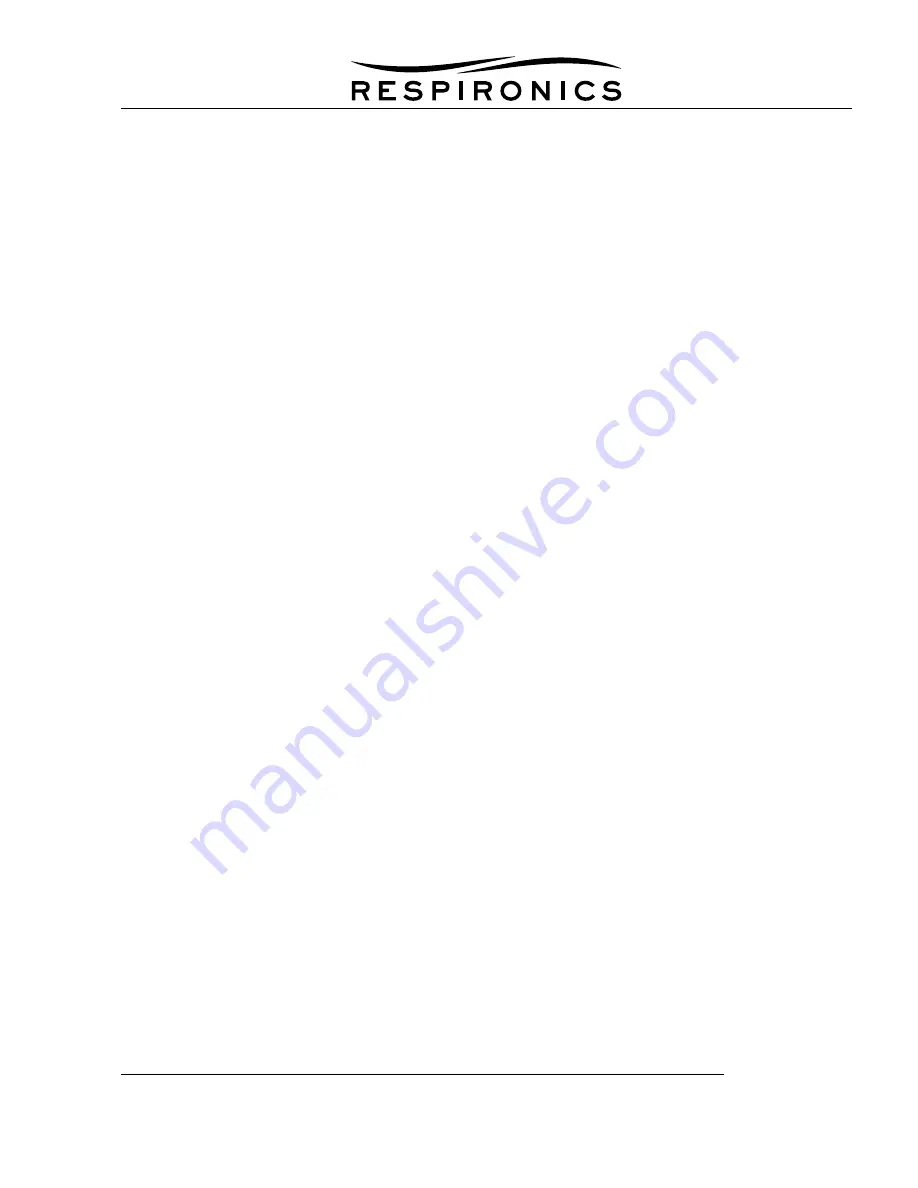
P
AGE
4-3
T
RILOGY
S
ERVICE
& T
ECHNICAL
I
NFORMATION
1002735, V
ER
. 05
Boost Converter -
The boost converter (U1) generates the regulated 29VDC supply used by the system
board. When the AC/DC power supply output voltage is greater than 28VDC the boost converter is OFF. If the
AC/DC power supply is not available one of the battery sources is selected. The boost converter will then boost
that battery voltage to 29VDC. When the input to the boost converter falls below 7VDC it is disabled.
Power Path Controller -
The power path controller (U6) selects either the battery power supply or the AC/DC
power supply to run the ventilator. When AC/DC supply is available the power path controller turns ON the AC/
DC supply MOSFET (Q20) allowing the boost converter to receive its power from the AC/DC supply. When AC/
DC supply in not available the power path controller turns ON the two parallel battery MOSFETs (Q25 & Q26)
allowing the boost converter to receive its power from the battery supply. Initially, upon power up the circuitry
powers the system with these MOSFETs acting as forward biased diodes until the sense and status lines for
the power path controller have reached equilibrium.
Power Mux -
The power path switch driver (U2) selects either the Pb-acid battery source or the lithium ion
battery source to power the system. It does so by controlling 4 N-channel MOSFETs (Q11, Q12, Q13, & Q14)
configured as two back to back ideal diode sources. This circuitry also disables all battery current when Trilogy
enters the low power state by turning the N-Channel MOSFETs OFF.
Smart Battery System Manager -
The smart battery system manager (U3) controls both the internal and
detachable lithium ion batteries. Both batteries are equipped with smart technology and communicate with the
power management board using the standard SMBus protocol. The smart battery system manager allows the
CPU to communicate with either battery and contains memory for battery status and charger information while
simultaneously monitoring the status and alarms bits of both batteries to prevent hazardous operation of either
battery.
The software queries battery information about once per second. If the detachable lithium ion battery is
disconnected, the comparator (U3) will quickly switch power to the internal lithium ion battery. Thereby
continuing to power the system before the software realizes that a disconnect has happened. This comparator
also prevents the software from disabling the internal lithium ion battery when there is no detachable battery
present. The detachable battery is only disabled by the software if the software determines it to be a counterfeit
battery.
Each lithium ion battery will power the system until its capacity falls below 10% of its full charge capacity. When
both the lithium ion batteries are at less than 10% of the full charge capacity, they share the current drawn by
the ventilator. This is done such that the battery with the greater capacity provides more current and both
batteries reach 0% capacity simultaneously.
When both lithium ion batteries are at less than 100% charge capacity, both batteries share a maximum of 2A
charge current according to their relative charge state. This is done such that the battery with less capacity
receives greater charge current and both batteries reach 100% capacity simultaneously. The charge voltage
and current limit used for each lithium ion battery is set at 16.9V and 2A respectively using resistors (R39,
R35). In addition, the current sense resistor (R26) disables the battery charging operation when the total
current output from the power supply exceeds 4A to prevent overloading of the power supply.
The smart battery system manager also generates an internal 5VDC supply to control all internal functions
from the greatest available power source. A voltage divider network (R28 & R38) sets the AC present threshold
at 22VDC coming from the AC/DC power supply. The smart battery system manger (U3) uses an internal
comparator with a 1.19V reference to determine if AC is present.
Half Bridge Buck Converter -
The buck converter (Q17, Q18, L4, & C33) generates the lithium ion battery
charge voltage for both the lithium ion batteries. The charge switch is controlled by the smart battery system
manager (U3).
Charge Switch -
The charge switches (Q3, Q4, Q5, & Q6) facilitate charge current sharing between the two
lithium ion batteries when they simultaneously request a charge. It is controlled by the smart battery system
manager (U3) which provides charge current inversely proportional to the relative battery capacity using the
charge switch.
Summary of Contents for Trilogy 02
Page 1: ...Trilogy 100 Trilogy 200 Trilogy 02 Trilogy 202 Service Technical Information ...
Page 177: ...PAGE 8 16 TRILOGY SERVICE TECHNICAL INFORMATION 1002735 VER 05 3 4 5 ...
Page 181: ...PAGE 8 20 TRILOGY SERVICE TECHNICAL INFORMATION 1002735 VER 05 6 ...
Page 184: ...PAGE 8 23 TRILOGY SERVICE TECHNICAL INFORMATION 1002735 VER 05 ...
Page 343: ...PAGE 10 40 TRILOGY SERVICE TECHNICAL INFORMATION 1002735 VER 05 ...
Page 346: ...PAGE 10 43 TRILOGY SERVICE TECHNICAL INFORMATION 1002735 VER 05 ...
Page 351: ...PAGE 10 48 TRILOGY SERVICE TECHNICAL INFORMATION 1002735 VER 05 ...
Page 352: ...PAGE 10 49 TRILOGY SERVICE TECHNICAL INFORMATION 1002735 VER 05 ...
Page 353: ...PAGE 10 50 TRILOGY SERVICE TECHNICAL INFORMATION 1002735 VER 05 ...
Page 354: ...PAGE 10 51 TRILOGY SERVICE TECHNICAL INFORMATION 1002735 VER 05 ...
Page 418: ...PAGE 12 5 TRILOGY SERVICE TECHNICAL INFORMATION 1002735 VER 05 ...
Page 419: ...PAGE 12 6 TRILOGY SERVICE TECHNICAL INFORMATION 1002735 VER 05 ...
Page 420: ...PAGE 12 7 TRILOGY SERVICE TECHNICAL INFORMATION 1002735 VER 05 ...
Page 421: ...PAGE 12 8 TRILOGY SERVICE TECHNICAL INFORMATION 1002735 VER 05 ...
Page 422: ...PAGE 12 9 TRILOGY SERVICE TECHNICAL INFORMATION 1002735 VER 05 ...
Page 423: ...PAGE 12 10 TRILOGY SERVICE TECHNICAL INFORMATION 1002735 VER 05 ...