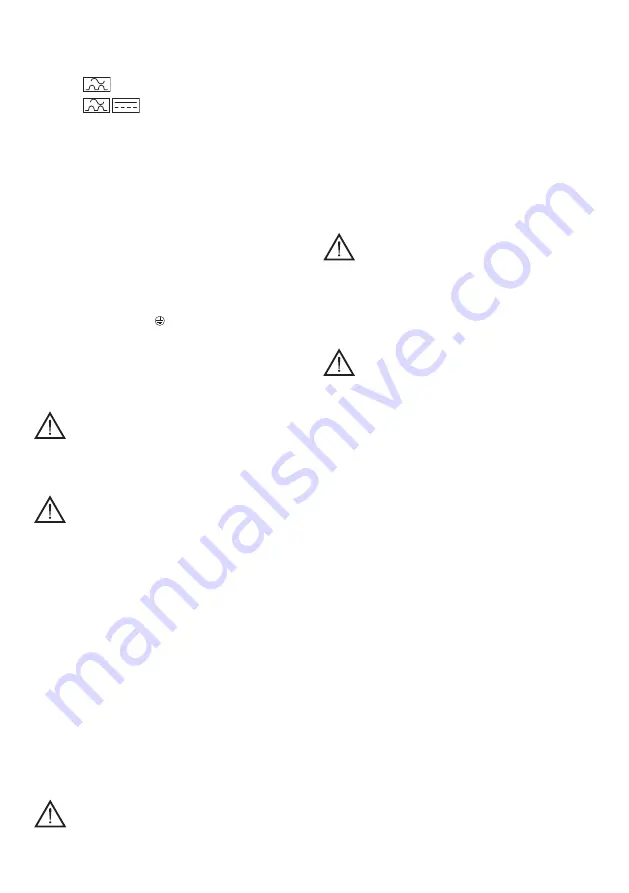
- 7 -
- The welding machine should only be connected to a power supply
system with the neutral conductor connected to earth.
- To ensure protection against indirect contact use residual current
devices of the following types:
- Type A (
) for single phase machines;
- Type B (
) for 3-phase machines.
- In order to satisfy the requirements of the EN 61000-3-11 (Flicker)
standard we recommend connecting the welding machine to the
interface points of the main power supply that have an impedance of
less than:
Zmax = 0.170 Ohm.
- the welding machine does not fall within the requisites of IEC/EN
61000-3-12 standard.
Should it be connected to a public mains system, it is the installer’s
responsibility to verify that the welding machine itself is suitable
for connecting to it (if necessary, consult the distribution network
company).
- Unless otherwise specified (MPGE), the welding machines are
compatible with power generating sets for voltage oscillations up to ±
15%.
For correct use, the power generating set must be brought to steady
conditions before being able to connect the inverter.
- PLUG AND OUTLET:
- The 230V model
is fitted at the factory with a power supply cable
and normalised plug, (2P +
) 16A/250V.
It can therefore be connected to a mains outlet fitted with fuses
or an automatic circuit-breaker; the special earth terminal should
be connected to the earth conductor (yellow-green) of the power
supply line.
Table
(TAB.1)
shows the recommended delayed fuse sizes in
amps, chosen according to the max. nominal current supplied by
the welding machine, and the nominal voltage of the main power
supply.
WARNING! Failure to observe the above rules will make the
(Class 1) safety system installed by the manufacturer ineffective with
consequent serious risks to persons (e.g. electric shock) and objects
(e.g. fire).
CONNECTION OF THE WELDING CABLES
WARNING! BEFORE MAKING THE FOLLOWING
CONNECTIONS MAKE SURE THE WELDING MACHINE IS SWITCHED
OFF AND DISCONNECTED FROM THE POWER SUPPLY OUTLET.
WELDING OPERATIONS
Gun connection
- Connect the 14 PIN connector of the gun to the specific socket of the
generator (
Fig. C-6
).
- Connect the gun cables to the generator using the specific male DINSE
and respecting the correct polarities (on “+” the red cable and “-” the
black cable).
Recommendations:
- Fully rotate the welding cable connectors in the fast coupling (if
present), to guarantee perfect electrical contact; on the contrary, the
connectors will overheat causing their rapid wear and loss of efficiency.
Consumable insertion and gun adjustment
- Insert the slotted washer (
Fig. E -1
) in the specific electrode holder (
Fig.
E-2
).
NB: If consumables are used other than the slotted washer, comply with
the instructions sheet attached to them.
- Loosen the ring nut in
Fig. F-1
and adjust the copper electrode as in
Fig. F-2
.
- Using the nut in
Fig. F-3
with a 17 hex key, adjust the stroke of the
slotted washer as in
Fig. F-4
: the stroke of the figure is measured by
manually withdrawing the electrode holder towards the gun.
ATTENTION:
- Adjust the stroke only if the factory settings are not satisfactory,
taking into consideration an excessive stroke causes the arc to
extinguish and too short a stroke will not strike the arc.
- Close the fastening ring nuts manually, do not use tools or clamps!
6. WELDING: PROCESS DESCRIPTION
- Position the gun perpendicular to the sheet metal to spot weld and
exert a light force to loosen the end of the electrode with the tip of the
consumable (
Fig. G-1
).
- Press and release the trigger, while keeping the gun pressed on the
sheet metal (
Fig. H
): in a few fractions of a second, the arc strikes and a
slight recoil generates in the gun.
- When complete, lift the gun perpendicularly, removing the consumable
which remains welded on the sheet metal.
Recommendations for a good result
- Keep the surfaces to weld clean.
- Keep the end of the copper electrode clean.
- Keep the end of the consumable to weld pointed.
7. MAINTENANCE
WARNING! BEFORE CARRYING OUT MAINTENANCE
OPERATIONS MAKE SURE THE WELDING MACHINE IS SWITCHED OFF
AND DISCONNECTED FROM THE MAIN POWER SUPPLY.
EXTRAORDINARY MAINTENANCE
EXTRAORDINARY MAINTENANCE MUST ONLY BE CARRIED OUT BY
TECHNICIANS WHO ARE EXPERT OR QUALIFIED IN THE ELECTRIC-
MECHANICAL FIELD, AND IN FULL RESPECT OF THE IEC/EN 60974-4
TECHNICAL DIRECTIVE.
WARNING! BEFORE REMOVING THE WELDING MACHINE
PANELS AND WORKING INSIDE THE MACHINE MAKE SURE THE
WELDING MACHINE IS SWITCHED OFF AND DISCONNECTED FROM
THE MAIN POWER SUPPLY OUTLET.
If checks are made inside the welding machine while it is live, this
may cause serious electric shock due to direct contact with live parts
and/or injury due to direct contact with moving parts.
- Inspect the welding machine regularly, with a frequency depending
on use and the dustiness of the environment, and remove the dust
deposited on the transformer, reactance and rectifier using a jet of dry
compressed air (max. 10bar).
- Do not direct the jet of compressed air on the electronic boards; these
can be cleaned with a very soft brush or suitable solvents.
- At the same time make sure the electrical connections are tight and
check the wiring for damage to the insulation.
- At the end of these operations re-assemble the panels of the welding
machine and screw the fastening screws right down.
- Never, ever carry out welding operations while the welding machine is
open.
- After having carried out maintenance or repairs, restore the connections
and wiring as they were before, making sure they do not come into
contact with moving parts or parts that can reach high temperatures.
Tie all the wires as they were before, being careful to keep the high
voltage connections of the primary transformer separate from the low
voltage ones of the secondary transformer.
Use all the original washers and screws when closing the casing.
8. TROUBLESHOOTING
IN THE EVENT OF UNSATISFACTORY OPERATION, AND BEFORE CARRYING
OUT THE MOST SYSTEMATIC CHECKS OR CONTACTING YOUR SUPPORT
CENTRE, CHECK:
- The welding current, adjusted using the potentiometer with reference
to the graduated scale in amperes, is adequate for the type of
consumable used.
- With the main switch “ON”, the relevant light is on; on the contrary,
the defect normally lies on the power line (cables, socket and/or plug,
fuses, etc.).
- The yellow led is not on, signalling intervention of the safety thermal
switch or short circuit.
- Ensure you have observed the nominal duty cycle ratio; in the event
of intervention of the thermostatic protection, wait for the welding
machine to cool naturally, check the fan is working.
- Check the line voltage: if the value is too high or too low, the welding
machine remains blocked.
- Check there is no short circuit on welding machine output: in this case,
Summary of Contents for 954677
Page 81: ...81 6 G 1 H 7 IEC EN 60974 4 max 10 bar 8 ON...
Page 84: ...84 6 G 1 H 7 IEC EN 60974 4 10 8 ON...
Page 86: ...86 FIG C FIG D 1 5 6 2 3 4 1 2...
Page 87: ...87 FIG E FIG F 1 2 2mm 1 2 2mm 3 4...
Page 88: ...88 FIG G FIG H 1 2...