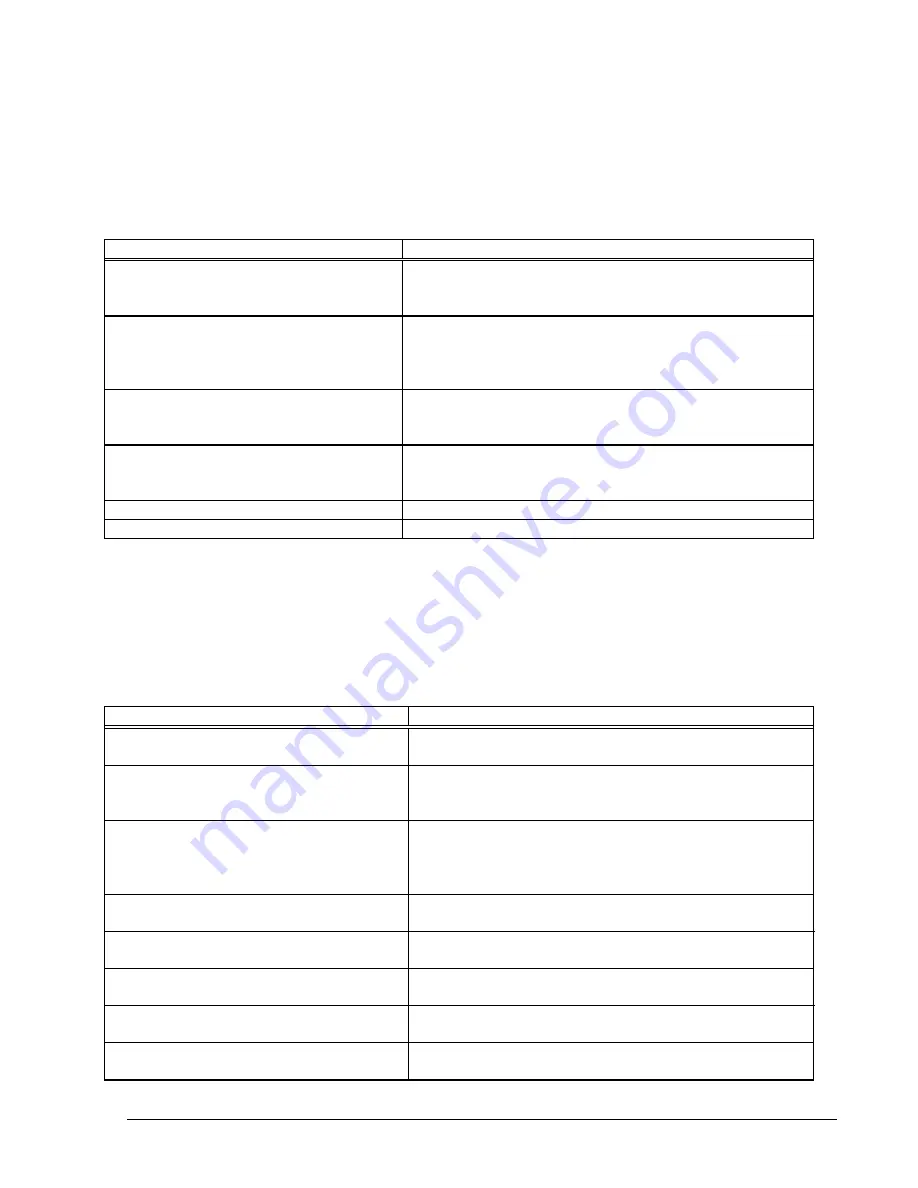
40
Southwestern Industries, Inc.
TRAK
2
OP
M11 Installation, Maintenance, Service, & Part List Manual
4.4.2 Spindle will not orientate properly
Each time a tool change is performed, the spindle must orientate the spindle so the dogs line up
with the ATC fingers that hold the tool.
Do the following Service Codes and procedures:
Code 510 – Spindle Setup, set spindle orientation
Possible Cause
Check This
The coupling that couples the motor to
the spindle has come loose
This is only likely after a heavy crash on the machine. If
this happens you will need to perform service code 510 -
spindle orientation to resolve the issue.
The spindle encoder is not being read
properly.
There is an index mark on the spindle encoder that we are
reading to orientate the spindle. Check this by running
service code 510. Make sure parameter 10-19 in the AC
drive matches the value set in service code 510
Poor cable connection at spindle encoder,
AC drive or computer module.
Check the cable connection at the spindle motor and AC
drive. Also check the cable that runs from the AC drive to
the computer module
Spindle Encoder Failure
Verify that all the encoder signals are being sent to the AC
drive by verifying the LEDs for Channel A, B and Z are
turning ON and OFF when the spindle is rotating.
Spindle drive failure
Replace drive
Computer module failure
Replace computer module. See section 5.3
4.4.3 Tool will not clamp or unclamp in the spindle
The automatic draw bar uses pull fingers that close down and pull up simultaneously on the
retention knob to lock the tool holder into the spindle taper. These fingers act in the opposite
fashion to release the tool holder. Tools can be clamped and unclamped manually by pressing
the green button on the head. See section 4.5.5 as well.
Possible Cause
Check This
The control thinks the door is closed when
pressing the green button on the head.
The door must be open for the green button to work
No or low air pressure
There is no air being supplied to the machine.
Is the pressure regulator set at 90 PSI
Is there a leak in the pneumatic system?
Are the tool holder(s) or the spindle taper
bore dirty?
Examine the spindle taper bore and the tool holder for
embedded chips and “tackiness” from excessive coolant
residue. Sometimes tools that are worn or have defects
on the taper will stick in the spindle.
The retention knob you are using is not
correct for this machine
See section 2 for an illustration of the correct retention
knob.
Loose tool holder retention knob
Check that the retention knob is tightened to the torque
value of between 70 and 85 ft lbs
Belleville washers are damaged, worn or
fatigued.
With a BT30 tension gage, check the pull strength of the
draw bar, it should be approximately 1000 lbs.
The pull fingers inside the spindle have
become loose
Check the fingers are tightened to the torque value of 20
ft lbs.
The pull fingers inside the spindle have
been damaged
Remove the pull fingers and visually inspect for damage
and replace as necessary
Summary of Contents for TRAK 2OP M11
Page 6: ...3 Southwestern Industries Inc TRAK 2 OP M11 Installation Maintenance Service Part List Manual...
Page 7: ...4 Southwestern Industries Inc TRAK 2 OP M11 Installation Maintenance Service Part List Manual...
Page 8: ...5 Southwestern Industries Inc TRAK 2 OP M11 Installation Maintenance Service Part List Manual...
Page 12: ...9 Southwestern Industries Inc TRAK 2 OP M11 Installation Maintenance Service Part List Manual...
Page 71: ...68 Southwestern Industries Inc TRAK 2 OP M11 Installation Maintenance Service Part List Manual...