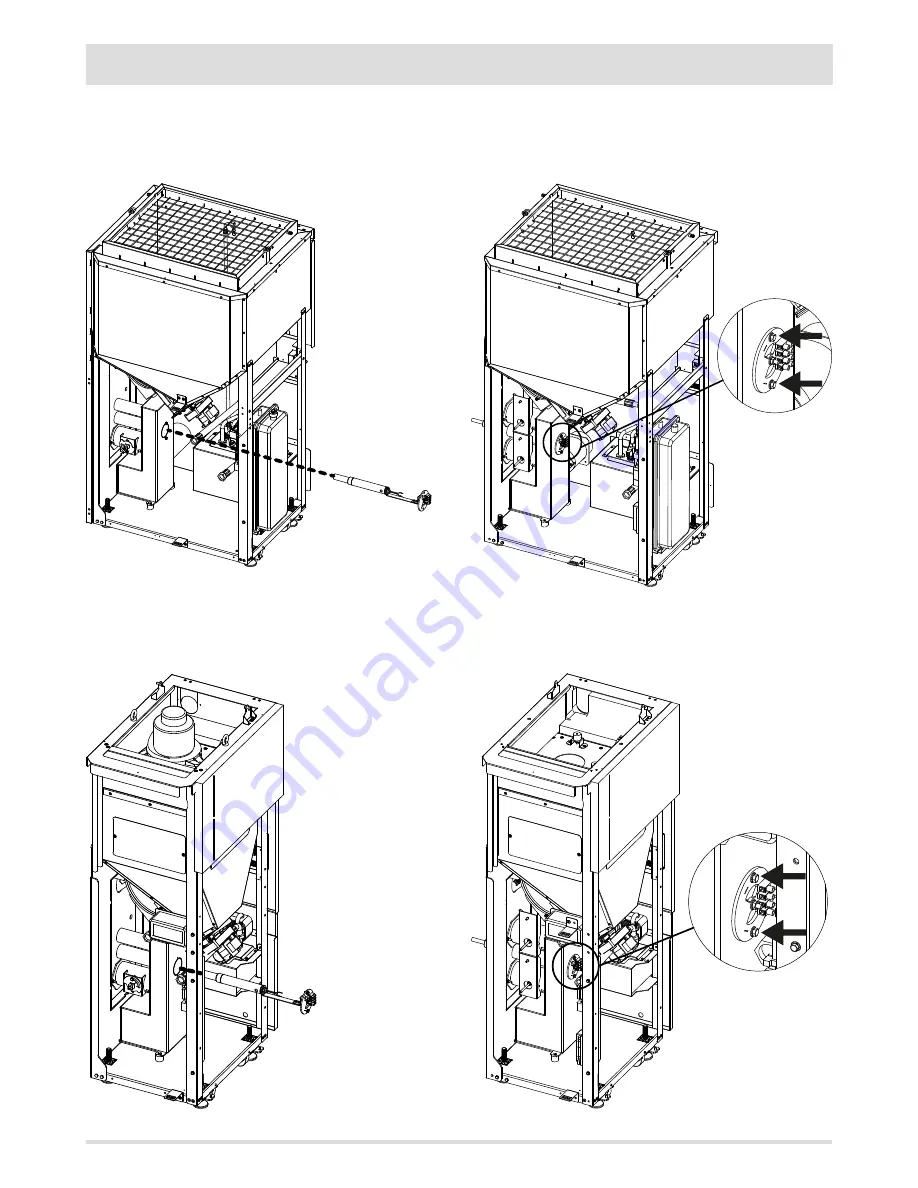
53
7 - INSTALLATION AND ASSEMBLY OF TANK
Technical Dept. - All rights reserved - Reproduction is prohibited
f) insertion of spark plug
Locate the spark plug loosely fitted in the tank and insert it fully, and fasten it in place with the two screws provided, as shown in the
figure. Apply gentle pressure to counteract the resistance of the spring and push the flange all the way down onto the structure.
DETAIL OF FASTENING OF SPARK PLUG (MANUAL TANK)
DETAIL OF FASTENING OF SPARK PLUG (REFILL TANK)
Summary of Contents for LOGIKA 25-35 REFILL
Page 52: ...50 y x S v 7 INSTALLATION AND ASSEMBLY OFTANK ASSEMBLYOFSIDEPANEL MANUALTANK ...
Page 121: ......
Page 122: ......
Page 123: ......