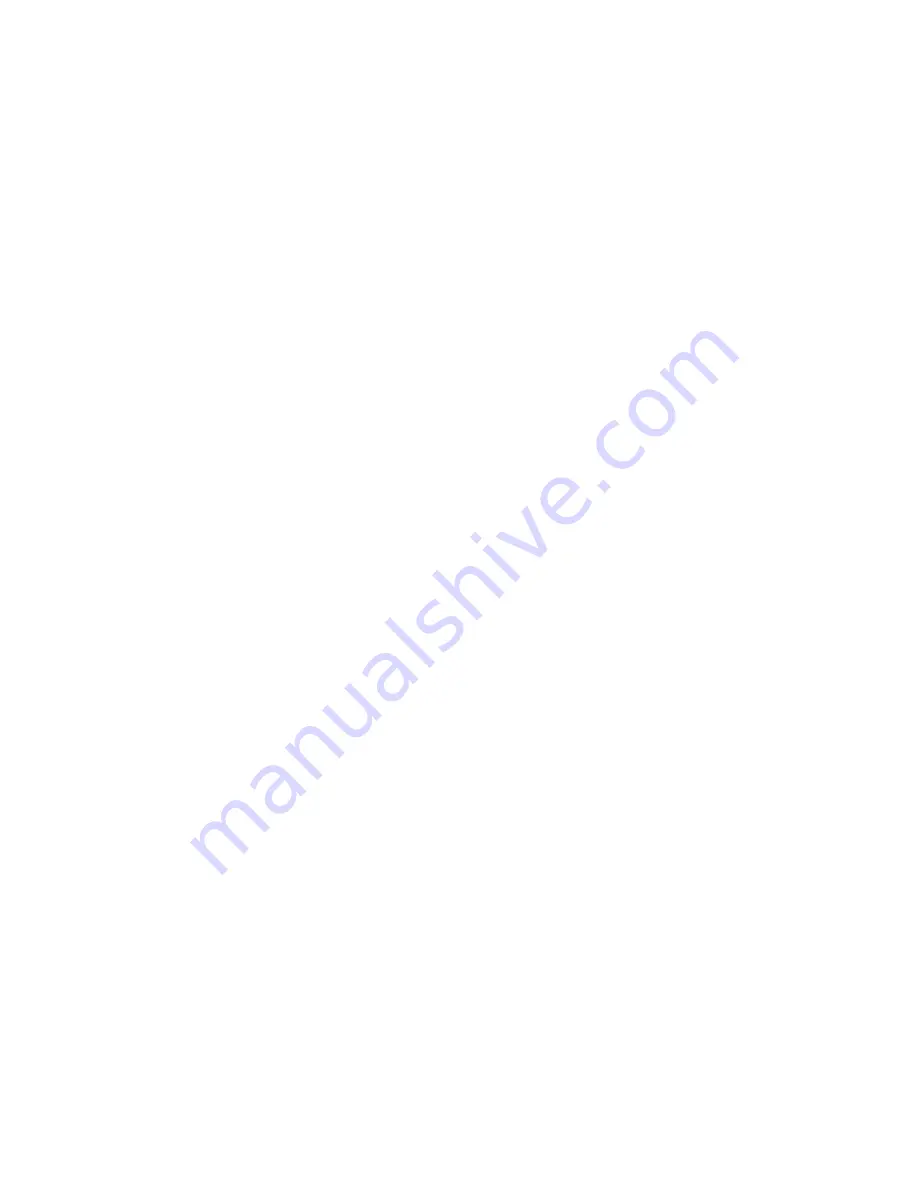
CONTENTS PAGE
INTRODUCTION.....................................................................................................................................4
PREPARING THE MOTORCYCLE FOR REPAIR................................................................................5
DETERMINING THE TECHNICAL CONDITION OF THE MOTORCYCLE....................................5
DISASSEMBLY AND REASSEMBLY..................................................................................................21
SERVICE AND REPAIR OF THE ENGINE...........................................................................................27
SERVICE AND REPAIR OF THE GEARBOX......................................................................................58
FINAL DRIVE AND DRIVE SHAFT REPAIR......................................................................................69
DISASSEMBLY AND REASSEMBLY OF THE FINAL DRIVE AND SIDECAR DRIVE................74
REPAIRING THE WHEELS....................................................................................................................81
REPAIRING THE FRONT FORKS.........................................................................................................85
INSPECTION AND REPAIR OF THE MOTORCYCLE FRAME.........................................................86
SUSPENSION SERVICE AND REPAIR.................................................................................................86
HANDLE BARS AND CONTROL CABLES..........................................................................................87
FUEL SYSTEM.........................................................................................................................................87
REPAIRING THE INTAKE AND EXHAUST........................................................................................88
SIDECAR REPAIR...................................................................................................................................88
ELECTRICAL EQUIPMENT...................................................................................................................88
BEARING LIST........................................................................................................................................97
SEAL AND O-RING LIST.......................................................................................................................99
Summary of Contents for 750cc Series
Page 1: ...Repair Manual 750cc All Models www imz ural com ...
Page 2: ......
Page 71: ...1 2 3 4 5 6 7 8 Fig 66 Final drive 71 ...
Page 98: ...Fig 11 iring Diagram 9 W 98 ...