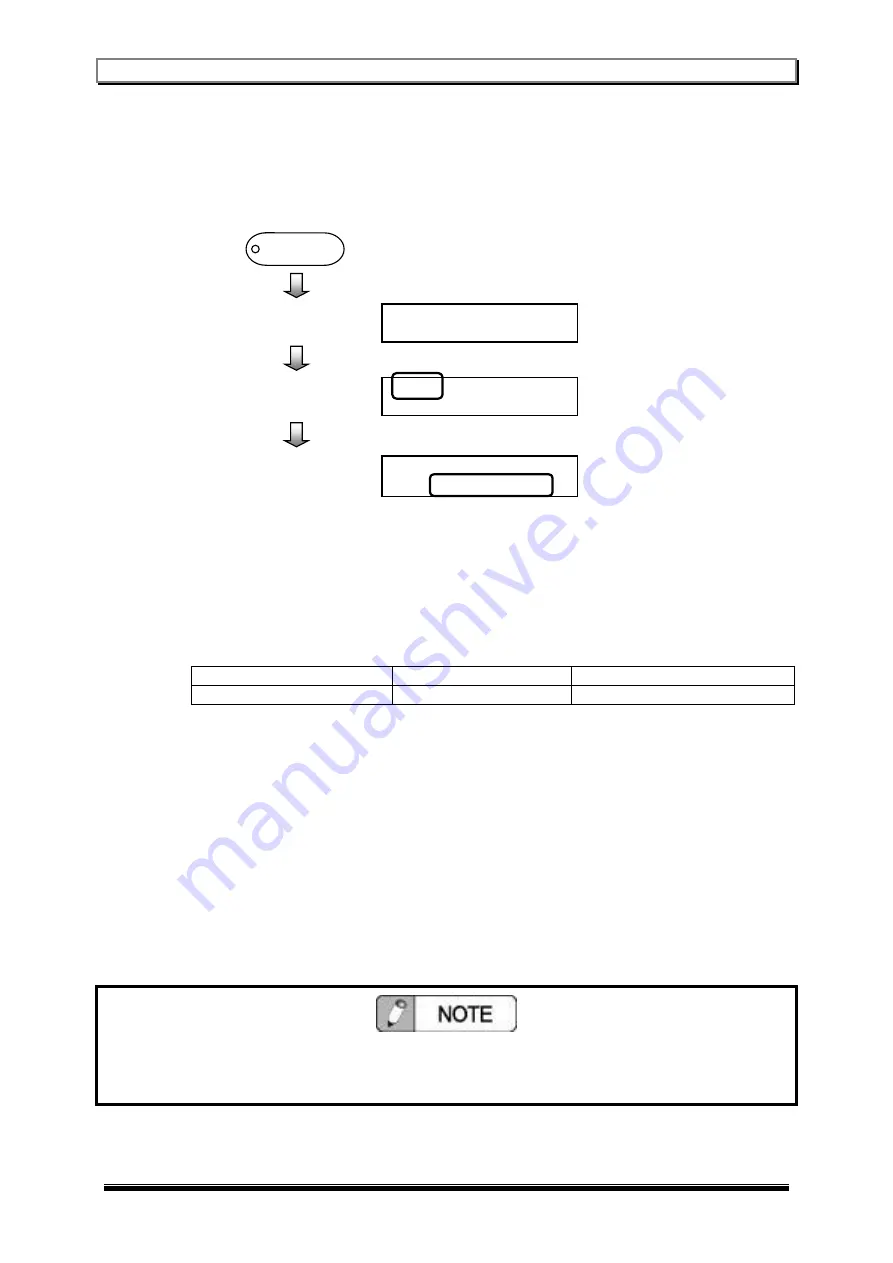
Chapter 4 Operating Panel
4-40
Setting the Pulse Rate
Specifies the extension length per pulse.
[Setting Procedure]
[Setting Value (1)]
•
CH. 1
Specifies the pulse rate for Digital Input 1.
•
CH. 2
Specifies the pulse rate for Digital Input 2.
[Setting Value (2)]
Enters the extension length per pulse.
Parameter
Default Value
Setting Range
Pulse Rate
0.001 mm/p
0.00001 mm/p to 100 mm/p
If the pulse form is A/B phase, the system multiplies the pulse count by four internally.
If a rotary encoder or other such device is attached, multiple the pulse rate by four.
Digital Input
Channel 1
Pulse Rate
Digital Input
>CH.1
>Pulse Rate (CH1)
0.100 mm/p
(1)
(2)
SYSTEM
Summary of Contents for AGS-100NX
Page 2: ...This page is intentionally left blank...
Page 16: ...Before Using the System xiv This page is intentionally left blank...
Page 20: ...Contents xviii This page is intentionally left blank...
Page 21: ...1 1 Chapter 1 Overview CONTENTS 1 1 Introduction 1 2 1 2 AGS X Unit Specifications 1 3...
Page 38: ...Chapte 2 Part List Specifications 2 12 This page is intentionally left blank...
Page 56: ...Chapter 3 Basic Instructions 3 18 This page is intentionally left blank...
Page 118: ...Chapter 5 Performing Tensile Tests 5 12 This page is intentionally left blank...
Page 126: ...Chapter 6 Performing Compression and Bending Tests 6 8 This page is intentionally left blank...
Page 130: ...Chapter 7 Method Files 7 4 This page is intentionally left blank...
Page 134: ...Chapter 8 Control Input Output 8 4 This page is intentionally left blank...
Page 142: ...Chapter 9 Sensor Input Output 9 8 This page is intentionally left blank...
Page 146: ...Chapter 10 Maintenance and Inspection 10 4 This page is intentionally left blank...