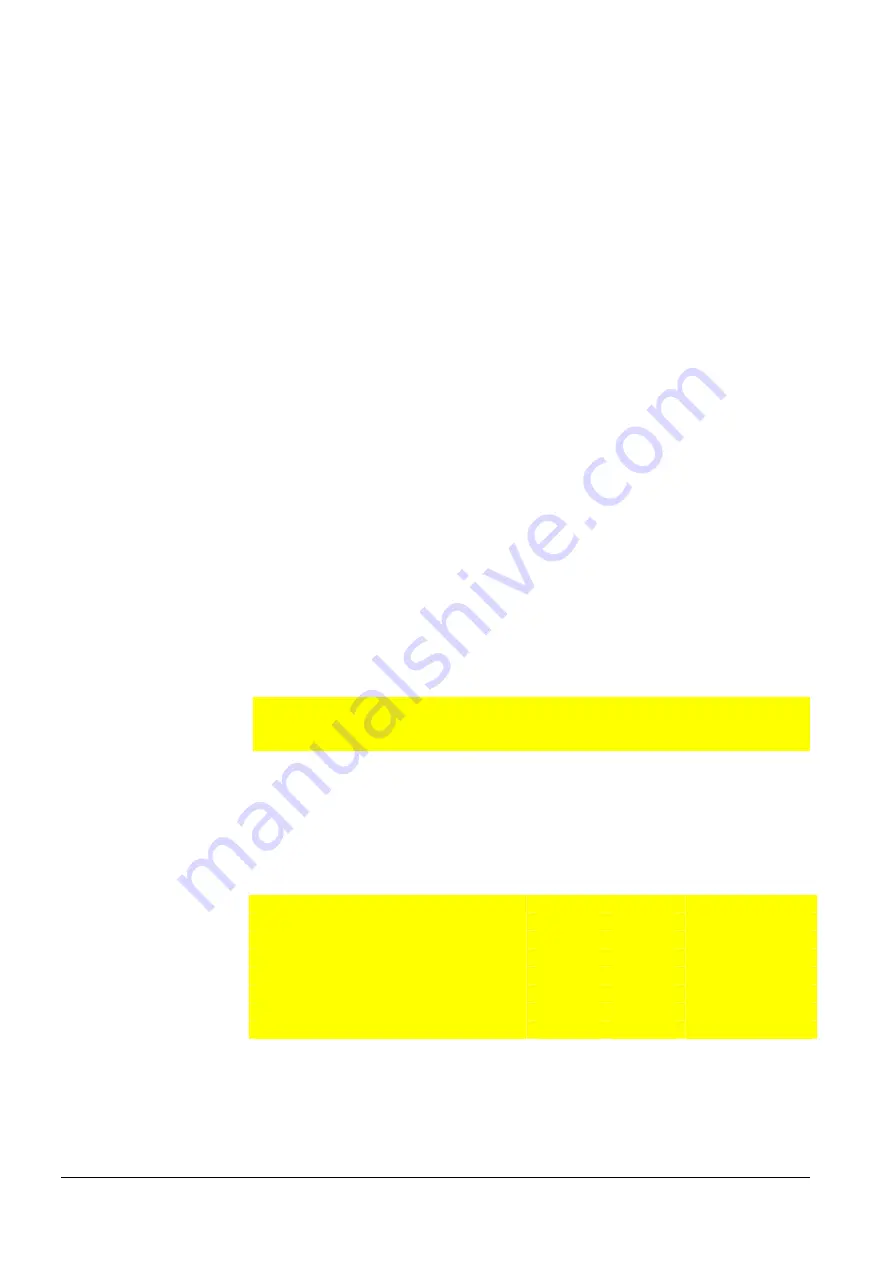
66/301
Siemens Building Technologies
Basic Documentation LMV5...
CC1P7550en
HVAC Products
5 Fuel / air ratio control (FARC)
13.08.2004
In the phases where the actuators are driven to one of the special positions (home,
prepurge, ignition or postpurge position), there is no continuous position check. To
make possible the change to the next phase, the required position must be reached. To
travel to the required position, the maximum time available is 35 seconds or 20 %
longer than
TmeNoFlame
parameterized. If the required position is not reached within
this maximum period of time, safety shutdown will be initiated
→
actuator overload pro-
tection. In the phases where the damper does not move, the position is continuously
checked. If there are deviations from the required position, adjustment attempts are
made where the
→
«Dynamic safety time ratio control» is used.
The position checkback signal delivered by the actuators is evaluated only when the
actuators do not travel, thus making possible precise position measurements.
To ensure that the actuators are not out of control of the basic unit for longer periods of
time, longer movements are subdivided into traveling steps of 1.2 seconds. After each
step, the required position must be reached. The required position is considered to be
reached when the actuator has traveled to a band width of
±
0.3°.
If the actual position does not agree with the required position, readjustments will be
made, whereby the
→
dynamic safety time of the fuel / air ratio control system will be
applied.
In multistage operation, the actuators are monitored at stationary points. The actuators
must reach these points within the calculated period of time, whereby the
→
dynamic
safety time of the fuel / air ratio control system will be applied.
Additional position checks are made during the actuators‘ travel, in order to find out if
the actuators do not move, or if they travel in the wrong direction.
5.1.3 Special features
To facilitate burner startup, startup and shutdown can be stopped in several phases.
If a program stop is active, the special positions (prepurge, ignition and postpurge posi-
tion) can be set in the respective phase.
If a program stop has been activated, it remains active until manual deactivation takes
place (even after power-OFF).
Parameter:
ProgramStop (deactivated / 24 PrePurgP / 32 PreP FGR /
36 IgnitPos / 44 Interv 1 / 52 Interv 2 / 72 PostPPos / 76
PostPFGR)
The actuators‘ direction of rotation can be reversed, so that the direction of rotation can
be matched to the mounting. method. The direction of rotation must be selected before
defining the ignition position and the curvepoints. If that is not observed, these points
must be deleted before the direction of rotation is reversed. For that purpose, a special
function called «Delete curves» is offered on the menu for selecting the direction of ro-
tation.
Parameters:
LMV51... LMV52...
1 AirActuator (standard / inverted)
x
x
2
GasActuator (oil) (standard / inverted)
x
x
3
OilActuator (standard / inverted)
x
x
4
AuxActuator (standard / inverted)
x
x
5 AuxActuator 2
x
6 AuxActuator 3
x
Outside the
operating position
Operating position
modulating
Operating position
multistage
Program stop
Direction of rotation
of actuators