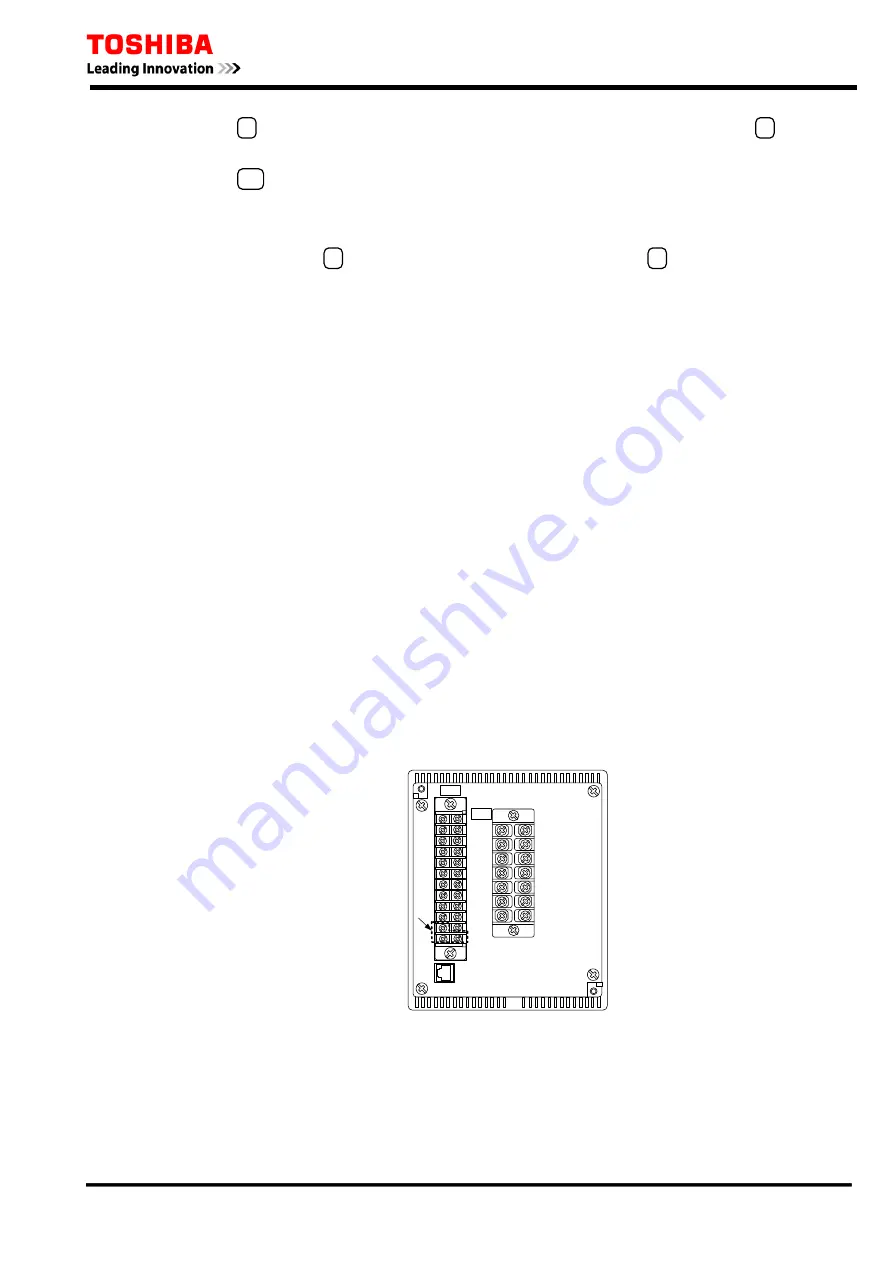
6 F 2 T 0 1 7 2
②
|
: Used for CB close operation. When CB is in the closed position, the
|
key
does not function
③
L/R
: Used for CB control hierarchy (local / remote) change.
CAUTION
The CB close control key
|
is linked to BO1 and the CB open control key
○
is linked to BO2,
when control function is enable.
USB connector
The USB connector is a B-type connector for connection with a local personal computer.
4.1.2 Communication Ports
The following three interfaces are mounted as communication ports:
•
USB port
•
RS485 port
•
Optional Communication Unit port
USB port
This connector is a standard B-type connector for USB transmission and is mounted on the front
panel. By connecting a personal computer to this connector, setting operation and display functions
can be performed.
RS485 port
The RS485 port is used for MODBUS communication or the IEC60870-5-103 communication to
connect between relays and to construct a network communication system.
The RS485 port is provided on the rear of the relay as shown in Figure 4.1.1.
TB2
TB1
RS485 Port
Figure 4.1.2 Location of Communication Port
Optional Fibre or Ethernet LAN port for model 402A and 422A
An optional Ethernet LAN port can be connected to substation automation system via an Ethernet
communication networks using the IEC 61850 protocol. 100Base-TX (T1: RJ-45 connector) for
Ethernet LAN is provided at the rear of the relay, as shown in Figure 4.1.3.
81
Summary of Contents for GRE110
Page 183: ...6 F 2 T 0 1 7 2 Appendix B Signal List 184 ...
Page 191: ...6 F 2 T 0 1 7 2 Appendix C Event Record Items 192 ...
Page 196: ...6 F 2 T 0 1 7 2 Appendix D Binary Output Default Setting List 197 ...
Page 199: ...6 F 2 T 0 1 7 2 Appendix E Relay Menu Tree 200 ...
Page 210: ...6 F 2 T 0 1 7 2 Appendix F Case Outline 211 ...
Page 211: ...6 F 2 T 0 1 7 2 Case Outline for model 400 401 420 421 820 and 821 212 ...
Page 212: ...6 F 2 T 0 1 7 2 Case Outline for model 402 and 422 213 ...
Page 213: ...6 F 2 T 0 1 7 2 Appendix G Typical External Connection 214 ...
Page 245: ...6 F 2 T 0 1 7 2 Appendix J Return Repair Form 246 ...
Page 249: ...6 F 2 T 0 1 7 2 Customer Name Company Name Address Telephone No Facsimile No Signature 250 ...
Page 250: ...6 F 2 T 0 1 7 2 Appendix K Technical Data 251 ...
Page 256: ...6 F 2 T 0 1 7 2 Appendix L Symbols Used in Scheme Logic 257 ...
Page 259: ...6 F 2 T 0 1 7 2 Appendix M Modbus Interoperability 260 ...
Page 289: ...6 F 2 T 0 1 7 2 Appendix N IEC60870 5 103 Interoperability 290 ...
Page 296: ...6 F 2 T 0 1 7 2 Appendix O PLC Default setting 297 ...
Page 298: ...6 F 2 T 0 1 7 2 Appendix P Inverse Time Characteristics 299 ...
Page 304: ...6 F 2 T 0 1 7 2 Appendix Q IEC61850 Interoperability 305 ...