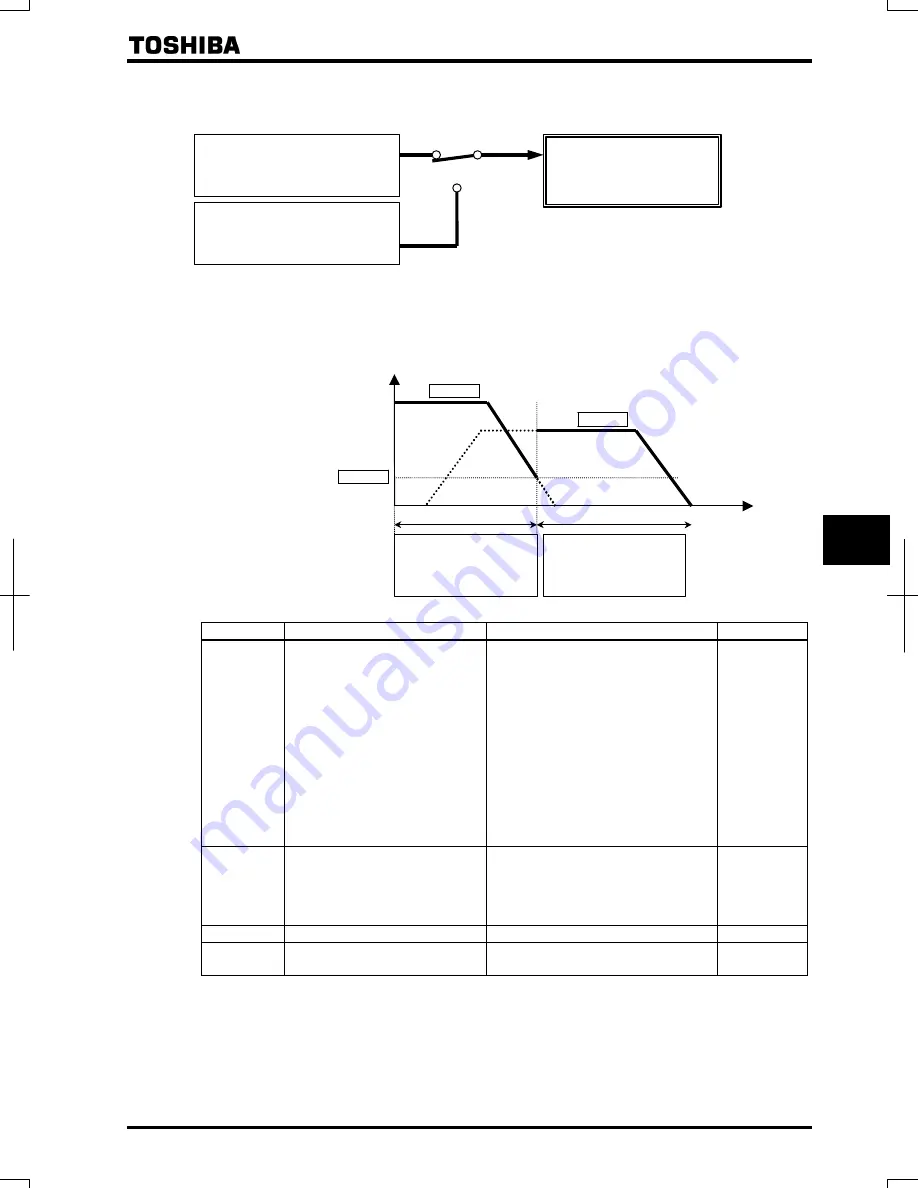
E6581531
F-11
6
2) Automatic switching by means of switching frequencies (
H
=
)
A
B
Command selected
with
HOQF
Command selected
with
H
Operation frequency
command
A: If the frequency set with
HOQF
is higher than that set with
H
························· Priority is given to the
command set with
HOQF
.
B: If the frequency set with
HOQF
is equal to or lower than that set with
H
········· Priority is given to the
command set with
H
.
H
Priority is given to
the command set
with
H
.
Priority is given to
the command set
with
HOQF
.
H
HOQF
Frequency setting signal
[ Parameter setting]
Title
Function
Adjustment range
Default setting
HOQF
Frequency setting mode selection 1
:VI/II (voltage/current input)
:RR/S4 (potentiometer/voltage input)
:RX (voltage input)
:Operation panel input enabled
(including LED/LCD option input)
:2-wire RS485 communication input
:4-wire RS485 communication input
:Communications option input
:Optional AI1 (differential current input)
:Optional AI2 (voltage/current input)
:Up/Down frequency
:Optional RP pulse input
:Optional high-speed pulse input
H
Frequency priority selection
:
HOQF
/
H
terminal switching
(input terminal function selection
,
)
:
HOQF
/
H
frequency switching
(switching with
H
)
H
Frequency setting mode selection 2
Same as
HOQF
(
~
)
H
Speed command priority switching
frequency
~
HJ
Hz