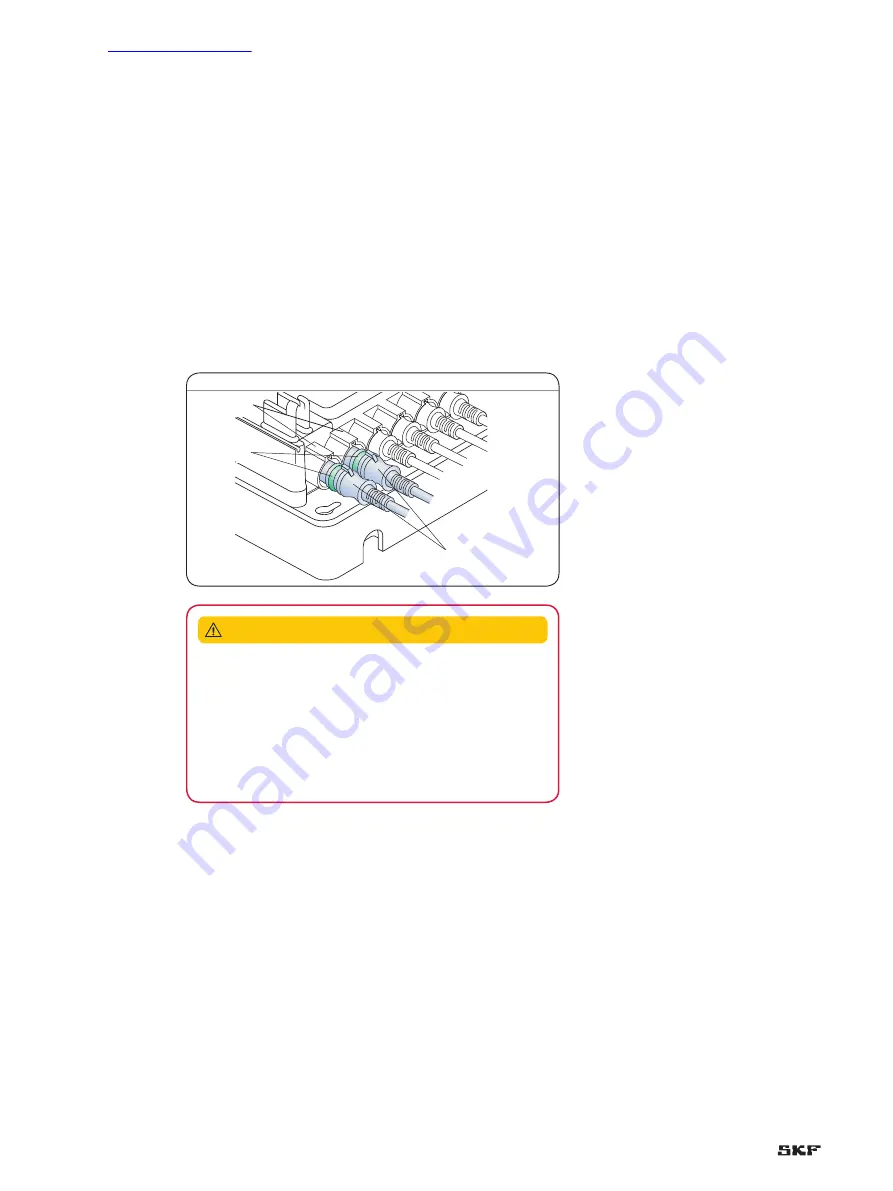
Maintenance
8.2.3 Check sealing function of DIN-8 plug
To be performed by a professional electrician
Check sealing function of DIN-8 plug
(
†
fig. 1
)
1
Separate the device from the energy supply.
2
Check sealing O-ring (3) of DIN-8 plug (2) for damage.
3
Ensure there is no irregular gap between the DIN-8 plug (2) and
the connection outlet (1) of the housing.
4
If sealing O-rings (3) are damaged, have the manufacturer
replace them.
5
If there is no damage, reconnect the device to the energy supply.
1
2
3
Fig. 10
8.2.4 Visual check of external condition
To be performed by qualified personnel
1
Separate the device from the energy supply.
2
Check the following structural components for visual external
damage:
2.1
Connecting cables for cracks, cuts and pinched sections
2.2
Rim covers for cracks, gaps and broken pieces
2.3
Tube set for scratches and indentations
3
Notify processor or manufacturer if damage is evident.
4
If no damage is evident and the processor/manufacturer has not
communicated any concerns, reconnect the device to the power
supply.
Device damage due to damaged or wrong sealing rings
Damaged or wrong sealing rings cannot guarantee protection
pursuant to IP40.
Therefore:
•
Ask the manufacturer to replace the damaged sealing rings
immediately.
C A U T I O N
44
www.lmotion.ru
Тел
.: (495)-921-34-60