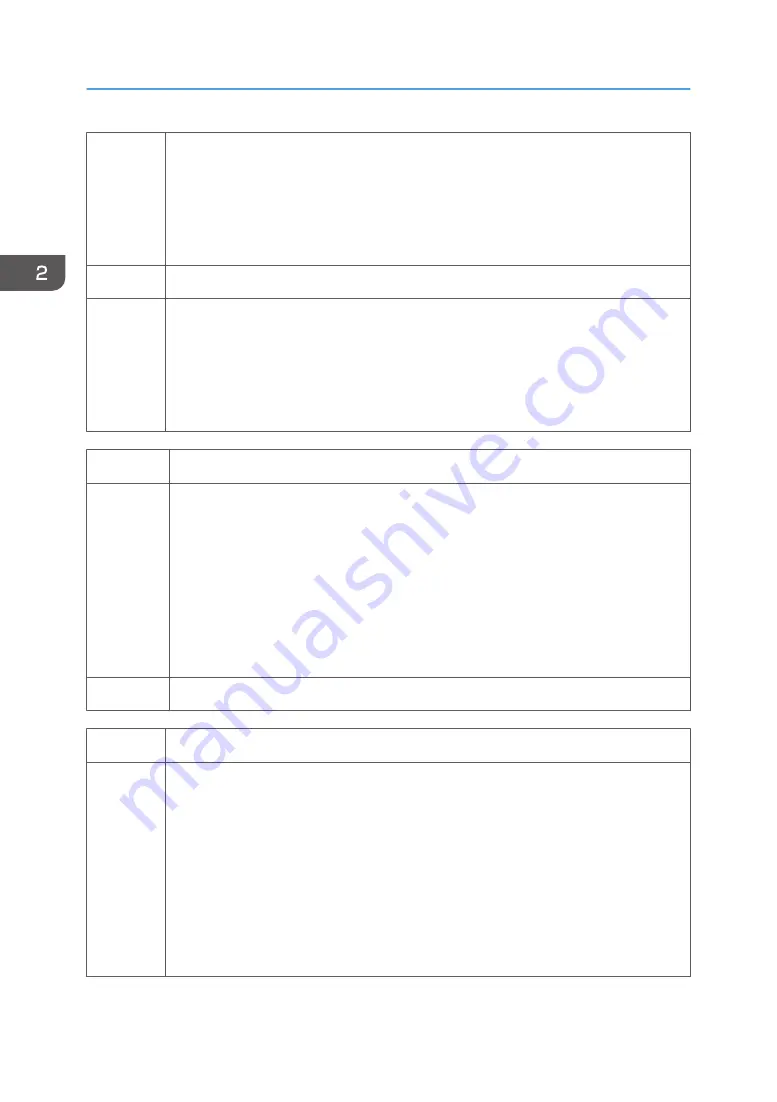
This SP adjusts the threshold for the tank full alert for the left ink sump at the far left side
of the machine.
• The left ink sump has no ID chip.
• Changing this SP setting changes the threshold value stored in NVRAM.
[1 to 800/500/1 ml]
6 Waste Ink Box: Left Near Full Threshold
This SP adjusts the threshold for the tank near-full alert for the left ink sump at the far left
side of the machine.
• The left ink sump has no ID chip.
• Changing this SP setting changes the threshold value stored in NVRAM.
[1 to 100/85/1 %]
2510
Flushing Magnification DFU
The SP adjusts the amount of ink that is purged from the ink heads at the beginning of a
print job. Increasing the number of drops purged before printing, prevents image
streaking. Consider raising this setting in an environment where the print heads may
have a tendency to dry out:
• If the machine is remaining idle for long periods.
• Where the ambient humidity is low.
• When the machine is switching infrequently between monochrome and color
printing.
[1 to 20/1/0.1]
2513
Mainten. after Leftover Thresh` DFU
Even with the print heads capped, if the machine remains idle for a long period, this can
cause the ink around the nozzles to dry slightly and become too viscous to produce
good quality images. To prevent this, the machine will execute a maintenance cycle
appropriate for the length of time that the machine has remained idle. This is done
automatically without intervention by the operator after the machine is turned on, or after
a print head has not been used for a long period of time.
These SP codes allow you to set the threshold settings that trigger SP2520 and SP2521:
• SP2520 - Maintenance On/Off Switch
• SP2521 - Number of maintenance cycle repetitions
2. Appendix 2: Service Program Mode
76
Summary of Contents for Mo-C1
Page 1: ...Model Mo C1 Machine Code D124 Field Service Manual November 2012...
Page 2: ......
Page 32: ...30...
Page 192: ...3 Preventive Maintenance 190...
Page 225: ...2 On the right disconnect the torque limiter plate x2 3 Remove the plate Common Procedures 223...
Page 257: ...5 Separate the bracket and the switches 6 Disconnect the switches x2 Scanner 255...
Page 263: ...2 Remove the center plate 3 On the right side A remove leaf plate B x1 Scanner 261...
Page 313: ...2 Remove the sensor x4 3 Disconnect the sensor x1 Reinstallation Roll Units 311...
Page 350: ...1 Disconnect the pre registration sensor x1 x1 x1 x4 4 Replacement and Adjustment 348...
Page 364: ...4 Replacement and Adjustment 362...
Page 379: ...2 Disconnect the sensor x1 3 Separate the bracket and sensor x4 Reinstallation Sub Scan 377...
Page 381: ...3 Separate the motor and bracket x4 Sub Scan 379...
Page 387: ...3 Remove the front cover x2 4 Remove the left cover of the carriage unit x1 Carriage Unit 385...
Page 469: ...2 Remove the ink cartridges 3 Disconnect the ink supply unit frame x3 Ink Supply 467...
Page 529: ...Switches 527...
Page 560: ...4 Replacement and Adjustment 558...
Page 594: ...5 System Maintenance Reference 592...
Page 608: ...SC300 Not Used There are no Group 300 service codes for this machine 6 Troubleshooting 606...
Page 628: ...SC700 Not Used There are no Group 700 service codes for this machine 6 Troubleshooting 626...
Page 660: ...Make sure bold was selected in the application 6 Troubleshooting 658...
Page 695: ...No Rating FU1 Break capacity 50V 16ADC Rated current 0 63A Fuses 693...
Page 696: ...6 Troubleshooting 694...
Page 700: ...MEMO 698...
Page 701: ...MEMO 699...
Page 702: ...MEMO 700 EN...
Page 703: ...Model Mo C1 Machine Code D124 Appendices October 2012...
Page 704: ......
Page 706: ...2...
Page 1051: ...MEMO 347...
Page 1052: ...MEMO 348 EN...