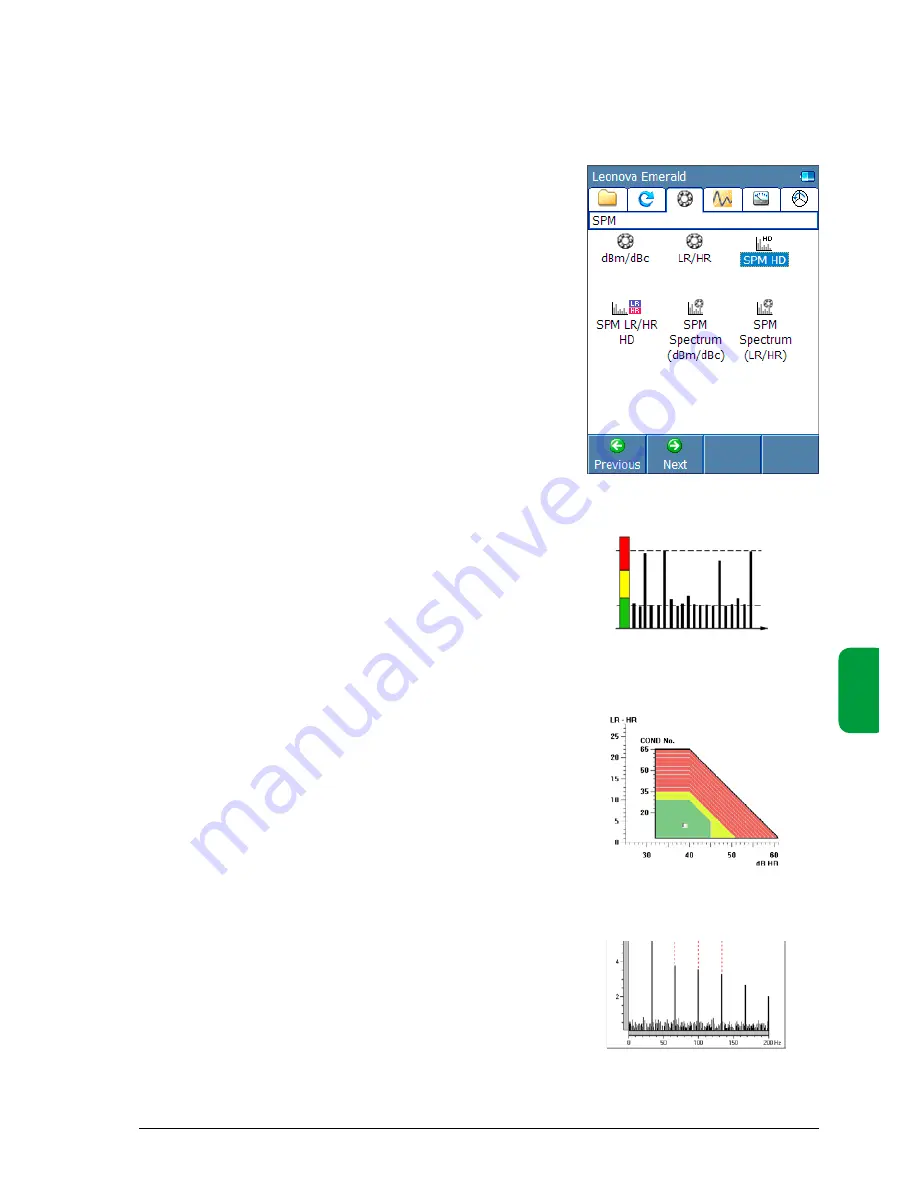
Shock pulse measurement
D:3
D
Shock pulse techniques
SPM HD
Shock pulse magnitude is quantified on a decibel scale by two
values, the maximum value
HDm
and the carpet value
HDc
.
The input data are very simple: the rpm and the bearing’s shaft
diameter. The maximum value HDm is evaluated on a green -
yellow - red condition scale. It indicates the bearing’s operating
conditions in terms of good - caution - bad. Operating condition
includes factors like installation quality, load, lubrication and the
mechanical state of the bearing surfaces.
In Time signal HD, repetitive shocks are enhanced and random
signals supressed using advanced digital algorithms. The Time
Signal HD is extremely useful to determine the location of a
possible bearing damage. The SPM Spectrum HD, obtained by
applying FFT algorithms on the Time Signal HD, is useful for
trending purposes (applying symptom and band values).
SPM dBm/dBc
With the dBm/dBc technique, the shock pulse magnitude is
quantified on a decibel scale by the maximum value
dBm
and
the carpet value
dBc
.
SPM LR/HR and LR/HR HD
Shock pulse magnitude is quantified on a decibel scale by the
values
LR
(low rate of occurrence, corresponding to the HDm) and
HR
(high rate of occurrence, similar to the HDc). In addition to
these ‘raw values’, the bearing’s operating condition is indicated
by the evaluation results CODE (overall condition), LUB (oil film
thickness) and COND (mechanical state of the surfaces). Thus,
condition information is more detailed, with emphasis on bearing
lubrication. The basic principles for LR/HR and LR/HR HD are the
same; however LR/HR HD utilizes the SPM HD algorithms for time
signals and spectrums. Both methods are most advantageous
for RPMs above 500.
The required input data are also more detailed: the rpm, the
bearing’s mean diameter and its type number. The type number
defines the bearing geometry and thus the evaluation box with
its green - yellow - red condition zones.
For all three techniques, measuring results indicating bad bearing
condition should be verified. By comparing shock values on and
around the bearing housing and through lubrication tests, the
operator can make sure that the measured shock pulses originate
from the bearing before taking corrective action. This verification
process is greatly simplified with the SPM Spectrum technique.
SPM Spectrum
A time record of the shock signal is subjected to an FFT. Prominent
bearing patterns in the resulting spectrum are conclusive evidence
that the measured shocks are generated by the bearing. Thus,
the bearing condition data obtained with either the dBm/dBc or
the LR/HR method are valid.
TYPE 3
HDm
HDc
Summary of Contents for leonova emerald
Page 1: ...User guide PORTABLE EFFICIENCY ...
Page 2: ......
Page 6: ...A 2 General instrument functions A ...
Page 36: ...B 2 General measurement functions B ...
Page 74: ...C 2 Measurement techniques always included B C ...
Page 88: ...D D 2 Shock pulse measurement ...
Page 122: ...D D 36 Shock pulse measurement ...
Page 124: ...E E 2 Vibration measurement ...
Page 150: ...E E 28 Vibration measurement ...
Page 152: ...F F 2 Rotor balancing ...
Page 170: ...F F 20 Rotor balancing ...