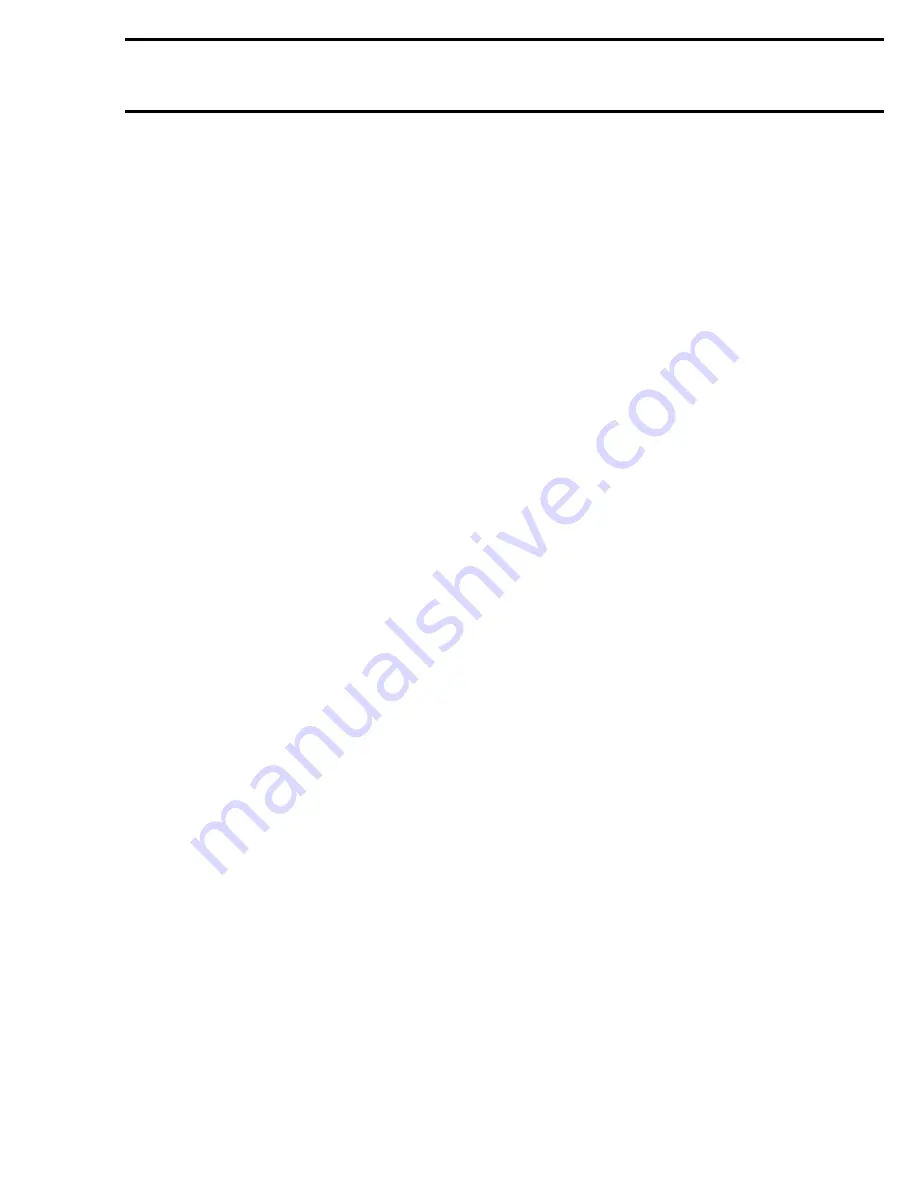
Section 07
ENGINE MANAGEMENT (DI)
Subsection 03
(COMPONENT INSPECTION AND ADJUSTMENT)
SMR2003_024 _07_03A.FM
07-03-37
1. Choose the
Setting
tab and look under IGNI-
TION OFFSET.
2. Check the
Locked
box to “freeze” the timing at
the correct value.
3. The VCK displays the number that is stored in
the MPEM.
4. Now click the up or down arrow to change the
number of the current angle so that the TDC
setting marks align when checking with the tim-
ing light. Each step makes an adjustment of 1/4
degree.
NOTE:
Each time the setting is changed on the
screen, the new value is also changed in the
MPEM, so there may be a slow response, do not
make changes too quickly.
5. When marks align, uncheck the
Locked
box to
finish.
NOTE:
This will write the new value immediately
in the MPEM. There is no need to press the “Write
data” button to transfer the data to the MPEM un-
less other changes were made. However, we rec-
ommend to reset the service hours when you per-
form a service action such as the TDC setting.
NOTE:
The MPEM features a permanent (non-vol-
atile) memory and keeps the TDC setting pro-
grammed even when the watercraft battery is dis-
connected.
Engine Start/Stop Switch Verification
A quick operation test can be done using the vehi-
cle communication kit (VCK) with the B.U.D.S. soft-
ware, using the MONITORING section. Press the
start button and look at the Start button LED. It
should turn on, indicating the starting system is
working on the input side (start button, MPEM and
wiring). You know now the problem is on the output
side (MPEM output signal to starting solenoid, wir-
ing harness going to the solenoid, starter motor. Re-
fer to STARTING SYSTEM for testing procedures).
Otherwise, check the input side as follows.
Disconnect the YELLOW/RED wire of the start/
stop switch. Using an ohmmeter, connect test
probes to YELLOW/RED wire and to ground.
Measure resistance, it must be an open circuit
(switch is normally open). Depress and hold switch,
the ohmmeter should read close to 0 ohm. Other-
wise, replace switch.
If the switch tests good, check continuity of cir-
cuits 2-8 and 2-12 using a multimeter.
If wiring harness tests good, it could be the MPEM.
Try a new MPEM referring to MPEM REPLACE-
MENT procedures elsewhere in this section.
Safety Lanyard Switch Verification
If 2 short beeps are not heard when installing the
safety lanyard, refer to DIAGNOSTIC PROCEDURES.
The following continuity tests can also be per-
formed using an ohmmeter:
Disconnect switch wires.
Safety Lanyard Removed
Connect test probes to switch BLACK and BLACK/
YELLOW wires. Measure resistance, there should
be NO continuity (open circuit).
Connect one test probe to the WHITE/GRAY wire
and the other test probe to the switch terminal.
Measure resistance, it must be close to 0 ohm.
Connect one test probe to the BLACK wire and the
other test probe to the switch ring. Measure resis-
tance, it must be close to 0 ohm.
Safety Lanyard on Switch
Connect test probes to switch BLACK and BLACK/
YELLOW wires. Measure resistance, it must be
close to 0 ohm.
As the DESS switch also controls the signal wire
to the power supply cut-off relay, it should be
checked as described below.
Power Supply Cut-Off Relay Verification
When the safety lanyard is on its post, the relay
allows current to be supplied from the battery to
the RED/PURPLE wire which supplies the MPEM
and all the electrical components (except bilge
pump which is connected to battery power on
XP
DI models
).
When the safety lanyard is NOT on its post, the
relay cuts the current supply from the battery to
the MPEM and the electrical components thus
preventing current drain that would slowly dis-
charge the battery.
Test the signal wire to the power supply cut-off
relay as follows:
Disconnect DESS switch wires.
Connect test probes to switch BLACK and BLACK/
PURPLE wires.
With safety lanyard NOT on its switch
: Measure
resistance. There should be NO continuity (open cir-
cuit). Otherwise replace DESS switch.
www.SeaDooManuals.net
Summary of Contents for 2003 GTI LE RFI
Page 1: ...www SeaDooManuals net ...
Page 767: ...NOTE www SeaDooManuals net ...
Page 768: ...NOTE www SeaDooManuals net ...
Page 769: ...F00Z0D 2003 GTI MODEL WARNING www SeaDooManuals net ...
Page 770: ...F00Z0C 2003 GTI LE MODEL WARNING www SeaDooManuals net ...
Page 771: ...F00Z0E 2003 GTI LE RFI MODEL WARNING www SeaDooManuals net ...
Page 772: ...F00Z0J 2003 RX DI MODEL WARNING www SeaDooManuals net ...
Page 773: ...F00Z0I 2003 GTX DI MODEL WARNING www SeaDooManuals net ...
Page 774: ...F00Z0K 2003 XP DI MODEL WARNING www SeaDooManuals net ...
Page 775: ...F00Z0F 2003 GTX 4 TEC MODEL WARNING www SeaDooManuals net ...
Page 776: ...F00Z0G 2003 GTX 4 TEC MODEL WITH AUXILIARY DESS MODULE WARNING www SeaDooManuals net ...
Page 777: ...F00Z0B 2003 GTX 4 TEC AND GTX 4 TEC SUPERCHARGED MODELS WARNING www SeaDooManuals net ...
Page 779: ...www SeaDooManuals net ...