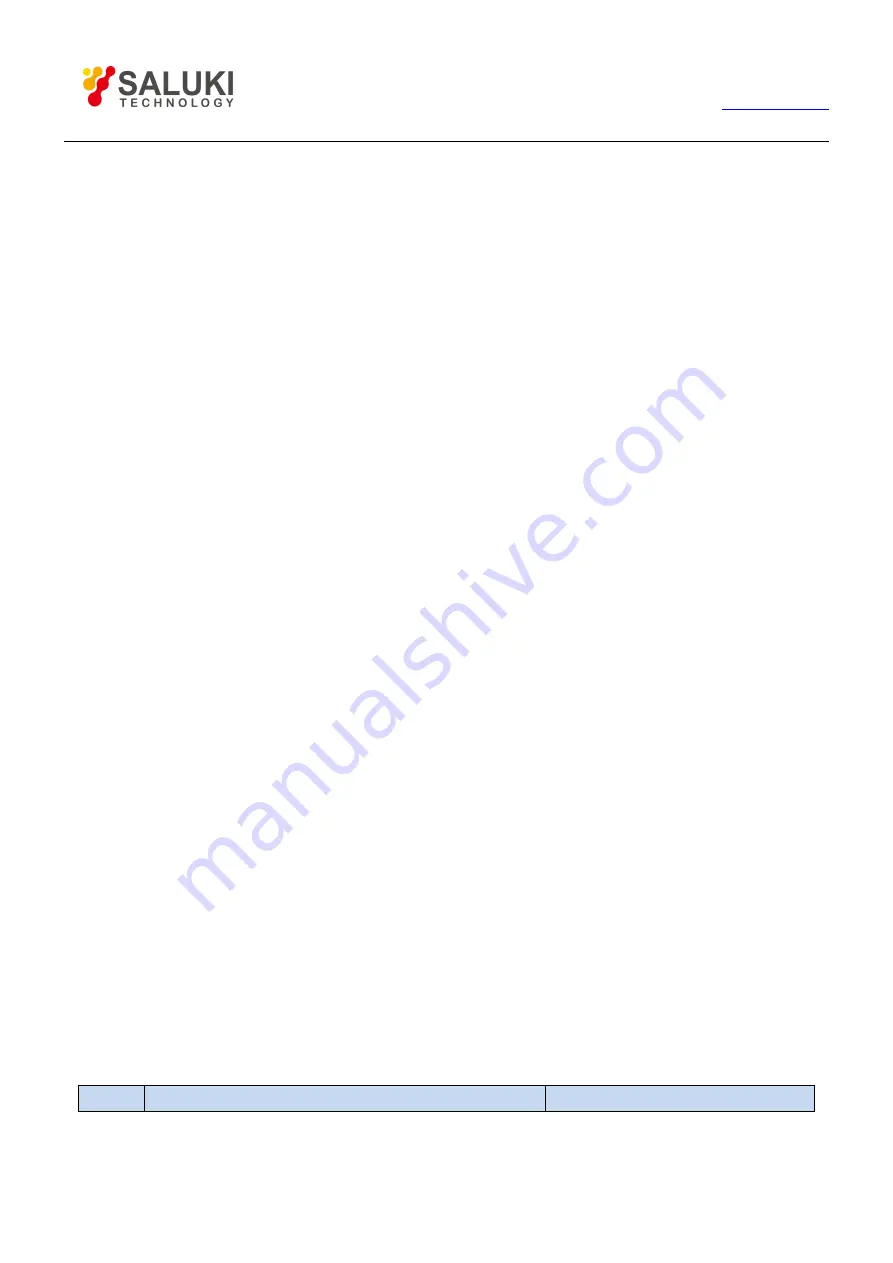
Tel: 886.909 602 109 Email: [email protected]
98
The controller is any computer used to communicate with the SCPI device. The controller may be a personal computer, a
small computer or a card inserted onto a cage. Some artificial intelligence device can also be used as a controller.
b. Device
The device is any component that supports SCPI. Most devices are electronic measuring or excitation device and use the
GPIB interface for communication.
c. Program message
The program message is a combination of one or more correctly formatted SCPIs. It guides the device to measure and
output the signal.
d. Response message
The response message is a data set that specifies the SCPI format. It is always sent from the device to the controller or
listener to remind the controller of the internal condition or measured value of the device.
e. Command
A command is an instruction in compliance with the SCPI standard. The combination of controller commands forms a
message. In general, a command includes the keyword, parameter and punctuation.
f.
Event command
An event-type SCPI can't be queried. An event command generally has no corresponding key settings on front panel. Its
function is to trigger an event at a particular moment.
g. Query
Query is a special command. When the controller is queried, it is necessary to return to the response message in
conformity with syntax requirement of the controller. The query statement is always ended with a question mark.
2) Command type
There are two types of SCPIs: common commands and instrument-specific commands. Common commands are defined
in IEEE 488.2 to manage macros, status registers, synchronization, and data storage. Common commands are easy to
recognize as they all begin with an asterisk. For example
*IDN? , *OPC and *RST are common commands. Common commands don
‟
t belong to any instrument-specific
command. The instrument uses the same method to interpret them without consideration to the current path setting.
It is very easy to identify instrument-specific commands because they contain a colon (:). The colon is used between the
beginning of a command expression and a keyword, for example: FREQuency[:CW?]. Instrument-specific commands
are divided into command subsets of corresponding subsystem according to the functional block inside the instrument.
For example, the power subsystem (:POWer) contains the power-related command while the status subsystem (:STATus)
contains the command for the status control register.
3) Instrument-specific command syntax
Table 5.2 Special Characters in Command Syntax
Symbol
Meaning
Example