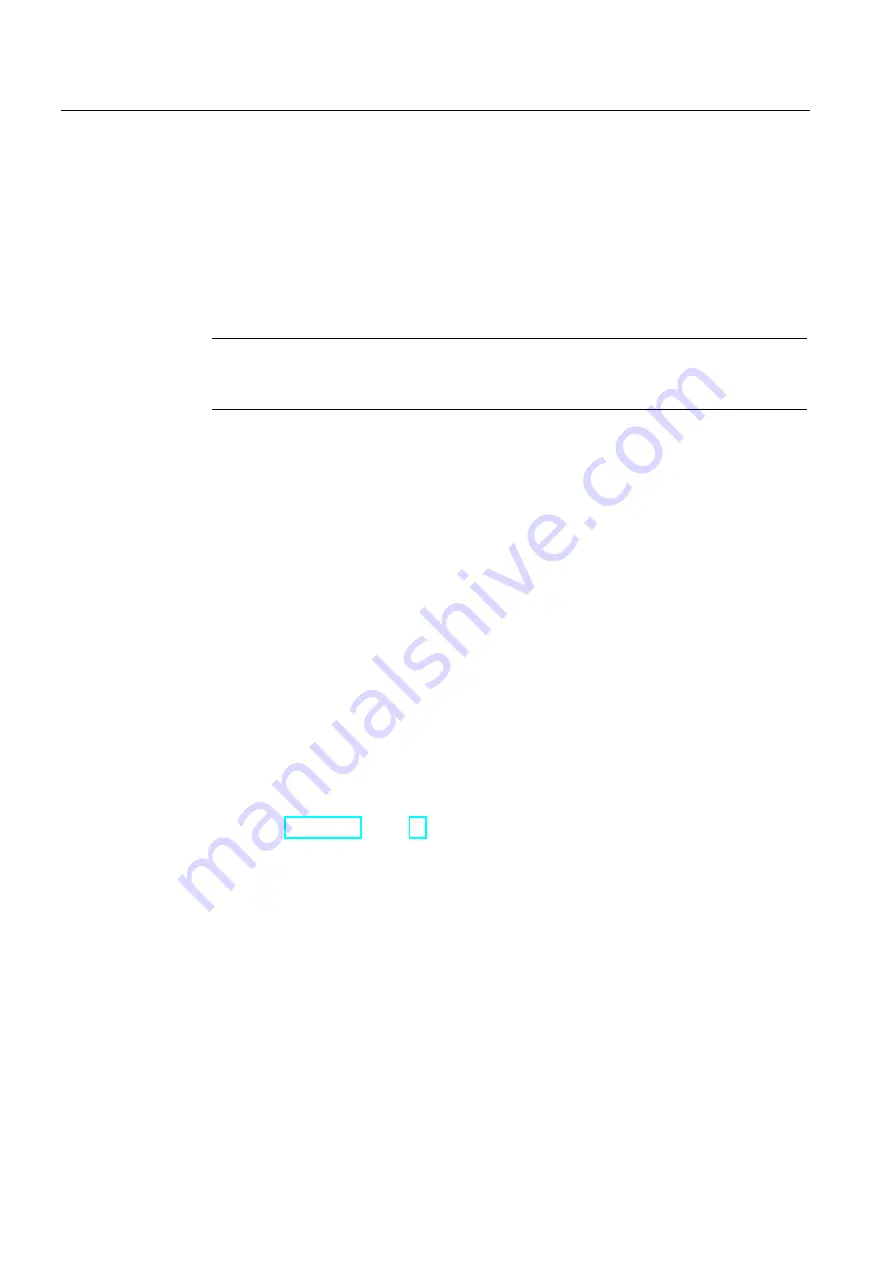
Wiring
6.8 Front connector for the I/O modules
ET 200MP Distributed I/O System
64
System Manual, 01/2013, A5E03723484-01
The front connector is characterized by the following:
●
40 clamping points each
●
Clamping technology: Screw
●
If you want to supply load groups with the same potential (non-isolated), use the potential
bridges supplied for the front connector. In four locations: 9 and 29, 10 and 30, 19 and
39, 20 and 40, the terminals can be bridged by means of potential bridges. Advantage:
Reduction of the wiring effort
Note
Please note that the potential bridges may be deployed up to a maximum rated voltage of
24 V DC! The current capacity per potential bridge is 8 A maximum.
Reference
Further information on the use of the potential bridges can be found in the Product Manual
for the respective I/O module.
6.8.2
Wiring front connectors for I/O modules without shield contact element
Introduction
The front connector connects the I/O modules with the process signals.
Requirements
●
The I/O modules are installed on the mounting rail.
●
The supply voltages are turned off.
●
Wires are prepared according to the utilized clamping technology.
●
Follow the wiring rules (Page 57).
Tools required
●
Stripping tool
●
3 to 3.5 mm screwdriver
Summary of Contents for simatic ET 200MP
Page 4: ...Preface ET 200MP Distributed I O System 4 System Manual 01 2013 A5E03723484 01 ...
Page 8: ...Table of contents ET 200MP Distributed I O System 8 System Manual 01 2013 A5E03723484 01 ...
Page 118: ...Service Support ET 200MP Distributed I O System 118 System Manual 01 2013 A5E03723484 01 ...
Page 126: ...Index ET 200MP Distributed I O System 126 System Manual 01 2013 A5E03723484 01 ...