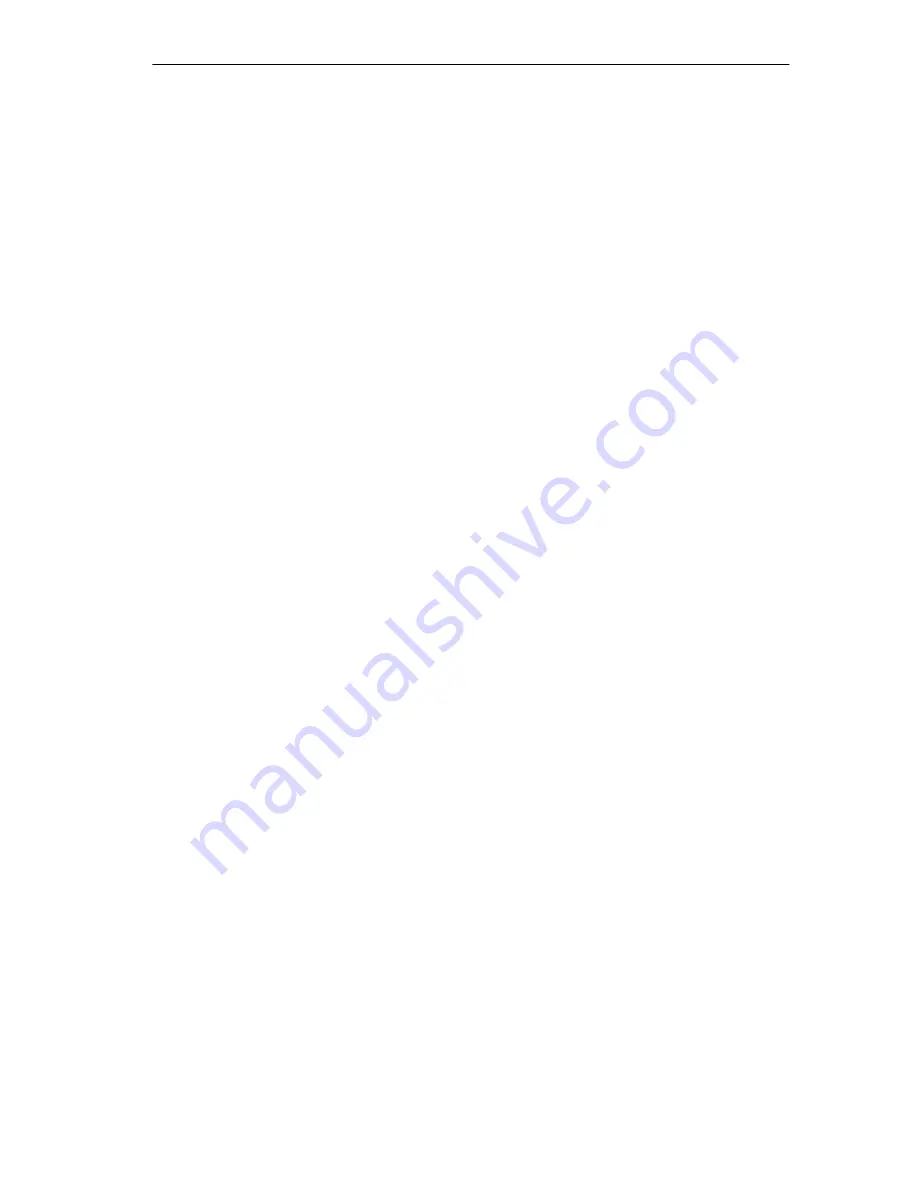
Installing LAN Cables
C-11
PROFIBUS Networks SIMATIC NET
6GK1970-5CA20-0AA1 Release 2 05/2000
How do you avoid potential differences?
Potential differences must be reduced by installing bonding conductors so that the
functions of the electronic components used are guaranteed.
When and why is equipotential bonding necessary?
The following reasons speak in favor of equipotential bonding:
S
Devices with a grounded interface can be damaged by potential differences.
S
The shield of the PROFIBUS cable must not be used for equipotential bonding.
This is, however, the case if parts of the system connected by the cable shield
are connected to different grounding points.
S
Equipotential bonding is a requirement for lightning protection.
Rules for Equipotential Bonding
Remember the following points about equipotential bonding systems:
S
The effectiveness of equipotential bonding is greater when the impedance of
the bonding conductor is low.
S
The impedance of the additional bonding conductor must not exceed 10% of
the shield impedance of the LAN cables.
S
Make large-area contact between the bonding conductor and the PE conductor.
S
Protect the bonding conductor from corrosion.
S
Install the bonding conductor so that the area enclosed by the bonding
conductor and signal cables is as small as possible.
S
Use copper or galvanized steel for the bonding conductor.
S
Include metal, conducting cable channels/racks in the equipotential bonding of
the building and between the individual parts of the system. The individual
segments of the channels/racks must be connected together with low
inductance and low resistance and connected to the building ground system as
often as possible. Expansion joints and angled connections should be bridged
by additional flexible grounding bands.
The connections between the individual segments of channels must be
protected from corrosion (long-term stability)
S
If there are connections between sections of buildings (for example separated
by expansion joints) with their own reference point for the building ground
network, a bonding conductor (equivalent copper cross-sectional area
≥
10mm
2
) must be installed parallel to the cables. This bonding conductor is not
necessary if metal, conducting cable channels/racks are used.
Summary of Contents for SIMATIC NET PROFIBUS
Page 10: ...Contents viii PROFIBUS Networks SIMATIC NET 6GK1970 5CA20 0AA1 Release 2 05 2000 ...
Page 11: ...PROFIBUS NETWORKS 1 ...
Page 26: ...PROFIBUS NETWORKS 1 16 PROFIBUS Networks SIMATIC NET 6GK1970 5CA20 0AA1 Release 2 05 2000 ...
Page 241: ...A 1 PROFIBUS Networks SIMATIC NET 6GK1970 5CA20 0AA1 Release 2 05 2000 Testing PROFIBUS A ...
Page 254: ...Testing PROFIBUS A 14 PROFIBUS Networks SIMATIC NET 6GK1970 5CA20 0AA1 Release 2 05 2000 ...
Page 288: ...Installing LAN Cables C 26 PROFIBUS Networks SIMATIC NET 6GK1970 5CA20 0AA1 Release 2 05 2000 ...
Page 325: ...F 1 PROFIBUS Networks SIMATIC NET 6GK1970 5CA20 0AA1 Release 2 05 2000 Dimension Drawings F ...
Page 338: ...Dimension Drawings F 14 PROFIBUS Networks SIMATIC NET 6GK1970 5CA20 0AA1 Release 2 05 2000 ...
Page 396: ...Infrared Link Modul ILM 6ZB530 3AC30 0BA1 54 Copyright by Siemens ...
Page 434: ......
Page 438: ...Contents ii PROFIBUS Optical Bus Terminal OBT C79000 G8976 C122 02 Contents ...
Page 450: ...Network Topology 4 4 PROFIBUS Optical Bus Terminal OBT C79000 G8976 C122 02 ...
Page 458: ...Installation and Startup 5 8 PROFIBUS Optical Bus Terminal OBT C79000 G8976 C122 02 ...
Page 460: ...Troubleshooting 6 2 PROFIBUS Optical Bus Terminal OBT C79000 G8976 C122 02 ...
Page 464: ...Technical Specifications 7 4 PROFIBUS Optical Bus Terminal OBT C79000 G8976 C122 02 ...
Page 468: ...References 9 2 PROFIBUS Optical Bus Terminal OBT C79000 G8976 C122 02 ...
Page 470: ...Abbreviations 10 2 PROFIBUS Optical Bus Terminal OBT C79000 G8976 C122 02 ...
Page 478: ...References I 4 PROFIBUS Networks SIMATIC NET 6GK1970 5CA20 0AA1 Release 2 05 2000 ...
Page 488: ...Glossary Glossary 8 PROFIBUS Networks SIMATIC NET 6GK1970 5CA20 0AA1 Release 2 05 2000 ...