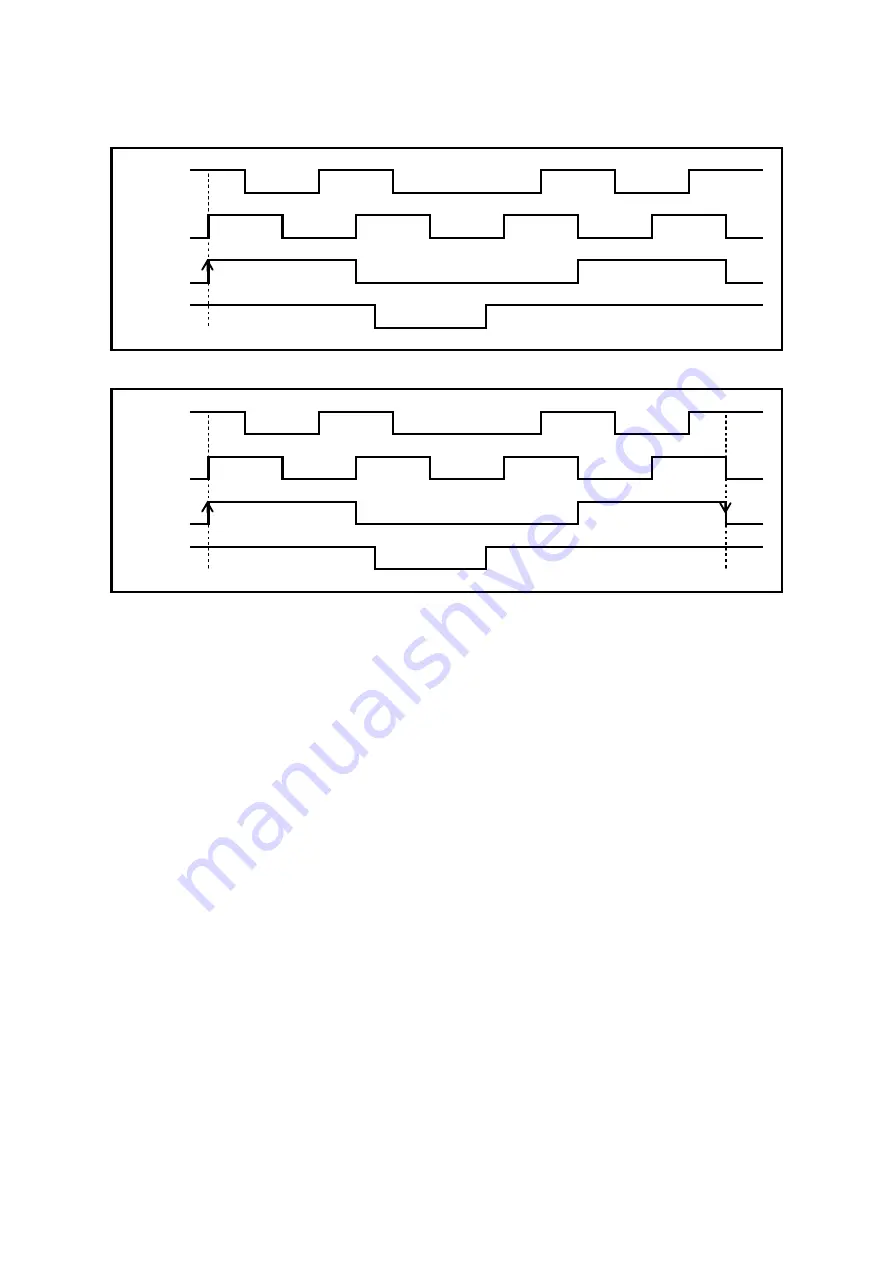
10-11
Phase A
Phase B
Z Pulse
Origin
Capture
Fig.10-14 Variable = 7
Phase A
Phase B
Z Pulse
Origin
Capture
Capture
Fig.10-15 Variable = 8 (Variable =6 and 7 OR)
10.1.6 Analog Output Variable (CHn_ANALOG_OUT!)
This variable outputs the results of digital signal processing in the PSC7000 controller. It is
an integer variable from -8192 to +8191. The value of this variable is transmitted to the
analog output circuit, and a comparable amount of voltage is output. The value out of the
range will be rounded off to the closest maximum or minimum value.
In case of MCIM-1, a value given by the analog output variable multiplied by 976.5625uV
is output to the +/-8V output terminal. Likewise, a value given by the analog output
variable multiplied by 1.220703125 mV is output to the +/-10V output terminal.
In case of MCIM-2, a value given by the analog output variable multiplied by 995.2387uV
is output to the +/-8V output terminal. Likewise, a value given by the analog output
variable multiplied by 1.244048mV is output to the +/-10V output terminal.
Since the slight offset voltage can exist, so adjust the offset value before being output as
the analog output variable in the application task or adjust the servo amplifier.
Summary of Contents for PSC7000
Page 2: ...Copyright 2015 Reliance Electric Limited All rights reserved...
Page 10: ......
Page 18: ...2 4...
Page 22: ...3 4...
Page 28: ...4 6 4 6 2 Terminal Block of PG Module and Cable Fig 4 2 Dimensions of Terminal Block...
Page 34: ...4 12...
Page 38: ...5 4...
Page 42: ...6 4...
Page 72: ...10 18...
Page 76: ...11 4...
Page 78: ...12 2...
Page 82: ...13 4...
Page 83: ......