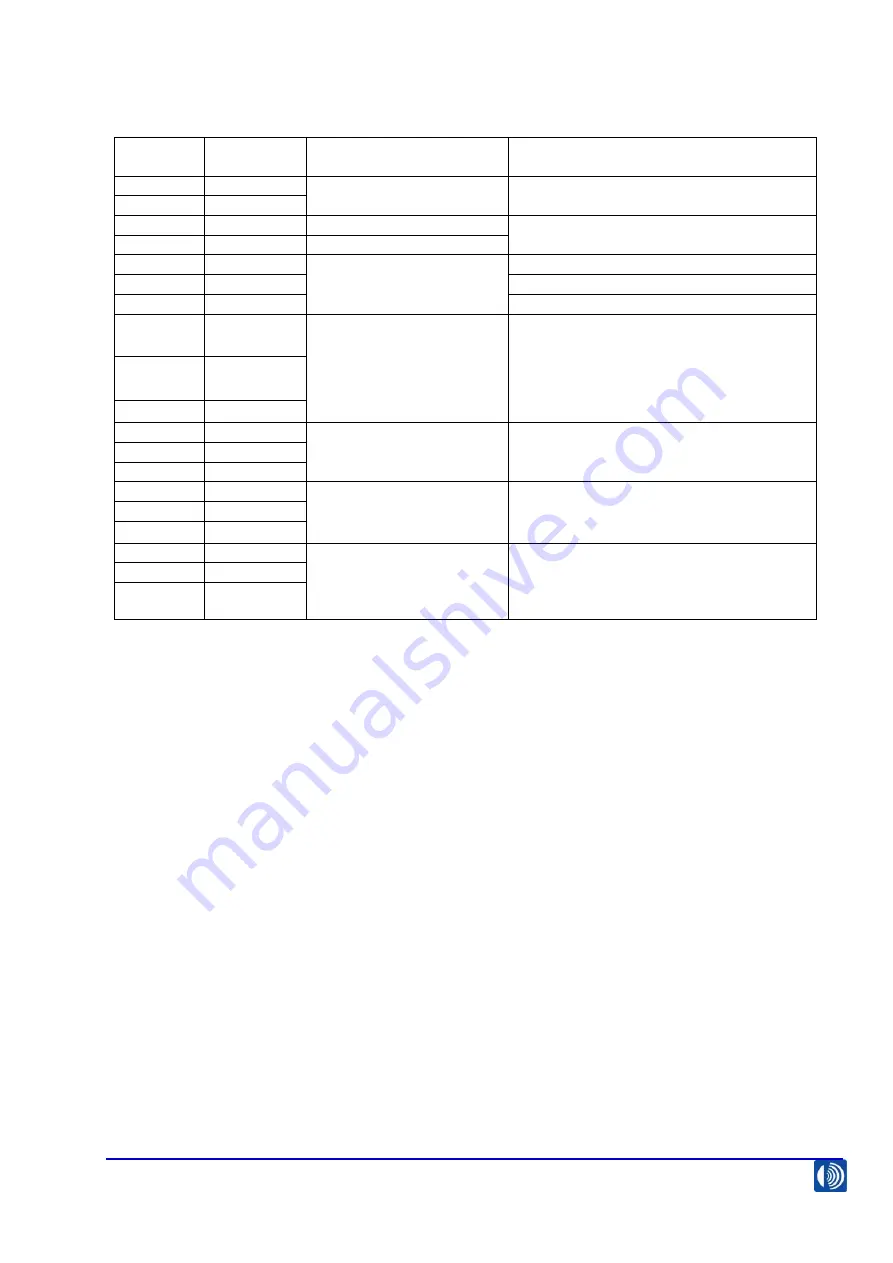
Operating manual for the VISATRON VN2020
V2.0 12/2021 EN
Page
42
of
106
SCHALLER AUTOMATION
66440 Blieskastel / Saarland / Germany / Industriering 14 / P.O. Box 1280
Industrielle Automationstechnik GmbH & Co. KG
T
el. +49(0)6842-508
-
0
/ Fax -260 / Email: [email protected] /
www.schaller-automation.com
Terminal
No.
Terminal
Connect to
Note/action
1
24 V DC +
Power supply
Voltage range: 18-31.2 V
2
24 V DC -
3
Spare S1
Reserve
4
Spare S2
5
A/H
Remote indicator
RS485 A/CAN H
6
B/L
RS485 B/CAN L
7
GND
RS485 GND/CAN GND
8
NC1
Alarm system/
safety system
Contacts COM1 and NO1 close in
Ready mode
9
COM1
10
NO1
11
NC2
Alarm system/
safety system
Contacts COM2 and NO2 close in the
event of an oil mist alarm (High Oil Mist
Alarm)
12
COM2
13
NO2
14
NC3
Alarm system/
safety system
Contacts COM3 and NO3 close in the
event of an oil mist alarm (High Oil Mist
Alarm)
15
COM3
16
NO3
17
NC4
Alarm system/
safety system
Contacts COM4 and NO4 close on pre-
alarm (Oil mist pre-alarm). Pre-alarm is
triggered from 70% of the high oil mist
alarm threshold.
18
COM4
19
NO4
Table 1: Wiring diagram of the terminal blocks