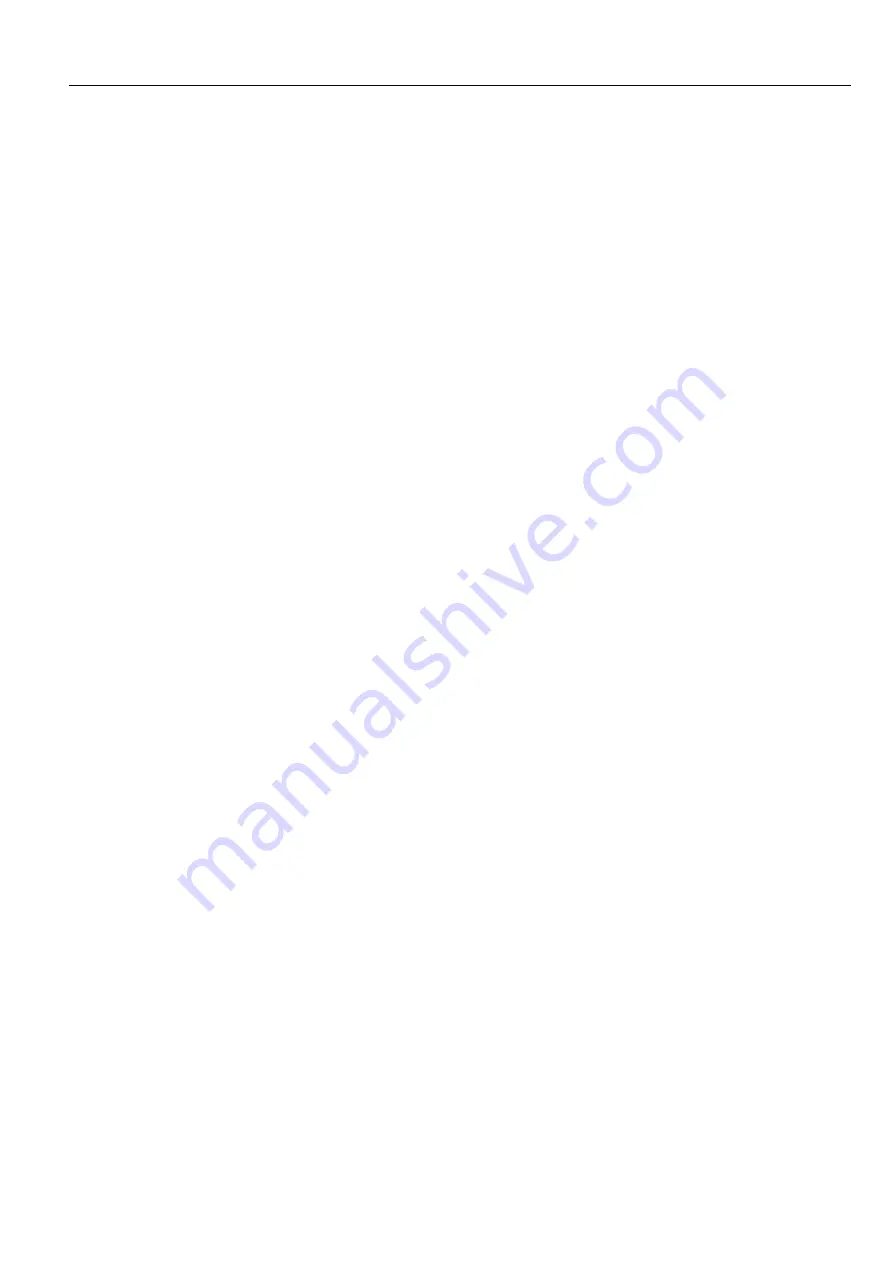
Rotary lobe pump
Operating instructions
VX100Q, VX136Q..QD..QDM2, VX186Q..QD..QDM2, VX230Q..QD
4/68
8.8
Change of wear plates ...................................................................................................................... 50
8.9
Change of cartridge mechanical seal ................................................................................................ 51
8.9.1
Change of cartridge mechanical seal on the gearbox ................................................................. 51
8.9.2
Cartridge mechanical seal change on the QD cover ................................................................... 53
8.10
Adjusting of pump housing segments .......................................................................................... 54
8.11
Reducing the starting torque ........................................................................................................ 55
9
Maintenance plan ................................................................................................................................. 57
10
Service plan .......................................................................................................................................... 58
11
Trouble-shooting .................................................................................................................................. 59
11.1
Troubleshooting ........................................................................................................................... 59
11.2
Help .............................................................................................................................................. 60
12
Specifications ....................................................................................................................................... 61
12.1
Material description for rotary lobes ............................................................................................ 61
12.2
VX100
– Technical data ............................................................................................................... 62
12.3
VX100 with flanged electric motor
– Technical data.................................................................... 62
12.4
VX136
– Technical data ............................................................................................................... 63
12.5
VX186
– Technical data ............................................................................................................... 63
12.6
VX230
– Specifications ................................................................................................................ 64
13
Long-term storage ................................................................................................................................ 65
14
Putting out of operation and disposal................................................................................................ 66
15
Declaration of Installation ................................................................................................................... 67
Table of figures
: Flow direction with motor drive
: Flow direction with PTO drive
: Flow direction with Marathon pumps
: Flow direction with pump units
: Flow direction with InjectionSystem
: Transport aids - pump type Q
: Transport aids - pump types QD and QDM2
........................................................................................ 15
: Transport aids - pump with flange-mounted electric motor
.................................................................. 16
: Transport aids - pump on base, type inline
........................................................................................ 16
: Transport aids - pump on base, type belt drive
.................................................................................. 16
: Pump with quenching fluid tank, without pressure valve
.................................................................... 28
: Pump with pressure valve, without buffer fluid tank
........................................................................... 29
: Installation example - dry buffer chamber
.......................................................................................... 31
: Gear oil change VX136, VX186, VX230
............................................................................................. 36
: Opening/Closing the QD cover
: Cleaning before QD cover assembly
: Rotary lobe change, Q series
: Position of pressure disc and spring washer
...................................................................................... 47
: Rotary lobe change, QD series
: Rotary lobe change, QDM2 series
: Installation position of the curved wear plates
.................................................................................... 50
: Cartridge mechanical seal on the gearbox
......................................................................................... 52
: Cartridge mechanical seal on the QD cover
....................................................................................... 53
: Adjustment of pump housing segments
............................................................................................. 54
Summary of Contents for VX Series
Page 1: ...Best Practices for Installation of VX Rotary Lobe Pumps WELCOME TO VOGELSANG FACTORY TRAINING ...
Page 15: ...Installation ...
Page 24: ...Pressurizing the Pump ...
Page 36: ...Direction of flow Startup Checklist Startup ...
Page 44: ......
Page 121: ...Service Manual Service Manual Pump Models VX Series Q Pumps ...
Page 122: ...Service Manual Service Manual Pump Models VX Series Q Pumps ...
Page 123: ...Service Manual Service Manual Pump Models VX Series Q Pumps ...