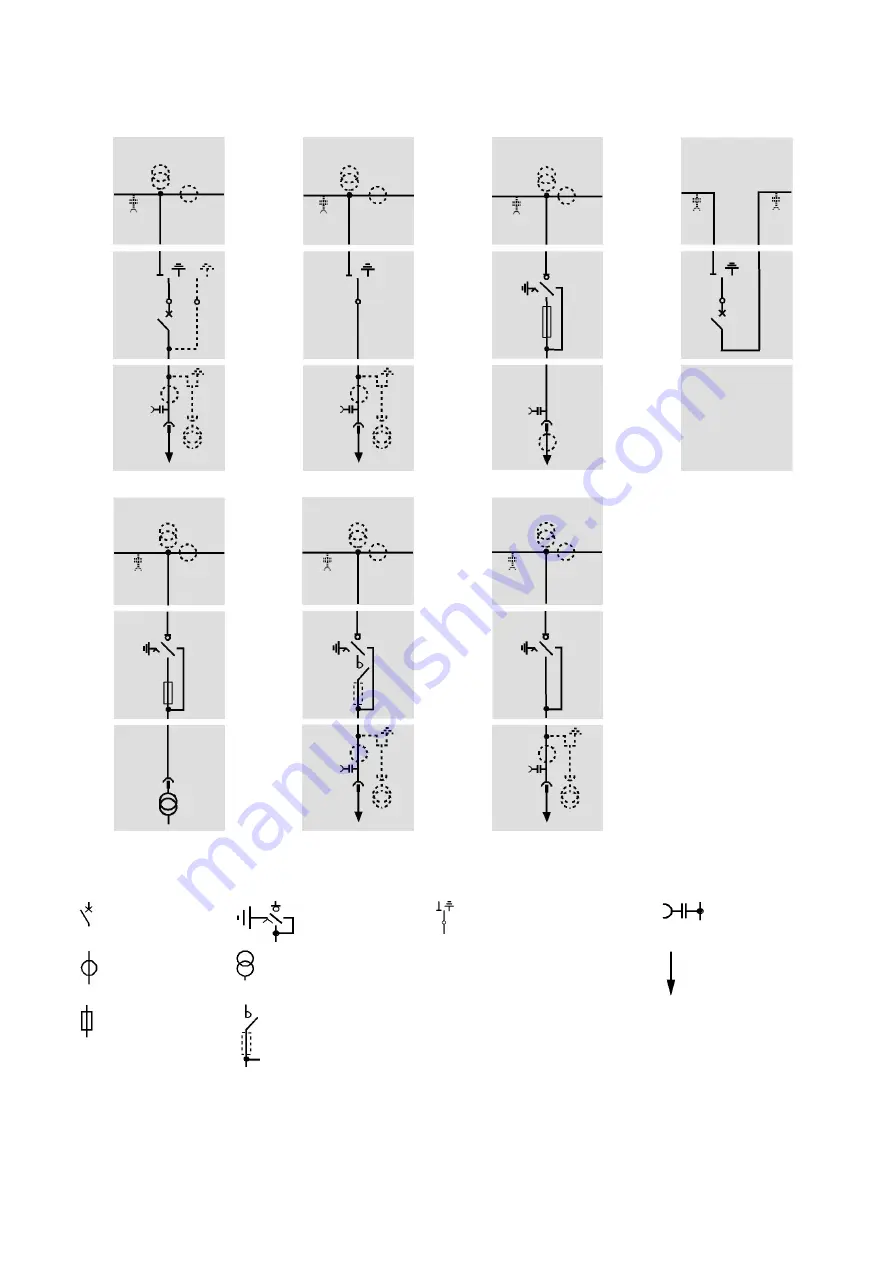
Description
12/293
Revision 11 • INSTALLATION AND OPERATING INSTRUCTIONS • NXPLUS C • 802-9081.9
7
Panel types
Circuit-breaker panel
Disconnector panel
Switch-disconnector panel
Bus sectionalizer
Metering panel
Vacuum contactor panel
Ring-main panel
Vacuum circuit-
breaker
Three-position switch-
disconnector
Three-position disconnector
Capacitive voltage
detecting system
Current transformer
Voltage transformer
--------------
These components can be
connected partially or
optionally
Cable (not included in the
scope of supply)
HV HRC fuse
Vacuum contactor