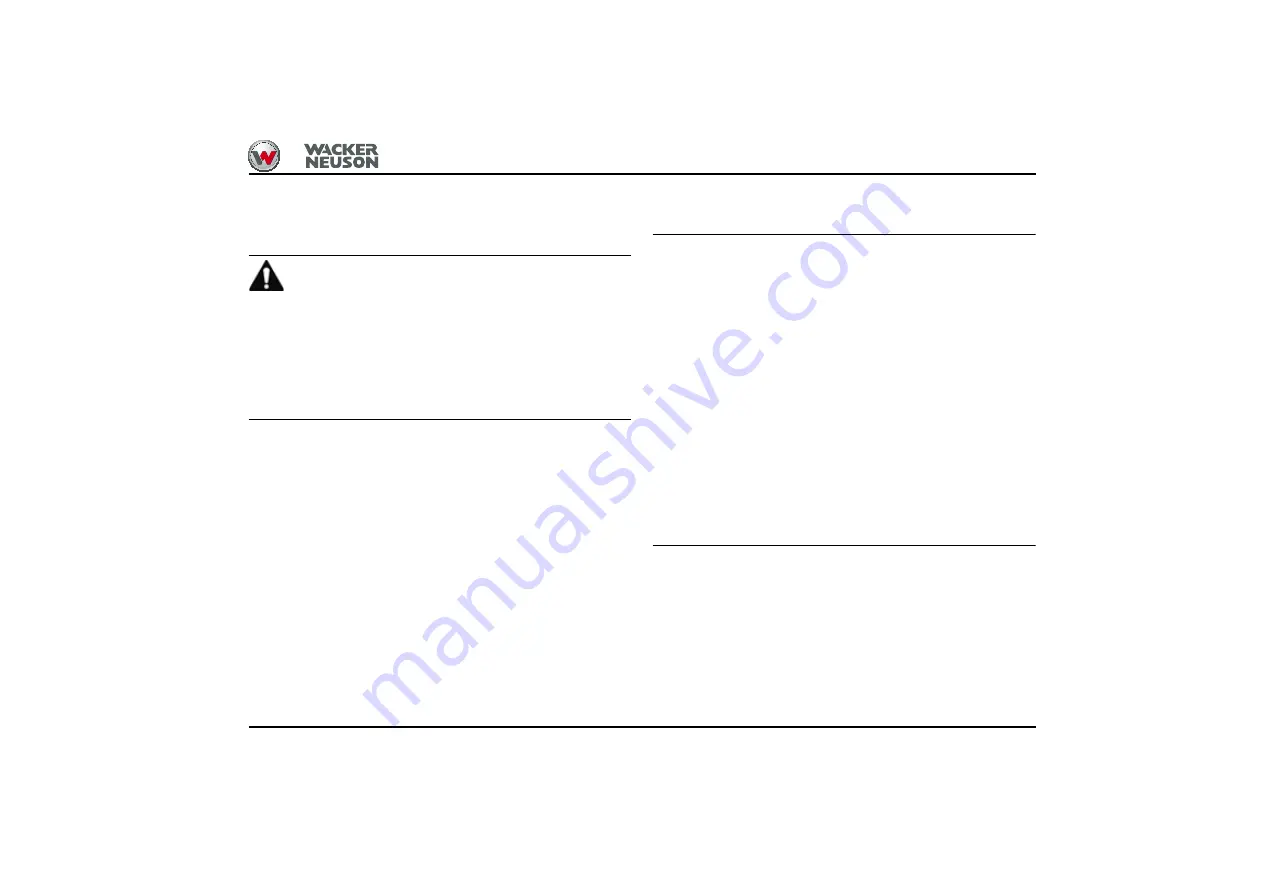
Maintenance 7
BA TH412 * 06/2017 * 4512_7-5_Reinigung_en.fm
7-23
7.5
Cleaning and maintenance
Information on cleaning and maintenance
CAUTION
Injury hazard due to a dirty machine!
A dirty machine can cause injury.
►
Follow the daily maintenance plan.
►
Remove dirt in particular from the handholds, footholds
and control elements.
NOTICE
Damage to machine due to cleaning work.
►
Pay attention to the lower side in particular when
cleaning the machine. Do not allow dirt to collect on
the engine or gearbox.
►
Ensure that the spaces between the radiator fins are
clean and not blocked.
►
Do not damage the radiator fins when cleaning with a
high-pressure cleaner.
►
Always cover the intake connection of the air filter
before washing the engine.
►
Do not clean sensitive electrical components
(instrument panel, alternator, compact connectors,
control levers, etc.) with a high-pressure cleaner.
Maintenance
Summary of Contents for Telehandler TH412
Page 1: ...Operator s manual Telehandler TH412...
Page 3: ...Legend Original Operator s Manual Version 1 3 Issue 06 2017 Document BA TH412...
Page 10: ...EG 2 BA TH412 06 2017 4512_0 1_Konform_en fm EG Declaration of conformity Notes...
Page 18: ...1 8 BA TH412 06 2017 4512_1 1_Vorwort_en fm 1 Preface Notes...
Page 46: ...2 28 BA TH412 06 2017 4512_2 1_Sicherheit_en fm 2 Safety Notes...
Page 271: ...Maintenance 7 BA TH412 06 2017 4512_7 1_Hinweise_en fm 7 17...
Page 319: ...Maintenance 7 BA TH412 06 2017 4512_7 16_Achsen_en fm 7 65 Fig 163 a b Fig 164 c...
Page 332: ...8 6 BA TH412 06 2017 4512_8_Stoerungen_en fm 8 Malfunctions Notes...
Page 345: ...Technical data 9 BA TH412 06 2017 4512_9_Tech_Daten_en fm 9 13 Load diagram Fig 170...
Page 354: ...9 22 BA TH412 06 2017 4512_9_Tech_Daten_en fm 9 Technical data Notes...
Page 360: ...S 6 BA TH412 06 2017 4512_SIX_en fm S Index...
Page 361: ......