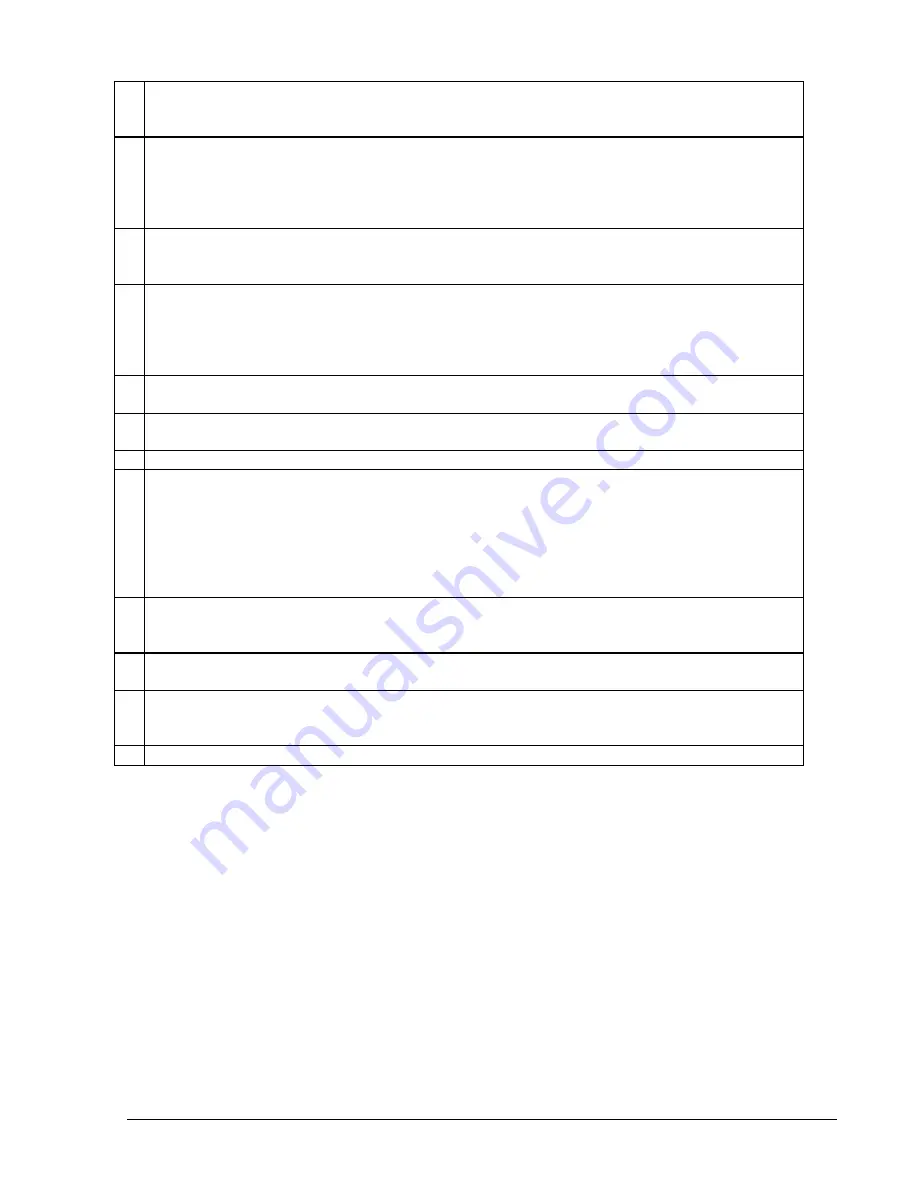
23
Southwestern Industries, Inc.
TRAK
2
OP
M11 Installation, Maintenance, Service, & Part List Manual
We set the air regulator for the door to be between 70 and 75 psi (verify) which equates to
roughly 8 to 10 lbs of force to lift the door. Make sure the door fully closes under its own
weight. Make sure hardware that holds door rollers is tight.
22. Press the manual tool change button on the head (GREEN button) and make sure air is
coming down through the spindle. This can be adjusted, see pneumatic system drawing
27563-1.
Put a tool in the spindle and verify the tool clamps once the green button is released.
23. Go to SETUP mode and press LOAD TOOLS. Follow the message and press GO. The
ATC should come forward. Remember the door must be shut. Hit RETURN once it comes out
and it should prompt you to press GO again to move it back.
24. Physically load a tool in and out of the ATC to make sure the orientation angle and tool
change height are correct. This can be done by pressing the TOOL IN ATC or TOOL OUT ATC
buttons. Check all 8 stations to make sure tools load properly. If there is a problem with the
X or Y location, adjust tool locations with service code 520. The Z tool change height can
also be adjusted with code 520.
25. Verify the ATC sensors that tell the control if the ATC is in or out are properly tightened.
Remove the rear cover on the machine to check them.
26. Turn off air to the machine and verify the control recognizes low air pressure. There
should be a warning message on the screen that says low air pressure.
27. Run spindle in DRO at low speeds.
28. Spindle head test
Run spindle at 1000 RPM for 5 minutes
Run spindle at 6000 RPM for 5 minutes. Make sure the spindle brakes properly from 6000
RPM. It should stop in 6 seconds or less.
Run spindle at 500 RPM increments for a few seconds per increment.
Please note any of the following: Head noise, excessive heat on spindle, vibration, spindle fan
noise.
29. Write a simple program with multiple tools called out and run program to make sure
everything runs properly, including changing tools in the ATC. Try to use actual tools when
running this program.
30. Double check the position of lower left hand corner ball lock location. Modify service 500
as necessary.
31. Make sure coolant wash down lines are adjusted properly. See section 5.10 for a picture
of how they should be adjusted. One line should be directed toward the rear door and one
toward the rear of the table to wash chips away so they do not interfere with the ATC.
32. Make sure fine chip filter is installed on top of coolant tank.
Summary of Contents for TRAK 2OP M11
Page 6: ...3 Southwestern Industries Inc TRAK 2 OP M11 Installation Maintenance Service Part List Manual...
Page 7: ...4 Southwestern Industries Inc TRAK 2 OP M11 Installation Maintenance Service Part List Manual...
Page 8: ...5 Southwestern Industries Inc TRAK 2 OP M11 Installation Maintenance Service Part List Manual...
Page 12: ...9 Southwestern Industries Inc TRAK 2 OP M11 Installation Maintenance Service Part List Manual...
Page 71: ...68 Southwestern Industries Inc TRAK 2 OP M11 Installation Maintenance Service Part List Manual...