.
Step 3
Press the indicated key or press NEXT to continue to the next screen prompt.
1.2. QCAT SOFTWARE REVISION LEVEL AND DATA LINK ADDRESS
Step 1
Continue holding the key down until the “REV” message below appears on the display, then
release. Once the system displays the “REV” message, the module has successfully entered the
self-test mode.
The top row of information in the “REV” message display represents the QCAT software revision.
The bottom row is the current terminal address for the data link. Data link addresses are assigned to
the module using the same number as the fueling point.
Step 2
If the CAT’s data link address is correct, press the
ENTER
key. To change the address, enter the
correct address number on the keypad and press
ENTER
(if the CAT is equipped with a DES
keypad, the keypad revision will be displayed).
CONTRAST ADJUST
PRESS NEXT TO EXIT
YES = DARKER
NO = LIGHTER
REV XXX MM/DD/YY
ADDRESS = YY
Summary of Contents for Ovation
Page 1: ...INSTALLATION Ovation Dispensers OPERATION...
Page 3: ...November 2008 Part No 920559 Rev H Ovation Series Dispensers Installation Operation...
Page 4: ...November 2008 Part No 920559 Rev H...
Page 54: ...48 Part No 920559 Rev H November 2008...
Page 66: ...60 Part No 920559 Rev H November 2008...
Page 67: ...61 November 2008 Part No 920559 Rev H DISTANCE BETWEEN EYE BOLTS 33 1...
Page 68: ...62 Part No 920559 Rev H November 2008 INSTALLATION INSTRUCTION page 1 of 2 OVATION MODEL R13...
Page 69: ...63 November 2008 Part No 920559 Rev H INSTALLATION INSTRUCTION page 2 of 2 OVATION MODEL R13...
Page 70: ...64 Part No 920559 Rev H November 2008 INSTALLATION INSTRUCTION page 1 of 2 OVATION MODEL B23...
Page 71: ...65 November 2008 Part No 920559 Rev H INSTALLATION INSTRUCTION page 2 of 2 OVATION MODEL B23...
Page 74: ...68 Part No 920559 Rev H November 2008 INSTALLATION INSTRUCTION page 1 of 2 OVATION MODEL R11...
Page 75: ...69 November 2008 Part No 920559 Rev H INSTALLATION INSTRUCTION page 2 of 2 OVATION MODEL R11...
Page 76: ...70 November 2008 Part No 920559 Rev H...
Page 77: ...71 November 2008 Part No 920559 Rev H 2 7151 C TYPICAL SITE WIRING...
Page 78: ...72 Part No 920559 Rev H November 2008...
Page 80: ...74 Part No 920559 Rev H November 2008...
Page 81: ...75 November 2008 Part No 920559 Rev H APPENDIX D SITE INTERCONNECTION DIAGRAMS...
Page 82: ...76 Part No 920559 Rev H November 2008 Figure D 1 Backroom Installation Wayne Control System...
Page 84: ...78 Part No 920559 Rev H November 2008 Figure D 3 Pump Relay Installation Wiring Diagram...