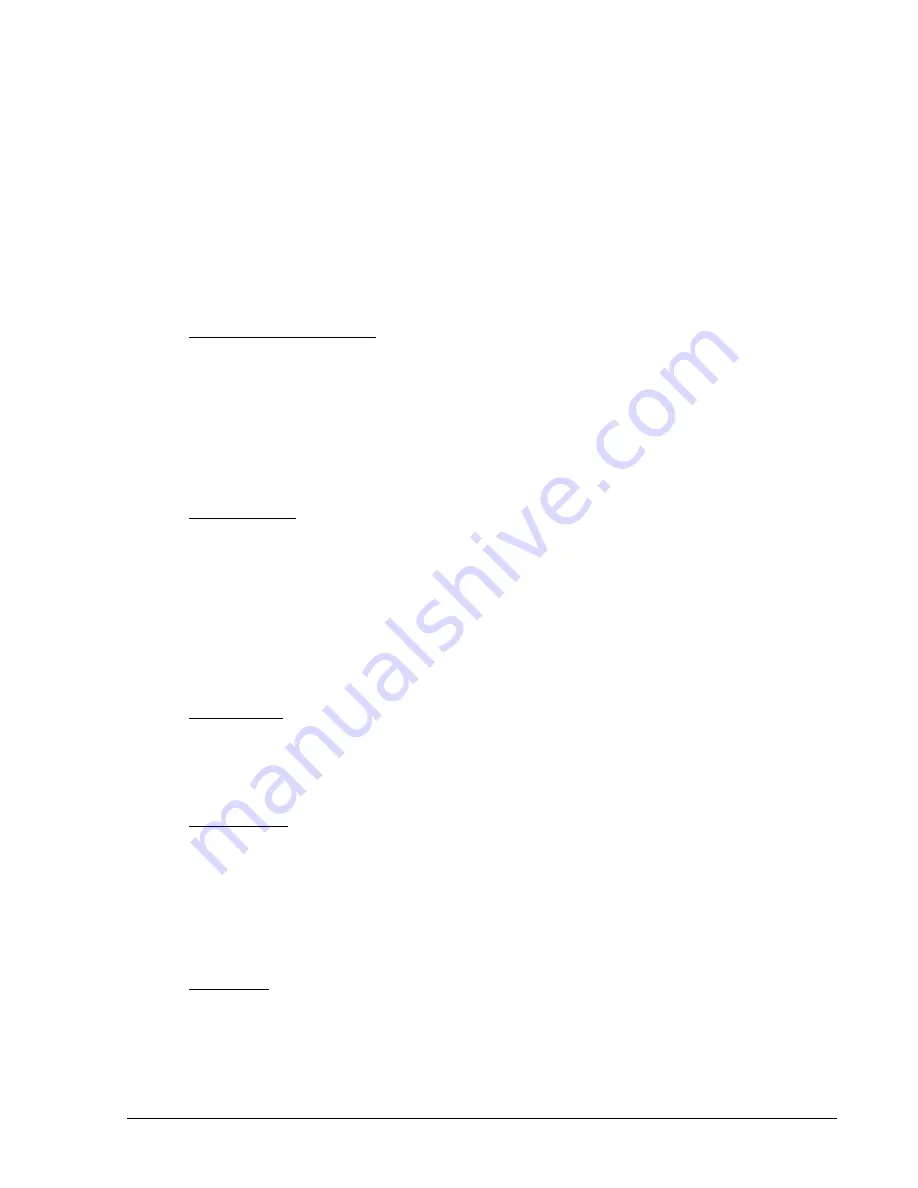
90
Southwestern Industries, Inc.
TRAK
2
OP
M11 Installation, Maintenance, Service, & Part List Manual
Initial adjustment
–
close the flow control all the way**, mark the knob with a black
marker to establish a reference starting point, and then open it 1 1/2 full turns.
* In order to close the door in a relatively controlled manner, a second flow control for
controlling the air going into the cylinder is used; this flow control is commonly known as
a “metering –in” type
(labeled 5 on drawing 27563-1).
Initial adjustment
- close the flow control all the way**, mark the knob with a black
marker to establish a reference starting point, then open it 1 1/2 full turns.
**Note: When closing flow controls used on this machine you will not feel a hard stop
when the flow control is completely closed, but you will feel a noticeable change in
tightening resistance as you approach the closed position, please use reasonable care
and do not over tighten them.
8.
Air/Oil Tool Change Cylinder
–
this is air-over-oil cylinder that is mounted near the top,
behind the spindle. Its output line carries high-pressure oil to the hydraulic cylinder built
into the spindle, for clamping and unclamping tools in the spindle. Please make sure to
monitor a small oil reservoir cup that is mounted near this cylinder, just above the head
sheet metal enclosure for easy visibility. The oil level inside this reservoir will only drop if
there is a leak in the system. Please note that the solenoid valve #1 described in item
5a provides air to this cylinder and a 2
nd
air line provides the air that is directed down
through the center of the spindle. See section 6.15 for how to bleed this hydraulic
system if air gets into it.
9.
ATC Air Cylinder
–
this is the cylinder that moves the ATC to the front and back when
changing tools. This cylinder has two adjustable internal cushions designed to decelerate
the carriage motion as smoothly as possible, as it approaches each end of its stroke.
These adjustment screws are located in the front and back end cap of the cylinder next
to the air line connections. They are factory set, and should not be tempered with. The
cushions must be properly adjusted to take advantage of this feature. The basic
adjustment of the cushion requires that the screw be turned almost all the way in at first,
and as the cylinder is moved back and forth with full load, the screw is slowly unscrewed
until the deceleration of the carriage is smooth and soft
–
see the initial setting
procedure above.
10.
Quick Exhaust
–
the 2 OP has a quick exhaust valve that helps to exhaust air quickly. On
the tool carrier carriage cylinder, the quick exhaust prevents the air cylinder from seeing
too high of a pressure during the ATC shift from the first to the second row of tools.
Once again, if you need to replace a quick exhaust valve, you must make sure to mount
it properly, as shown on the pneumatic schematic, drawing 27563-1.
11.
Reservoir Tank
–
this tank is used to store extra volume of compressed air for the front
door assist cylinder in the event the 90 psi compressed air supply line is disconnected
from the machine. It also acts as an air pressure accumulator to help maintain the air
pressure relatively constant during opening and closing of the front door. This tank will
keep the door feeling light even if the air supply is suddenly disconnected or removed.
Due to the check valve installed before the tank’s pressure regulator, the pressure will
stay in the front door reservoir tank overnight assuming you do not open and close the
door many times with the air disconnected.
12.
Check Valve
–
there is one check valve found prior to the inlet of the door pressure
regulator. It prevents air from exhausting from this line when air is removed from the
machine.
Summary of Contents for TRAK 2OP M11
Page 6: ...3 Southwestern Industries Inc TRAK 2 OP M11 Installation Maintenance Service Part List Manual...
Page 7: ...4 Southwestern Industries Inc TRAK 2 OP M11 Installation Maintenance Service Part List Manual...
Page 8: ...5 Southwestern Industries Inc TRAK 2 OP M11 Installation Maintenance Service Part List Manual...
Page 12: ...9 Southwestern Industries Inc TRAK 2 OP M11 Installation Maintenance Service Part List Manual...
Page 71: ...68 Southwestern Industries Inc TRAK 2 OP M11 Installation Maintenance Service Part List Manual...