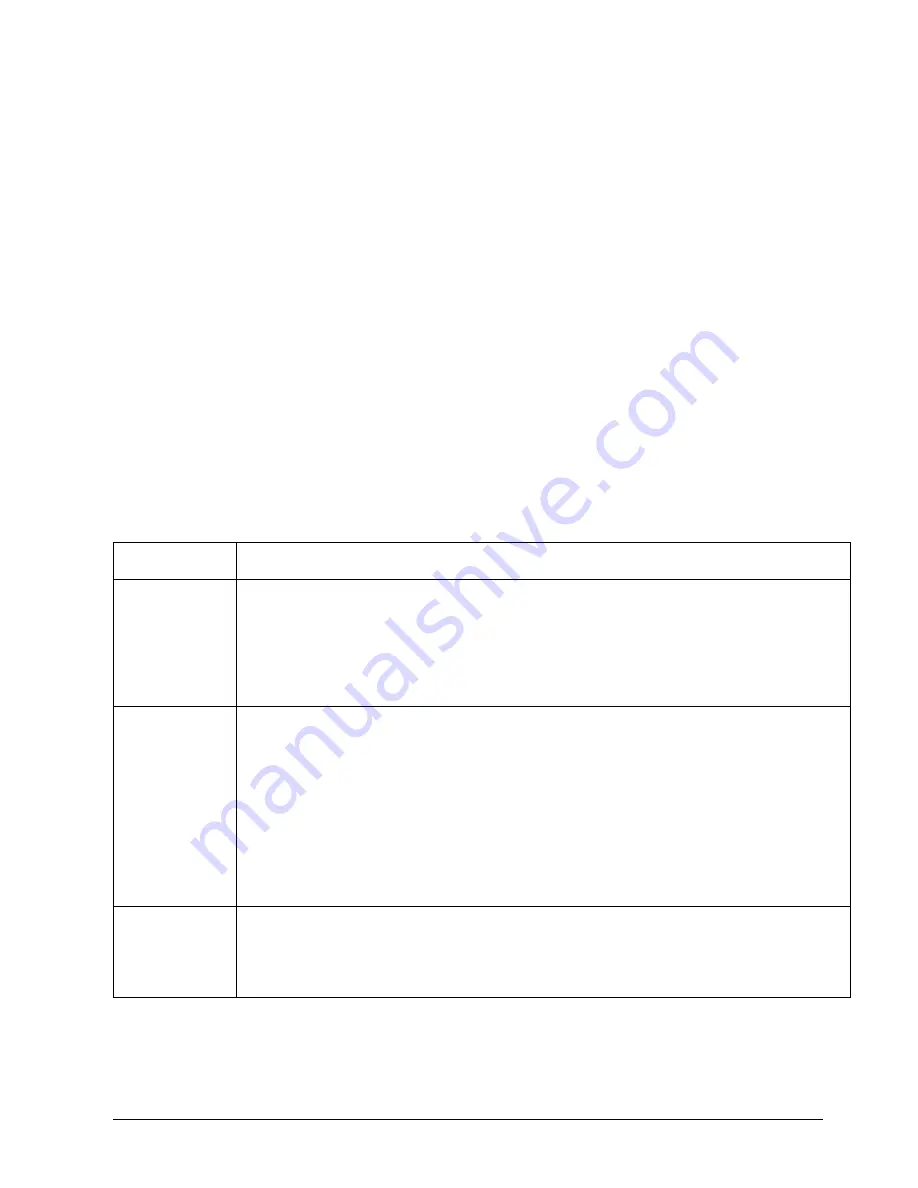
137
Southwestern Industries, Inc.
TRAK
2
OP
M11 Installation, Maintenance, Service, & Part List Manual
7.2 Backlash Compensation
Every mechanical system has at least a little backlash or lost motion. It is produced by the small
amount of play between the mechanical components, and mostly by the accumulative bending or
elasticity of all the parts of the drive train under load. The backlash constants are factory set, but
may need to be adjusted periodically. These are set at the factory by running a ballbar test using a
Reinshaw probe. If a ballbar is not available, then the following procedure will work.
1.
Set a .0001-inch dial indicator in the spindle, and touch off on a block or the vise along the
direction (X, Y or Z) you wish to check.
2.
The backlash can also be found manually with a 0.0001” indicator with the following method.
3.
Load the indicator to zero from one direction and zero out the DRO.
4.
Move the indicator to 0.002” and then back to zero. Do not over shoot 0, otherwise start over.
5.
Whatever number appears on the screen is the backlash value.
6.
Enter this value into service code 128.
7.
After entering this number, redo the process. The DRO and indicator should now both read 0.
Typical values for backlash should be 0.002
” or less. Most
new machines will exhibit
a 0.001” or less.
Larger values could mean the machine has a mechanical problem.
7.3 Periodic Maintenance
The following table lists the periodic maintenance that must be done on a daily, month(s) and yearly
basis.
Maintenance
Time Period
Items
Daily
1.
Remove majority of chips from around the axis slide ways, work table and ways
covers, especially between table and ATC.
2.
Empty chip tray.
3.
Visually check lubrication pump oil level, make sure it is always above the minimum
line.
4.
Visual check the coolant level, add if needed.
5.
Visually check the air supply filter.
Month(s)
1.
Remove back ATC and Y axis motor compartment access covers and clean chips and
any other debris. Cleanup any oil or coolant accumulated on the bottom panel of the
machine base. There is a drain plug at the rear of the machine to drain any fluids.
2.
Visually inspect the condition of way and ballscrew covers, clean if showing chip build
up.
3.
Check and if needed replace the air regulator filter element.
4.
Remove all air filters in the electrical cabinet and transformer enclosure every 2
months and clean.
5.
Every 2 months, drain and remove the coolant tank and clean inside, including the
pump screen. Fill with new coolant.
6.
Visually check the tool unclamp oil reservoir level.
Yearly
1.
Check backlash on each axis and adjust as necessary.
2.
Remove all covers and clean chips and debris that may have built up.
3.
Inspect the tool change air cylinder and grease the ATC linear rail bearing blocks.
4.
Inspect machine for any unusual wear and play, check cables and pneumatic lines for
any excessive abrasions or cuts.
Summary of Contents for TRAK 2OP M11
Page 6: ...3 Southwestern Industries Inc TRAK 2 OP M11 Installation Maintenance Service Part List Manual...
Page 7: ...4 Southwestern Industries Inc TRAK 2 OP M11 Installation Maintenance Service Part List Manual...
Page 8: ...5 Southwestern Industries Inc TRAK 2 OP M11 Installation Maintenance Service Part List Manual...
Page 12: ...9 Southwestern Industries Inc TRAK 2 OP M11 Installation Maintenance Service Part List Manual...
Page 71: ...68 Southwestern Industries Inc TRAK 2 OP M11 Installation Maintenance Service Part List Manual...