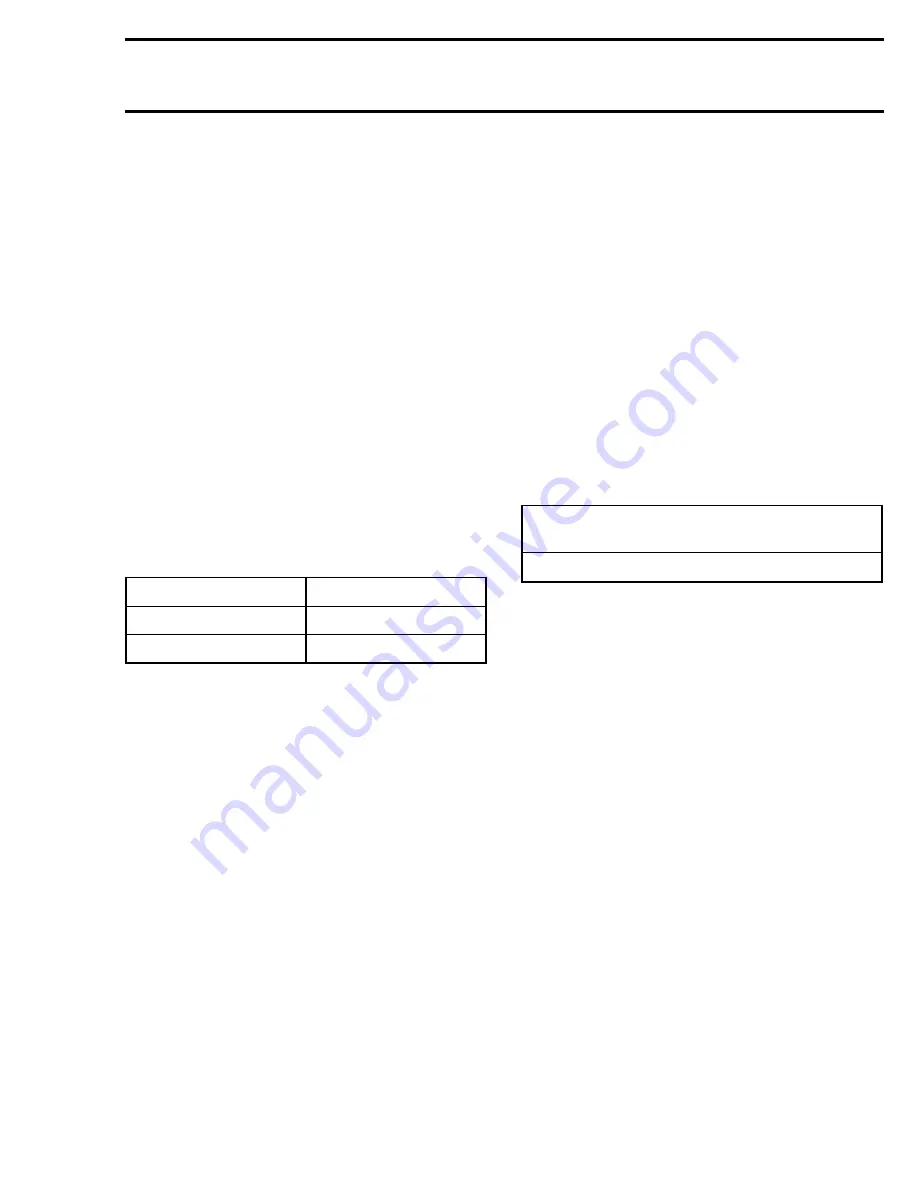
Section 07
ENGINE MANAGEMENT (DI)
Subsection 03
(COMPONENT INSPECTION AND ADJUSTMENT)
SMR2003_024 _07_03A.FM
07-03-15
Electrical Test
Safety lanyard must be on DESS post.
Using the vehicle communication kit (VCK) with
the B.U.D.S. software, energize the fuel injector
from the ACTIVATION section.
If the injector does not work, disconnect the con-
nector from the injector.
Install a temporary connector to the injector with
wires long enough to make the connection out-
side the bilge and apply voltage (12 V) to this test
harness.
This will validate the injector mechanical and elec-
trical operation.
If it does not work, replace it.
Otherwise, check the resistance of the fuel injec-
tor circuit.
Reconnect
the injector and disconnect the AMP
connector number 4 on the MPEM.
Using a multimeter, check resistance value be-
tween terminals as follows.
The resistance should be between 1.7 and 1.9
Ω
.
If resistance value is correct, try a new MPEM.
Refer to MPEM REPLACEMENT procedures else-
where in this section.
If resistance value is incorrect, repair the wiring
harness/connectors between AMP connector and
fuel injector.
Fuel Injector Replacement
When one fuel injector is defective, both have to
be replaced at the same time. Be sure to check
the other one. Also replace direct injectors.
Removal
See FUEL PRESSURE REGULATOR REPLACE-
MENT
above for procedure. However, do not re-
move any regulator.
To remove fuel injector, pull it out of rail.
Installation
For the installation, reverse the removal proce-
dure. Paying attention to the following details.
If the same injector is reinstalled, carefully inspect
O-ring condition before reinstalling fuel injector.
Replace O-ring with a new one if damaged.
Insert the fuel injector in place with your hand. Do
not use any tool.
NOTE:
A thin film of injection oil may be applied
to O-ring to ease insertion in rail.
Apply Loctite 243 on rail retaining screws then torque
to 25 N•m (18 lbf•ft).
AIR/FUEL RAIL
Pressure test
Crank or start engine
and observe fuel pressure.
If pressure is within limits, fuel and air systems are
working adequately. No subsequent tests are nec-
essary for the air/fuel system.
Remove pressure gauge and reinstall fuel hose. At
installation apply engine oil on O-ring.
If pressure is out of limits, check air/fuel rail for
leaks. If it is not leaking then replace air pressure
regulator.
A higher pressure may be an indication of a
pinched or clogged air pressure regulator outlet
line.
Air Pressure Regulator Replacement
Removal
See FUEL PRESSURE REGULATOR REMOVAL
above for procedure.
Remove the fuel regulator then the air pressure
regulator.
Installation
For the installation, reverse the removal procedure
but pay attention to the following.
NOTE:
A thin film of injection oil may be applied
to O-ring to ease insertion in rail.
Apply Loctite 243 on rail retaining screws then
torque to 25 N•m (18 lbf•ft).
COMPONENT
TERMINAL LOCATION
Fuel injector MAG
7 and 13
Fuel injector PTO
8 and 14
FUEL PRESSURE
(when cranking engine or when engine is running)
738 ± 14 kPa (107 ± 2 PSI)
www.SeaDooManuals.net
Summary of Contents for 2003 GTI LE RFI
Page 1: ...www SeaDooManuals net ...
Page 767: ...NOTE www SeaDooManuals net ...
Page 768: ...NOTE www SeaDooManuals net ...
Page 769: ...F00Z0D 2003 GTI MODEL WARNING www SeaDooManuals net ...
Page 770: ...F00Z0C 2003 GTI LE MODEL WARNING www SeaDooManuals net ...
Page 771: ...F00Z0E 2003 GTI LE RFI MODEL WARNING www SeaDooManuals net ...
Page 772: ...F00Z0J 2003 RX DI MODEL WARNING www SeaDooManuals net ...
Page 773: ...F00Z0I 2003 GTX DI MODEL WARNING www SeaDooManuals net ...
Page 774: ...F00Z0K 2003 XP DI MODEL WARNING www SeaDooManuals net ...
Page 775: ...F00Z0F 2003 GTX 4 TEC MODEL WARNING www SeaDooManuals net ...
Page 776: ...F00Z0G 2003 GTX 4 TEC MODEL WITH AUXILIARY DESS MODULE WARNING www SeaDooManuals net ...
Page 777: ...F00Z0B 2003 GTX 4 TEC AND GTX 4 TEC SUPERCHARGED MODELS WARNING www SeaDooManuals net ...
Page 779: ...www SeaDooManuals net ...