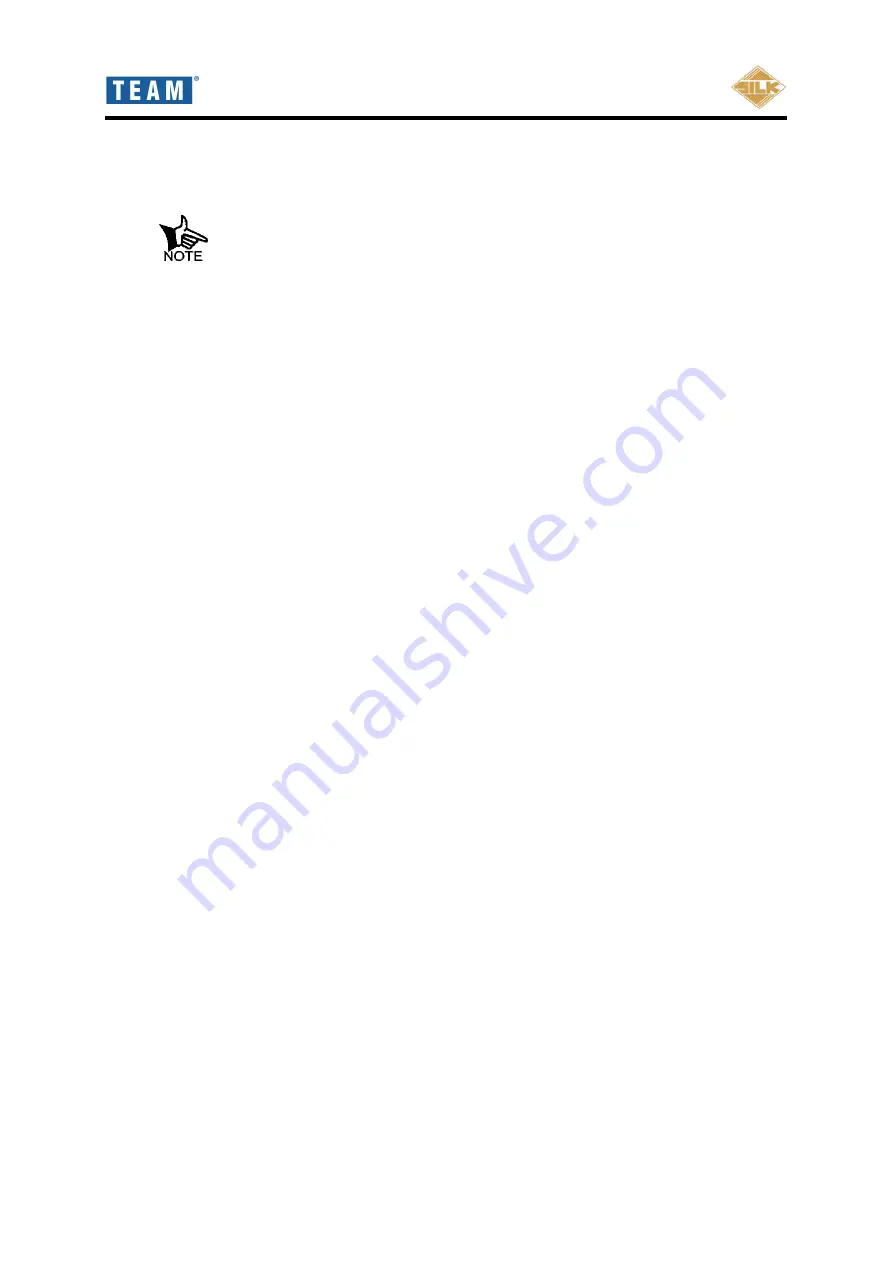
AX14-60 Flange Facing Machine
46
7.4.3
Removal of gearbox
Removing the gearbox can be made easier with the surfacing arm removed (see
section 7.4.2) but it is not essential to the operation
To remove:
1. Observe all Warnings and Cautions; refer to sections 3.1 and 7.4.
2. Push both selectors on the gearbox fully in i.e. the direction selector to the
'OUT' position and the feed selector to the
‘N’ position (see Fig. 9).
3. Remove the surfacing arm. This may be left in position but removal will make
the task easier.
4. Remove 4 off M10 cap head screws from gearbox housing.
5. Firmly grip the gearbox in your right hand, ensuring the keeper plate is secured
into the gearbox as this prevents the output shaft from pulling out of the
gearbox as it is eased away from the hub. Do not allow the traverse direction
selector to pull out of its position or this may result in the spring loaded drive
key being lost or displaced.
6. Draw the gearbox assembly off the location dowels and clear of the input and
output support bushes.
7. Place in a clean safe location.
8. If the drive key becomes displaced it will be necessary to remove the selector
shaft and gears. To do this remove the black anodised handle and securing
nuts, remove the keeper plate and securing screw before withdrawing the shaft
from the gearbox (consult the gearbox drawing in parts list) and locate the drive
key. Inspect the springs and replace if any damage is visible.
To refit
To refit follow the removal procedure above in reverse. Do not forget the gear
selector shaft stop sleeve. When inserting the sub-assembly into the gearbox
rotate the gears on the shaft to allow them to mesh more easily. Refit the keeper
plate and securing screw.
7.4.4
Replacement of shear pins
To replace either shear pin follow the procedure:
1. Remove the gearbox as described in section 7.4.3. The shear pins will be
found in the worm shaft and in the output shaft.
2. To replace a broken shear pin in the worm shaft unscrew the three retaining
screws and remove the bearing cap.
3. Withdraw the worm shaft, drift out the broken pin and refit a new shear pin.
Ensure the broken sections of the original shear pin are removed from the
gearbox and check grease for contamination and foreign elements.
Summary of Contents for SILK AX14-60
Page 6: ...AX14 60 Flange Facing Machine 5 Fig 1 AX14 60 Flange Facing Machine main assembly...
Page 38: ...AX14 60 Flange Facing Machine 37 Fig 23 Tool post movement UP DOWN Toolpost...
Page 52: ...AX14 60 Flange Facing Machine 51 Fig 29 Main drive assembly sheet 1...
Page 53: ...AX14 60 Flange Facing Machine 52 Fig 30 Main drive assembly sheet 2...
Page 56: ...AX14 60 Flange Facing Machine 55 Fig 31 Surfacing arm assembly...
Page 58: ...AX14 60 Flange Facing Machine 57 Fig 32 Gearbox assembly...
Page 61: ...AX14 60 Flange Facing Machine 60 Fig 33 Base assembly sheet 1...
Page 62: ...AX14 60 Flange Facing Machine 61 Fig 34 Base assembly sheet 2...
Page 64: ...AX14 60 Flange Facing Machine 63 Fig 35 Toolpost assembly...
Page 66: ...AX14 60 Flange Facing Machine 65 Fig 36 Base centraliser...
Page 68: ...AX14 60 Flange Facing Machine 67 Fig 37 Counter balance...
Page 71: ...AX14 60 Flange Facing Machine 70 TYPES OF TOOL BIT FOR GENERAL PURPOSE AND FINE FINISH...
Page 72: ...AX14 60 Flange Facing Machine 71 TOOLS FOR V GROOVE PLUNGE MACHINING...
Page 76: ...AX14 60 Flange Facing Machine 75 APPENDIX C V GROOVE MEASUREMENT...
Page 77: ...AX14 60 Flange Facing Machine 76...
Page 78: ...AX14 60 Flange Facing Machine 77 APPENDIX D AIR MOTOR MANUFACTURERS INFORMATION...
Page 79: ...AX14 60 Flange Facing Machine 78...
Page 80: ...AX14 60 Flange Facing Machine 79...
Page 81: ...AX14 60 Flange Facing Machine 80...
Page 82: ...AX14 60 Flange Facing Machine 81...
Page 83: ...AX14 60 Flange Facing Machine 82...
Page 90: ...AX14 60 Flange Facing Machine 89 APPENDIX F BEARING LUBRICATION RU40035UU...
Page 91: ...AX14 60 Flange Facing Machine 90 APPENDIX G UKCA DECLARATION OF CONFORMITY...
Page 92: ...AX14 60 Flange Facing Machine 91 APPENDIX H CE DECLARATION OF CONFORMITY...