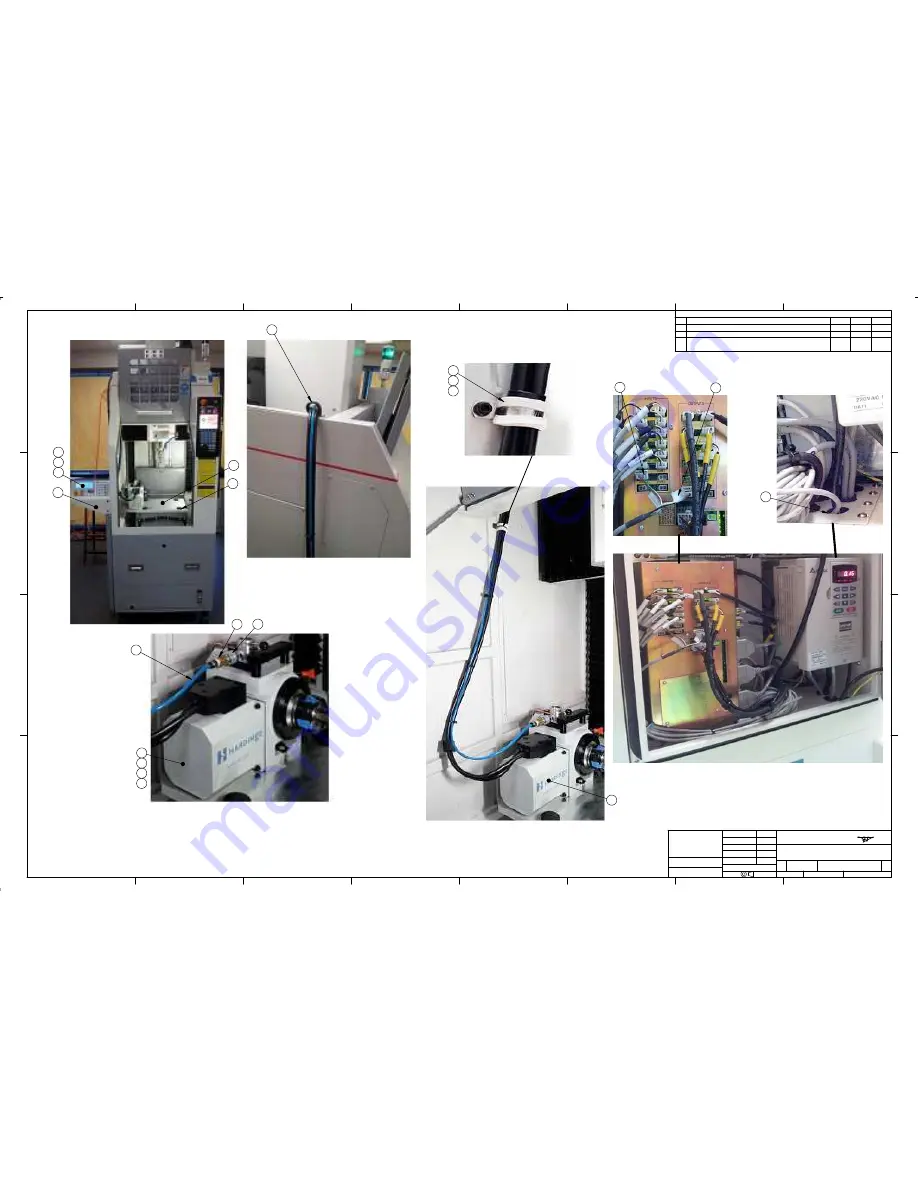
TITLE
SHEET
SIZE
CODE IDENT. NO.
DWG NO.
REV
SCALE:
OF
D
06238
NOTICE: THIS DESIGN WAS ORIGINATED BY AND EMBODIES A
CONFIDENTIAL PROPRIETARY DESIGN OWNED BY SOUTH-
WESTERN INDUSTRIES. IT IS DISCLOSED IN CONFIDENCE FOR
A SPECIFIC PURPOSE AND THE RECIPIENT HEREOF AGREES
NOT TO MAKE ANY REPRODUCTION, DISCLOSURE OR OTHER
USE OF THIS INFORMATION WITHOUT THE WRITTEN CON-
SENT OF SOUTHWESTERN INDUSTRIES.
DATE
APPROVALS
DRAWN BY
ENGINEER
CHECKER
FE
MATERIAL
FINISH
INDEXER READY KIT
HARDINGE
28137
3
-
7/14/14
Chris
-
-
C
DIMENSIONS ARE IN INCHES
DEC. .X = ±.1, .XX = ±.01, .XXX = ±.005,
ANGLES .XX = ±0°30'
FRACTIONS = ±1/8
FINISH = 125 RMS
REMOVE ALL SHARP EDGES
MASK ALL TAPPED HOLES
DIMENSIONING PER ASME Y14.5
8/29/14
TO
8/29/14
Sal
REV
ECN
DATE
APPRV
DESCRIPTION
REVISIONS
B
14354
1-7-15
LG
ITEM 16 26712 QTY 4 WAS: CLAMP-BALL LOCK QTY 1
A
B
C
D
A
B
C
D
1
2
3
4
5
6
7
8
1
2
3
4
5
6
7
8
THIRD ANGLE PROJECTION
SOUTHWESTERN INDUSTRIES, INC.
2615 HOMESTEAD PLACE
RANCHO DOMINGUEZ, CA 90220-5610
A
14201
8/29/14
TO
PRODUCTION RELEASE
C
14448 11-13-15
PB
ADDED ITEMS 14,17,18, 24, 35, 36. REVISED PICTURES &
FIGURE NUMBERS.
NOTES: (UNLESS OTHERWISE SPECIFIED).
1
FIG 1
30
21
28
2X
29
2X
3
20
7
10
9
15
23
15
1
REF
6
INDEXER OUT
6
INDEXER IN
2
16
1
33
4X
34
4X
FIG 4b
FIG 3b
FIG 3
FIG 3a
(RR)
(FT)
FIG 4
FIG 2
6
FIG 4a
4X
Summary of Contents for TRAK 2OP M11
Page 6: ...3 Southwestern Industries Inc TRAK 2 OP M11 Installation Maintenance Service Part List Manual...
Page 7: ...4 Southwestern Industries Inc TRAK 2 OP M11 Installation Maintenance Service Part List Manual...
Page 8: ...5 Southwestern Industries Inc TRAK 2 OP M11 Installation Maintenance Service Part List Manual...
Page 12: ...9 Southwestern Industries Inc TRAK 2 OP M11 Installation Maintenance Service Part List Manual...
Page 71: ...68 Southwestern Industries Inc TRAK 2 OP M11 Installation Maintenance Service Part List Manual...