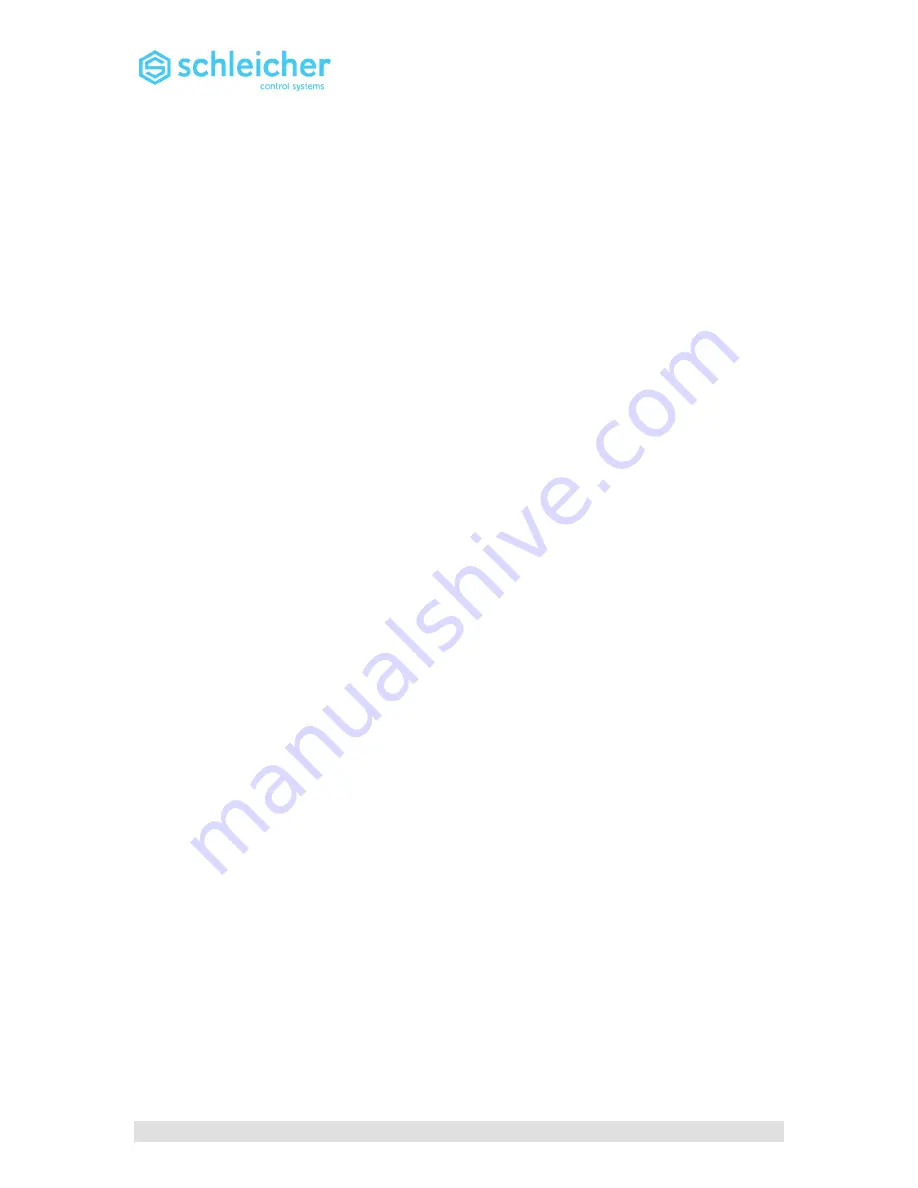
CANopen Field Bus
76
Operating Manual XCx 300 / 500 / 540 Version 09/08
7
CANopen Field Bus
7.1
Fundamentals
General
CANopen is based on the CAN Application Layer for industrial CAL
applications. The CANopen communications profile CiA DS-301
specifies the mechanisms for configuring and communication between
devices in real-time environments.
CANopen uses the data transmission layer to ISO 11898 and CAN 2.0
A+B.
Description of device details via an EDS (Electronic Data Sheet)
Object-oriented communication with PDOs and SDOs
Transmission of real-
time data with ‘pure’ CAN as the PDO
(Process Data Object) PDOs can be sent by all slaves, either
event-driven or synchronized
Complex data or low-priority services are transmitted/processed
with SDOs (Service Data Objects)
CANopen configuration managers (or masters) carry out functions
such as network management during network start-up. However,
they are not necessary for communication between the slaves.
In theory up to 127 stations are possible on one bus.
In practical terms, however, the number of bus stations is
restricted by the respective bus topology, and in particular by the
type of CAN transceiver modules used.
(current limit on Schleicher CAN devices is 64)
CNopen with XCx
The XCx PLC can access network variables and parameterizing and
diagnosis functions via the CANIO driver. Driver installation and
network startup are described in the startup section of the XCx
manual.
You can also access direct network variables, see Accessing direct
network variables.
The parameterizing and diagnosis functions relate to the hardware
and software of the XCx CANopen interface, which is described here
as the CAN processor. See "Accessing parameterizing and diagnosis
functions" and "Parameterizing and Diagnosis Functions".