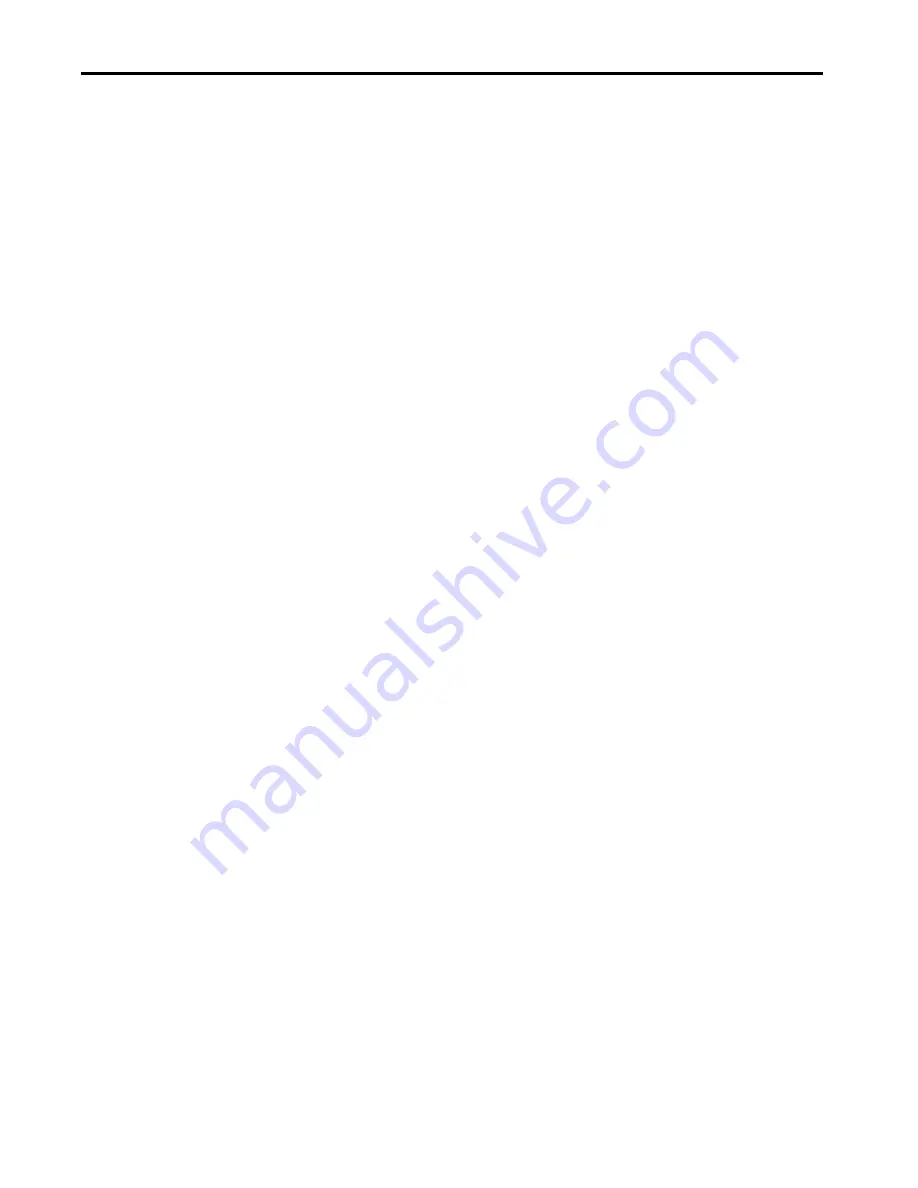
152
Rockwell Automation Publication D2-3518-4 - January 2020
Chapter 9
Parameter Descriptions
If the Auto/Manual input function is closed, then the drive uses one of the analog
inputs (defined by TB Man Ref Sel) as the reference. If an OIM subsequently
requests manual control (that is, Auto/Man F-Key is pressed) and then gives
control up (presses Auto/Man F-Key again), then the Auto/Manual digital input
must be opened and closed again to regain control of the manual reference.
If this input is open, then the terminal block does not request manual control of
the reference. If no control device (including the terminal block) is currently
requesting manual control of the reference, then the drive uses the normal
reference selection mechanisms.
19 = Local
20 = Acc2 & Dec2:
A single input function is used to select between Accel Time
1/Decel Time 1 and Accel Time 2/Decel Time2.
If the function is open, the drive uses Accel Time 1 as the acceleration rate and
Decel Time 1 as the deceleration rate. If the function is closed, the drive uses
Accel Time 2 as the acceleration rate and Decel Time 2 as the deceleration rate.
21, 22 = Accel 2, Decel 2:
One input function (called Accel 2) selects between
Accel Time 1 and Accel Time 2, and another input function (called Decel 2)
selects between Decel Time 1 and Decel Time 2. The open state of the function
selects Accel Time 1 or Decel Time 1, and the closed state selects Accel Time 2 or
Decel Time 2.
23, 24 = MOP Increment, MOP Decrement:
The MOP is a reference setpoint
(called the MOP Value) that can be incremented and decremented by external
devices. These input functions are used to increment and decrement the Motor
Operated Potentiometer (MOP) value inside the drive. The MOP value is
retained through a power cycle. The current MOP value is visible in inverter
parameter MOP Frequency (11).
• While the MOP Increment input is closed, the MOP value increases at
rate contained in MOP Rate (195). Units for rate are Hz per second.
• While the MOP Decrement input is closed, MOP value decreases at rate
contained in MOP Rate (195). Units for rate are Hz per second.
• If both the MOP Increment and MOP Decrement inputs are closed, the
MOP value stays the same.
• In order for the drive to use the MOP value as the current speed reference,
either Speed Ref A Sel must be set to MOP.
25 = Excl Link:
The state of this input is passed through to the
Input x Link
function of a digital output. See inverter parameters 380...387.
26 = PI Enable:
If this input function is closed, the operation of the Process PI
loop is enabled.
If this input function is open, the operation of the Process PI loop is disabled.
Summary of Contents for Allen-Bradley LiquiFlo 2.0
Page 1: ...LiquiFlo 2 0 AC Drive User Manual OriginalInstructions ...
Page 6: ...6 Rockwell Automation Publication D2 3518 4 January 2020 Table of Contents Notes ...
Page 8: ...8 Rockwell Automation Publication D2 3518 4 January 2020 Preface Notes ...
Page 12: ...12 Rockwell Automation Publication D2 3518 4 January 2020 Chapter 1 Introduction Notes ...
Page 34: ...34 Rockwell Automation Publication D2 3518 4 January 2020 Chapter 2 About the Drive Notes ...
Page 68: ...68 Rockwell Automation Publication D2 3518 4 January 2020 Chapter 8 Programming Basics Notes ...
Page 267: ......