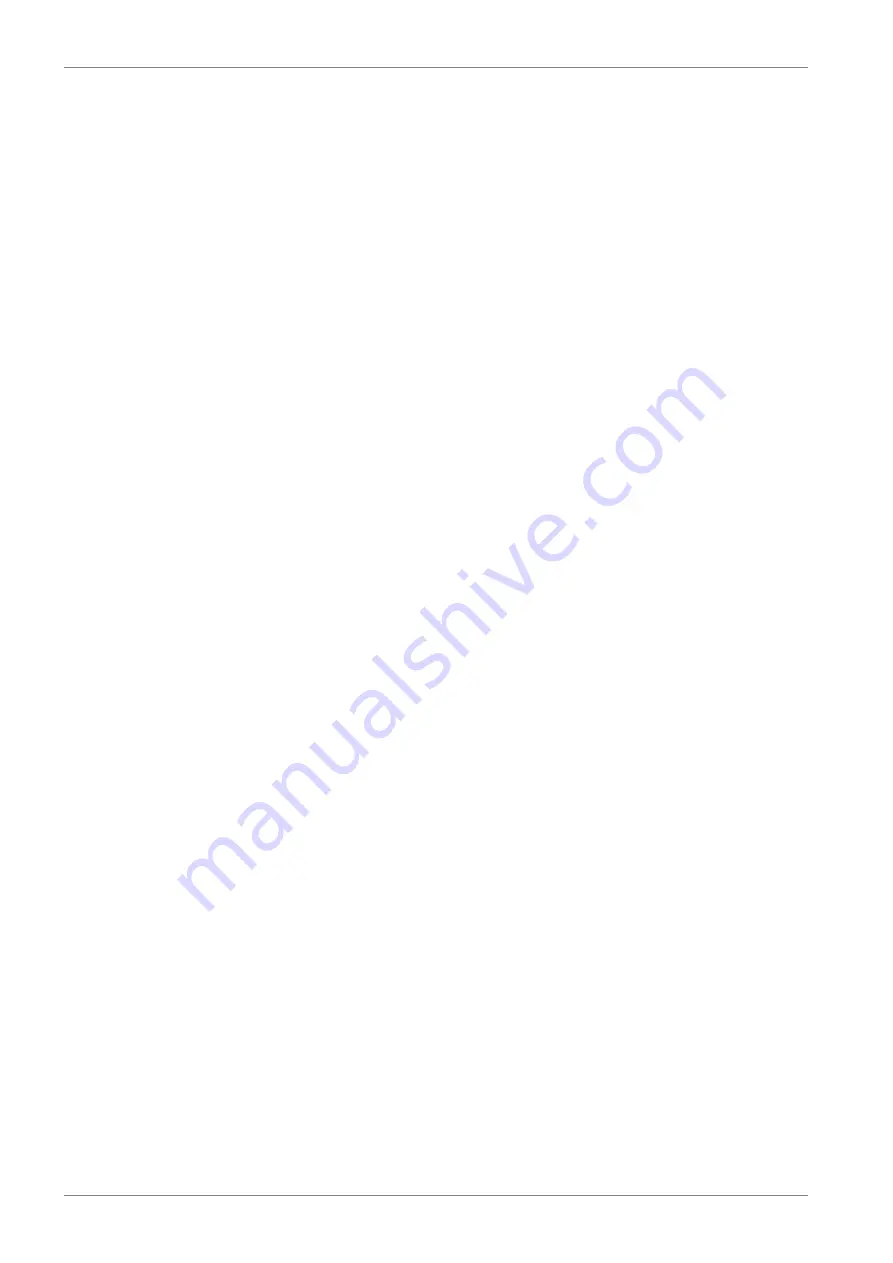
9.3.2
Sea water pump (4P11)
The sea water pumps are always separate from the engine and electrically driven.
The capacity of the pumps is determined by the type of coolers and the amount of heat to be
dissipated.
Significant energy savings can be achieved in most installations with frequency control of the
sea water pumps. Minimum flow velocity (fouling) and maximum sea water temperature (salt
deposits) are however issues to consider.
9.3.3
Temperature control valve for central cooler (4V08)
The temperature control valve is installed after the central cooler and it controls the temperature
of the LT water before the engine, by partly bypassing the cooler. The control valve can be
either self-actuated or electrically actuated. Normally there is one temperature control valve
per circuit.
The set-point of the control valve is 35 ºC, or lower if required by other equipment connected
to the same circuit.
9.3.4
Temperature control valve for heat recovery (4V02)
The temperature control valve after the heat recovery controls the maximum temperature of
the water that is mixed with HT water from the engine outlet before the HT pump. The control
valve can be either self-actuated or electrically actuated.
The set-point is usually somewhere close to 75 ºC.
The arrangement shown in the example system diagrams also results in a smaller flow through
the central cooler, compared to a system where the HT and LT circuits are connected in parallel
to the cooler.
9.3.5
Coolers for other equipment and MDF coolers
The engine driven LT circulating pump can supply cooling water to one or two small coolers
installed in parallel to the engine charge air and lubricating oil cooler, for example a MDF cooler
or a generator cooler. Separate circulating pumps are required for larger flows.
Design guidelines for the MDF cooler are given in chapter Fuel system.
9.3.6
Fresh water central cooler (4E08)
Plate type coolers are most common, but tube coolers can also be used. Several engines can
share the same cooler.
If the system layout is according to one of the example diagrams, then the flow capacity of
the cooler should be equal to the total capacity of the LT circulating pumps in the circuit. The
flow may be higher for other system layouts and should be calculated case by case.
It can be necessary to compensate a high flow resistance in the circuit with a smaller pressure
drop over the central cooler.
Design data:
see chapter Technical Data
Fresh water flow
see chapter Technical Data
Heat to be dissipated
max. 60 kPa (0.6 bar)
Pressure drop on fresh water side
acc. to cooler manufacturer, normally 1.2 - 1.5 x the fresh
water flow
Sea-water flow
acc. to pump head, normally 80 - 140 kPa (0.8 - 1.4 bar)
Pressure drop on sea-water side, norm.
9-14
DAAB605814
Wärtsilä 46F Product Guide
9. Cooling Water System
Summary of Contents for 46F Series
Page 1: ...Wärtsilä 46F PRODUCT GUIDE ...
Page 4: ...This page intentionally left blank ...
Page 8: ...This page intentionally left blank ...
Page 18: ...This page intentionally left blank ...
Page 86: ...This page intentionally left blank ...
Page 104: ...This page intentionally left blank ...
Page 154: ...This page intentionally left blank ...
Page 162: ...This page intentionally left blank ...
Page 170: ...This page intentionally left blank ...
Page 176: ...This page intentionally left blank ...
Page 194: ...This page intentionally left blank ...
Page 200: ...This page intentionally left blank ...
Page 202: ...This page intentionally left blank ...
Page 207: ...Fig 21 7 List of symbols DAAF406507 7 DAAB605814 21 5 21 ANNEX Wärtsilä 46F Product Guide ...