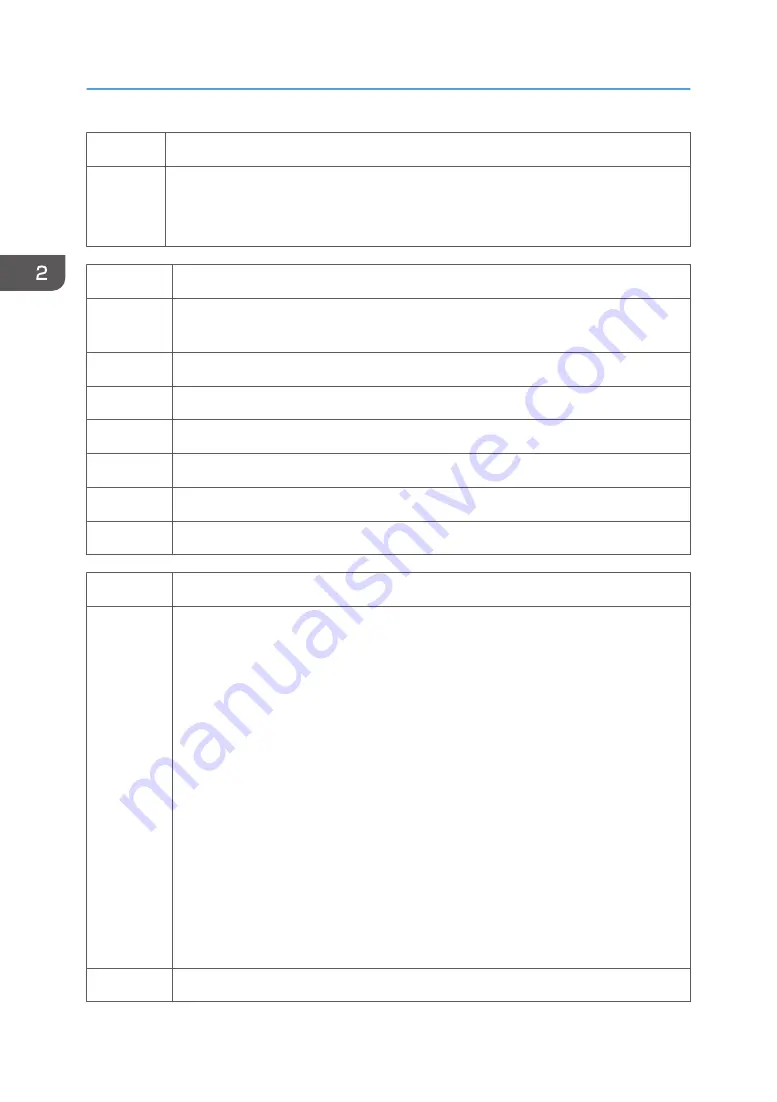
4 Correcting Length
The length of paper feed to correct skew. The vertical motor rotates forward while the
roll feed motor in the roll feeder rotates in reverse.
[300 to 2000/800/100 mm]
1953
Skewed Value Indication DFU
Use these SPs to display previous readings done with the DRESS sensor during skew
correction.
1 Current Skewed Value
[0 to 10/0/0.01 %]
2 Previous Skewed Value
[0 to 20/0/0.01 %]
3 Preceding Previous Skewed Value
[0 to 20/0/0.01 %]
1955
Suction Fan Duty Correction DFU
These SP codes adjust the operation of the transport fan during paper feed. The
efficiency of roll paper feed can be affected by temperature, humidity, paper type, and
paper size. The suction of the transport fan below the perforated platen keeps the
paper flat during printing. There are three Duty phases applied to change the speed of
the motor to create more suction.
• Duty 1. When the DRESS sensor switches on, the fan motor is in Duty 1 phase
while the paper feeds up to 79 mm past the registration standby position.
Strongest suction.
• Duty 2. After the paper has fed more than 79 mm, the motor enters the Duty 2
phase. Strong suction.
• Duty 3. When the leading edge of the paper reaches the cutting position, the fan
enters Duty 3 phase. Normal suction.
When the cutter reaches the left side of the machine after performing the cut, the cutter
return switch switches on, and reverses the cutter motor to return the cutter to its home
position on the right side of the machine, and also shifts the paper transport fan down
into Duty 2 phase.
1 Suction Fan
2. Appendix 2: Service Program Mode
38
Summary of Contents for Mo-C1
Page 1: ...Model Mo C1 Machine Code D124 Field Service Manual November 2012...
Page 2: ......
Page 32: ...30...
Page 192: ...3 Preventive Maintenance 190...
Page 225: ...2 On the right disconnect the torque limiter plate x2 3 Remove the plate Common Procedures 223...
Page 257: ...5 Separate the bracket and the switches 6 Disconnect the switches x2 Scanner 255...
Page 263: ...2 Remove the center plate 3 On the right side A remove leaf plate B x1 Scanner 261...
Page 313: ...2 Remove the sensor x4 3 Disconnect the sensor x1 Reinstallation Roll Units 311...
Page 350: ...1 Disconnect the pre registration sensor x1 x1 x1 x4 4 Replacement and Adjustment 348...
Page 364: ...4 Replacement and Adjustment 362...
Page 379: ...2 Disconnect the sensor x1 3 Separate the bracket and sensor x4 Reinstallation Sub Scan 377...
Page 381: ...3 Separate the motor and bracket x4 Sub Scan 379...
Page 387: ...3 Remove the front cover x2 4 Remove the left cover of the carriage unit x1 Carriage Unit 385...
Page 469: ...2 Remove the ink cartridges 3 Disconnect the ink supply unit frame x3 Ink Supply 467...
Page 529: ...Switches 527...
Page 560: ...4 Replacement and Adjustment 558...
Page 594: ...5 System Maintenance Reference 592...
Page 608: ...SC300 Not Used There are no Group 300 service codes for this machine 6 Troubleshooting 606...
Page 628: ...SC700 Not Used There are no Group 700 service codes for this machine 6 Troubleshooting 626...
Page 660: ...Make sure bold was selected in the application 6 Troubleshooting 658...
Page 695: ...No Rating FU1 Break capacity 50V 16ADC Rated current 0 63A Fuses 693...
Page 696: ...6 Troubleshooting 694...
Page 700: ...MEMO 698...
Page 701: ...MEMO 699...
Page 702: ...MEMO 700 EN...
Page 703: ...Model Mo C1 Machine Code D124 Appendices October 2012...
Page 704: ......
Page 706: ...2...
Page 1051: ...MEMO 347...
Page 1052: ...MEMO 348 EN...