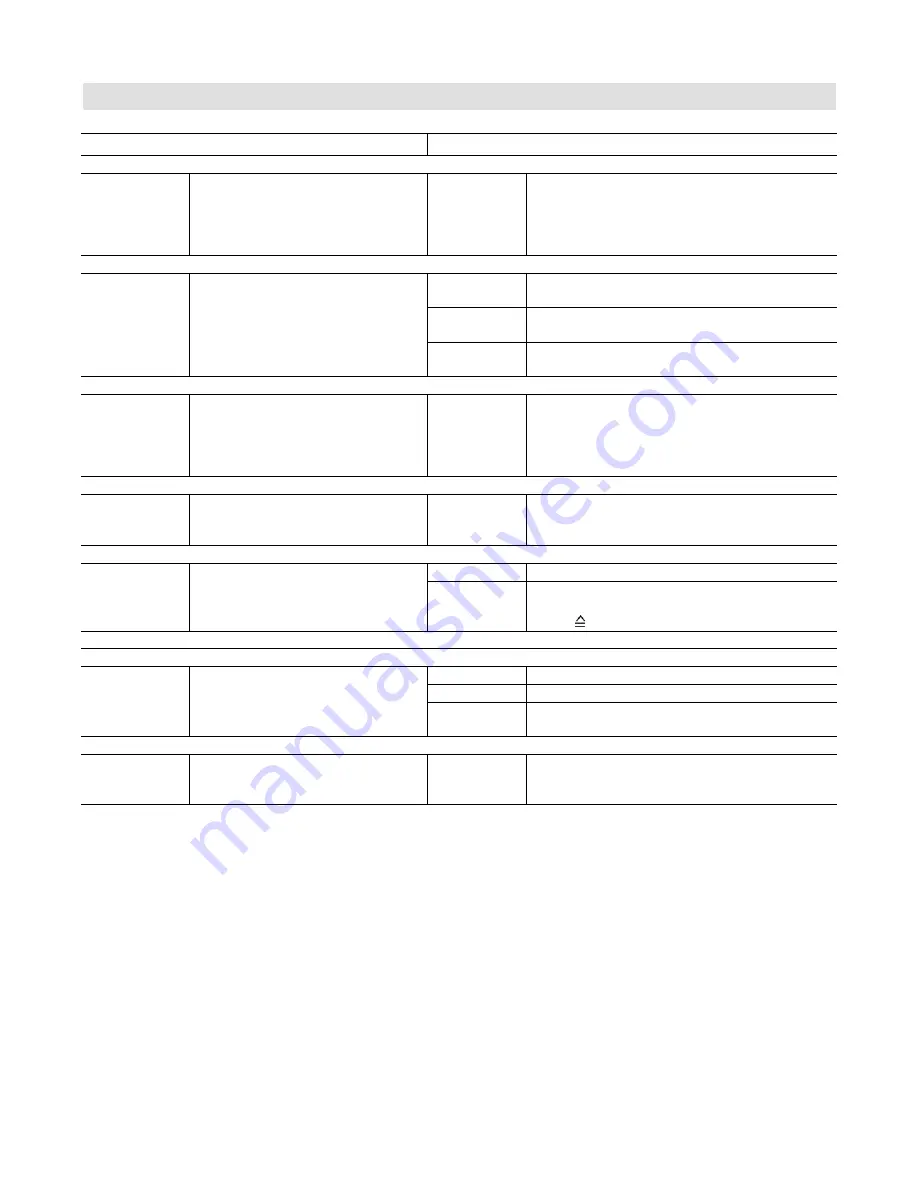
151
5790 733 - 07
Vitocrossal 300 CA3 Series 2.5 to 6.0 Installation/Service
Coding Level 2
“General” Group
(continued)
Coding in the factory set condition
Possible change
“With LON communication module”
79:1
Control unit is fault manager.
79:0
Control unit is not fault manager
IMPORTANT
Must be set for boiler section 2/boiler section 3,
see page 87.
“Central control of heating circuits”
7a:0
Without central control of heating
circuits.
7a:1
With central control Heating circuit without
mixing valve A1 (heating circuit 1).
7a:2
Heating circuit with mixing valve M2
(heating circuit 2).
7a:3
Heating circuit with mixing valve M3
(heating circuit 3).
“LON communication module: Time”
7b:1
Control unit transmits the time.
7b:0
No time transmission
IMPORTANT
Must be set for boiler section 2/boiler section 3,
see page 87.
“Detached house/apartment building”
7f:1
Detached house
7F:0
Apartment building
Separate adjustment of holiday program
and time program for DHW heating possible.
“Fault message”
80:6
A fault message is issued if a fault
occurs for at least 30 sec.
80:0
Immediate fault message.
80:2
to
80:199
Adjustable from
10 to 995 sec,
1 step 5 sec.
“Automatic summer/wintertime changeover”
81:1
Automatic summer/wintertime
changeover.
81:0
Manual summer/wintertime changeover
81:2
Do not adjust!
81:3
With LON communication module:
The control unit receives the time.
“Summer time starts: Month”
82:3
March
82:1
to
82:12
January to December