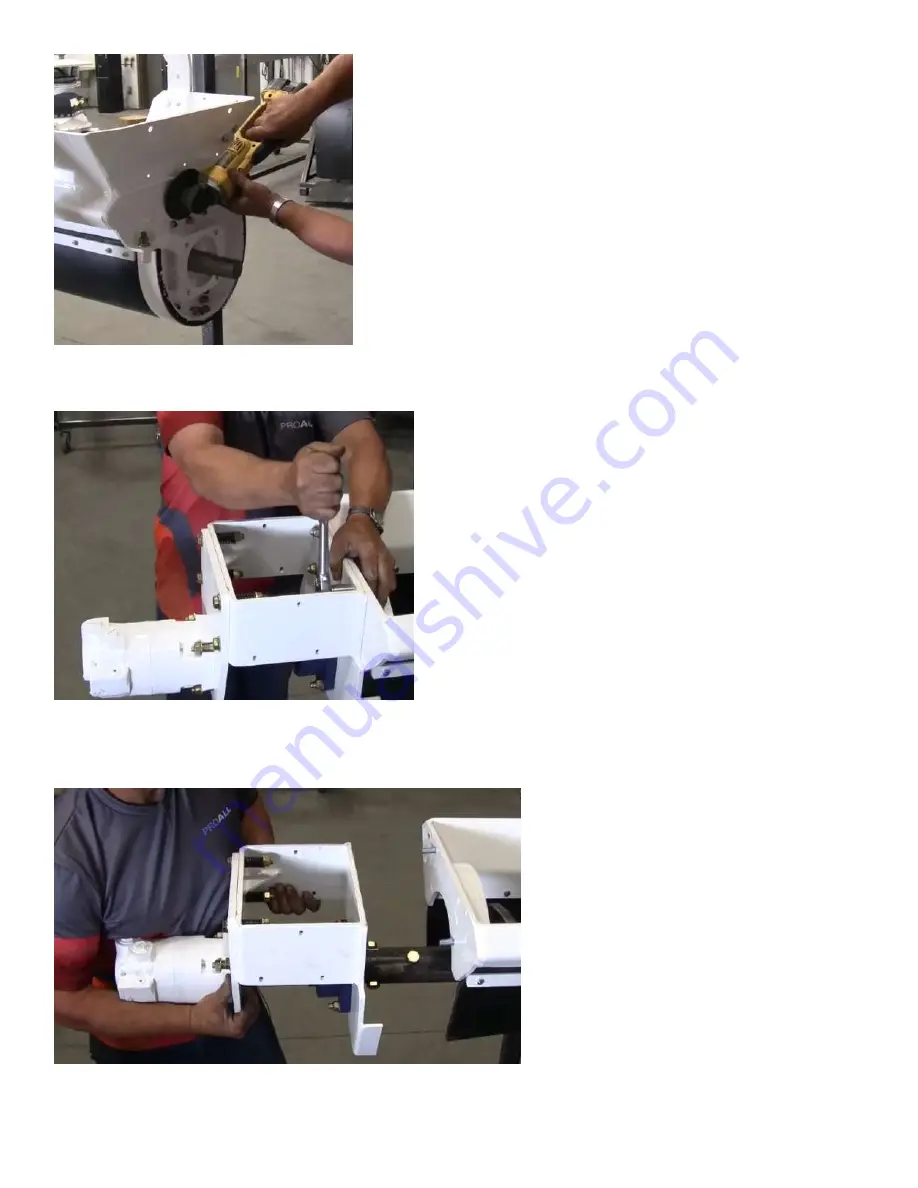
45
Figure 5. Remove idler shaft seal assembly bolts
8.
Remove 4 bolts holding the offset bracket (PN MX10006) to the mix auger frame.
Figure 6. Remove offset bracket from mix auger frame
9.
Pull the motor, housing and auger assembly towards the top of the mix auger until the auger shaft clears the
bottom of the mix auger frame.
Figure 7. Separate mix auger from bottom of mix auger frame
Summary of Contents for P Series
Page 1: ...1 PROALL Mobile Mixer Service Manual P Model MX04703 August 2020 Rev 1 0 ...
Page 20: ...20 has been removed and not replaced then the charge pressure will drop to zero C ...
Page 85: ...International Manufacturing Inc P P1 OUT IN OUT IN 2 1 3 IN S1 S2 2 1 3 OUT IN ...
Page 100: ... ADMIX 1 ADMIX 2 WORK LIGHTS ...
Page 101: ... COOLER 1 VIB1 SPARE VIB1A SPARE VIB2A VIB2 VIB3 VIB4 VIB5 ...
Page 105: ... BATTERY V BATTERY V ...