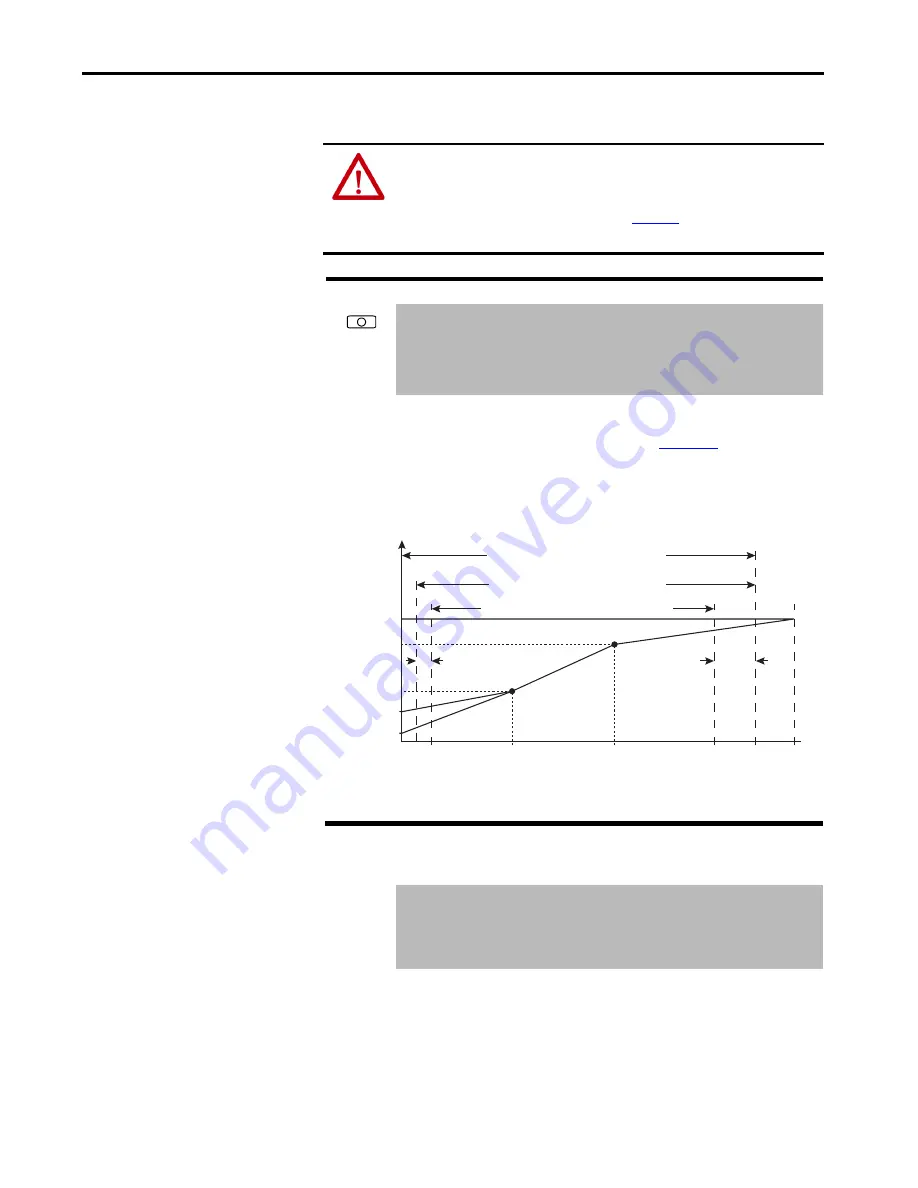
Rockwell Automation Publication D2-3518-4 - January 2020
87
Parameter Descriptions
Chapter 9
Sets the high limit for the speed reference after scaling is applied.
Sets the incremental amount of the output frequency (above Maximum Speed)
allowable for functions such as slip compensation. See
.
Maximum Speed + Overspeed Limit
must be
≤
to Maximum Frequency.
Figure 38 - Speed Limits
Sets a frequency at which the drive will not operate (also called an
avoidance
frequency
). Requires that both Skip Frequency 1...3 and Skip Frequency Band
(87) be set to a value other than 0.
ATTENTION:
You are responsible for ensuring that driven machinery, all drive-
train mechanisms, and application material are capable of safe operation at the
maximum operating speed of the drive. Overspeed detection in the drive
determines when the drive shuts down. See
. Failure to observe this
precaution could result in bodily injury.
83
Overspeed Limit
Range:
0.0...20.0 Hz [0.1 Hz]
Default:
10.0 Hz
Access:
1
Path:
Speed Command > Spd Mode & Limits
See also:
55, 82
84
85
86
Skip Frequency 1
Skip Frequency 2
Skip Frequency 3
Range:
-/+250.0 [0.1 Hz]
Default:
0.0 Hz
Access:
1
Path:
Speed Command > Spd Mode & Limits
See also:
87
Allowable Output Frequency Range
Bus Regulation or Current Limit
V
o
l
t
a
g
e
Frequency
Allowable Output Frequency Range
Normal Operation
Allowable Reference Frequency Range
Frequency Trim due to
Speed Control Mode
Max Volts
Motor Volts
Break Volts
Start Boost
Run
0
Min
Speed
Motor
Hz
Max
Speed
Output
Freq Limit
Max
Freq
Break
Frequency
Overspeed
Limit
Summary of Contents for Allen-Bradley LiquiFlo 2.0
Page 1: ...LiquiFlo 2 0 AC Drive User Manual OriginalInstructions ...
Page 6: ...6 Rockwell Automation Publication D2 3518 4 January 2020 Table of Contents Notes ...
Page 8: ...8 Rockwell Automation Publication D2 3518 4 January 2020 Preface Notes ...
Page 12: ...12 Rockwell Automation Publication D2 3518 4 January 2020 Chapter 1 Introduction Notes ...
Page 34: ...34 Rockwell Automation Publication D2 3518 4 January 2020 Chapter 2 About the Drive Notes ...
Page 68: ...68 Rockwell Automation Publication D2 3518 4 January 2020 Chapter 8 Programming Basics Notes ...
Page 267: ......