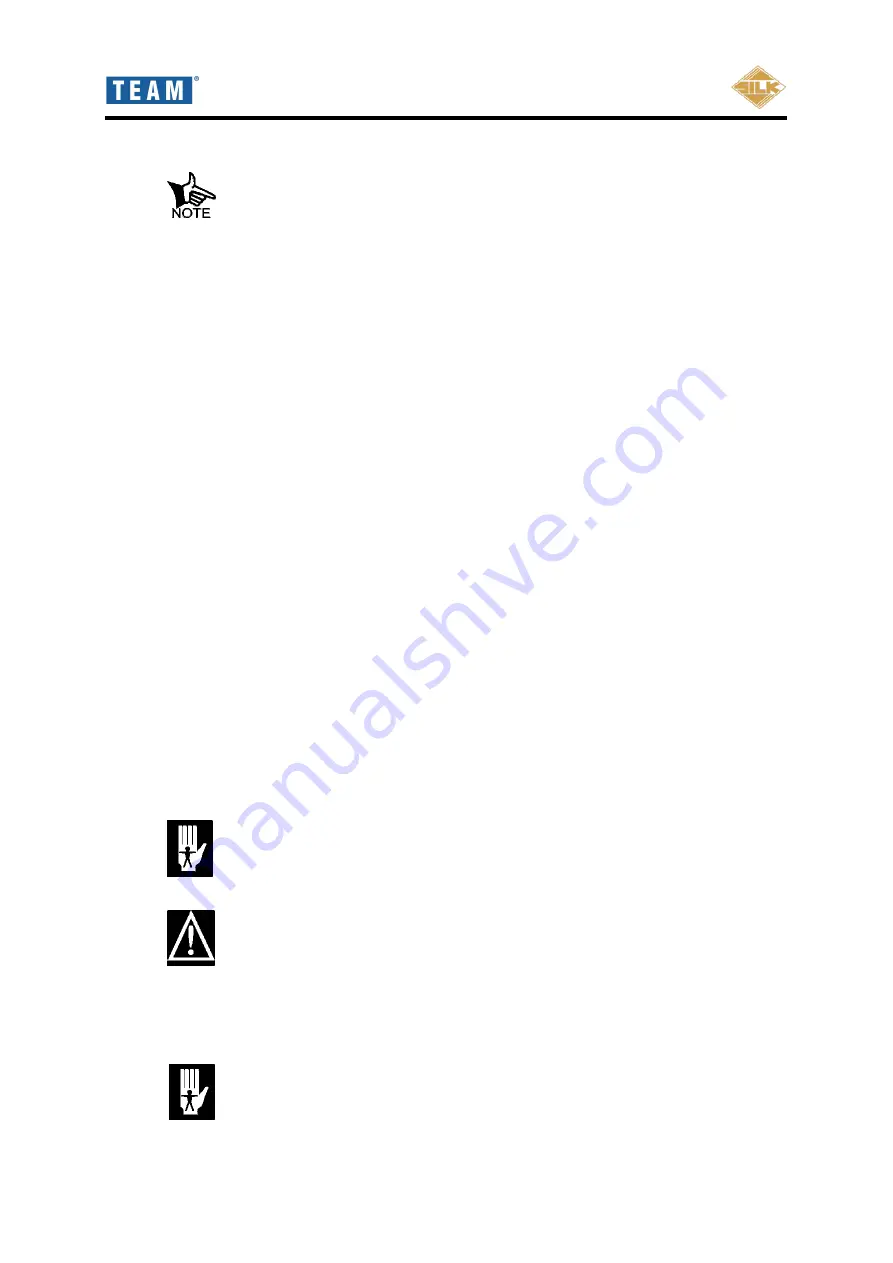
AX14-60 Flange Facing Machine
30
During centralising ensure that the setting straps are fitted. When centralised, the
base should be tight enough within the bore to support its own weight and that of
the turntable assembly.
6. When the base assembly is correctly positioned within the bore, evenly tighten
the remaining 4 non-adjustable ram bolts. Take care not to move the base
assembly out of position.
7. Care must be taken not to over tighten the jaw assemblies as it is possible for
them to distort the base assembly, flange or pipe.
8. Remove the centralising assembly from the mounting base assembly.
5.2.4
Levelling the base within the bore
1. Replace the spike on the clocking arm with a dial test indicator (DTI)
and
manually rotate the arm to clock the flange surface. Make a note of the reading
at the highest point (datum level) and at the lowest point. Using the jaw height
adjuster adjust the jaw nearest the lowest point first. Turn clockwise to raise the
base, adjust the other two jaws until the clock reaches the highest reading
(datum level) at all points. Re-clock the face to ensure a constant reading.
When achieved the base will be parallel to the flange.
2. Recheck that the base is tight enough within the flange and that it is capable of
supporting its own weight and that of the drive hub assembly. Remove the
clocking tower and the four support setting brackets.
3. Finally, secure the four remaining non-adjustable ram bolt assemblies into
position. Do not over tighten as it is possible to distort the base or work piece.
5.2.5
Machine installation
THE MACHINE WEIGHS 85KG. USE A MECHANICAL LIFTING DEVICE.
WHEN SETTING UP THE MACHINE ON A VERTICAL FLANGE THE
LIFTING HOOK SHOULD BE LEFT ON UNTIL THE MACHINE IS FULLY
SECURED.
CARE MUST BE TAKEN TO ENSURE THAT THE LIFTING EQUIPMENT
DOES NOT OBSTRUCT THE ROTATION OF THE MACHINE DURING THE
INSTALLATION
1. Determine if the fall-stop kit is needed (refer to Appendix E).
FAILURE TO FIT THE FALL-STOP KIT OR A SIMILAR DEVICE COULD
RESULT IN SERIOUS INJURY TO PEOPLE OR DAMAGE TO PLANT &
EQUIPMENT.
Summary of Contents for SILK AX14-60
Page 6: ...AX14 60 Flange Facing Machine 5 Fig 1 AX14 60 Flange Facing Machine main assembly...
Page 38: ...AX14 60 Flange Facing Machine 37 Fig 23 Tool post movement UP DOWN Toolpost...
Page 52: ...AX14 60 Flange Facing Machine 51 Fig 29 Main drive assembly sheet 1...
Page 53: ...AX14 60 Flange Facing Machine 52 Fig 30 Main drive assembly sheet 2...
Page 56: ...AX14 60 Flange Facing Machine 55 Fig 31 Surfacing arm assembly...
Page 58: ...AX14 60 Flange Facing Machine 57 Fig 32 Gearbox assembly...
Page 61: ...AX14 60 Flange Facing Machine 60 Fig 33 Base assembly sheet 1...
Page 62: ...AX14 60 Flange Facing Machine 61 Fig 34 Base assembly sheet 2...
Page 64: ...AX14 60 Flange Facing Machine 63 Fig 35 Toolpost assembly...
Page 66: ...AX14 60 Flange Facing Machine 65 Fig 36 Base centraliser...
Page 68: ...AX14 60 Flange Facing Machine 67 Fig 37 Counter balance...
Page 71: ...AX14 60 Flange Facing Machine 70 TYPES OF TOOL BIT FOR GENERAL PURPOSE AND FINE FINISH...
Page 72: ...AX14 60 Flange Facing Machine 71 TOOLS FOR V GROOVE PLUNGE MACHINING...
Page 76: ...AX14 60 Flange Facing Machine 75 APPENDIX C V GROOVE MEASUREMENT...
Page 77: ...AX14 60 Flange Facing Machine 76...
Page 78: ...AX14 60 Flange Facing Machine 77 APPENDIX D AIR MOTOR MANUFACTURERS INFORMATION...
Page 79: ...AX14 60 Flange Facing Machine 78...
Page 80: ...AX14 60 Flange Facing Machine 79...
Page 81: ...AX14 60 Flange Facing Machine 80...
Page 82: ...AX14 60 Flange Facing Machine 81...
Page 83: ...AX14 60 Flange Facing Machine 82...
Page 90: ...AX14 60 Flange Facing Machine 89 APPENDIX F BEARING LUBRICATION RU40035UU...
Page 91: ...AX14 60 Flange Facing Machine 90 APPENDIX G UKCA DECLARATION OF CONFORMITY...
Page 92: ...AX14 60 Flange Facing Machine 91 APPENDIX H CE DECLARATION OF CONFORMITY...