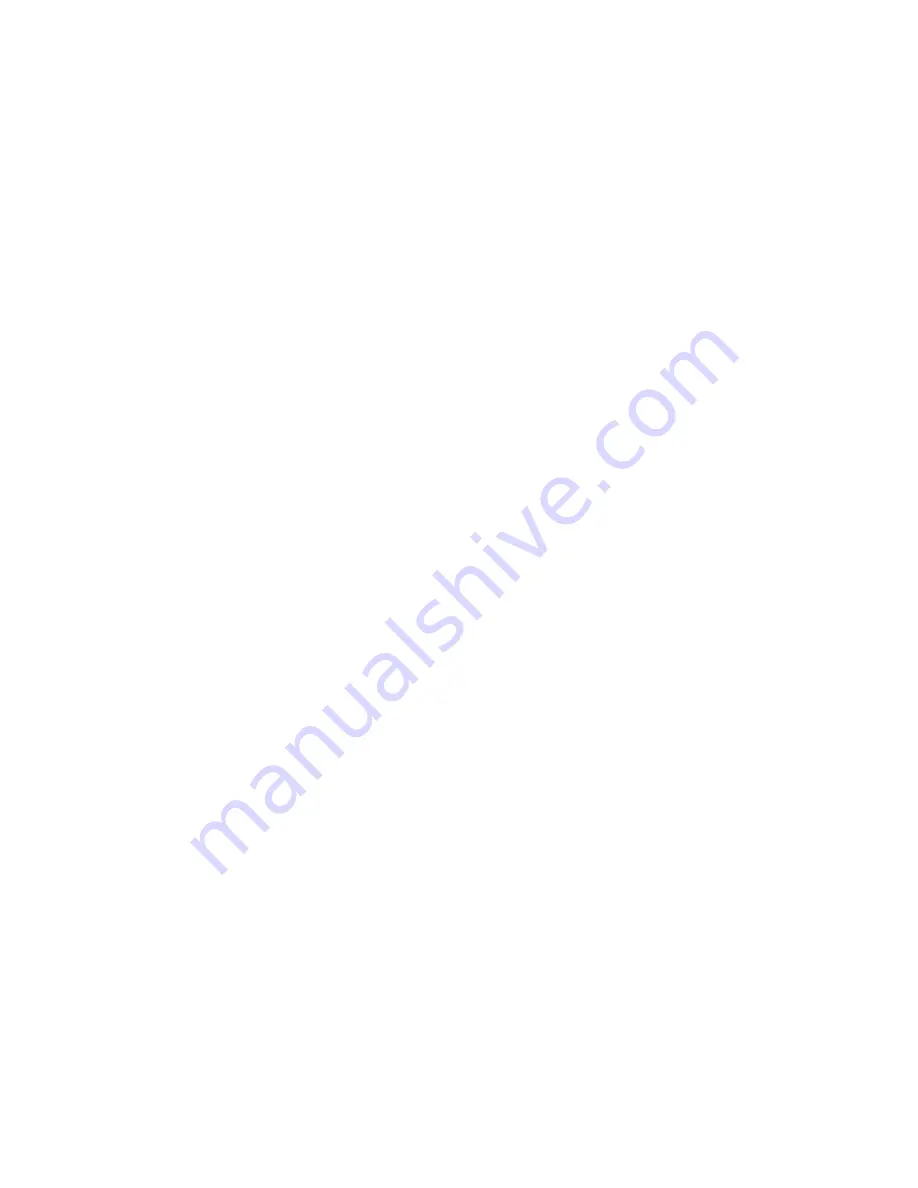
10
3.
THEORY OF OPERATION
The Commander mixer’s overall function is to dose / meter a pre-defined quantity of materials, which could be solids or
liquids and mix these materials to achieve the end product. To do this many speed controlled and flow-controlled
functions must work in unison to ensure the correct proportions are being administered.
Counts (or pulses) are used to measure and calibrate all material functions on the mixer. A count is basically just several
points in one revolution of the shaft. Calibrations are done by weighing the total material dispensed and then dividing
that by the total counts. This gives the weight per count or the amount of material dispensed between each count of
the shaft. When looking at liquid calibration each measuring device records flow as a function of pulses or counts per
unit volume.
The belt speed and counts are the basis for all dosage and total volume calculations. When belt speed is changed by the
operator all the other material dosing functions will change in relation to this change in speed. This gives the operator
the ability to change the production rate of the machine without having to change all the other material dosage
functions at the same time.
Aggregate materials are metered via gates at the outlet of the aggregate bin. These materials are calibrated based on
gate height in relation to belt counts. The higher the gate height the more weight per belt count is metered.
The speed-controlled functions operate based on RPM and counts. The counts determine the volume output based on
calibration and the RPM determines dosage or production rate. The Commander control system uses the data in the
mix design entered by the user to pre-determine required counts and RPM required. The RPM is monitored by the
Commander computer to ensure the speed is maintained and is also variable when the belt speed changes.
The flow-controlled functions operate based on flow (multiple units of measure) and counts. The counts determine the
volume output based on the flow meters k-factor (scaling). The flow determines the dosage or production rate. The
Commander control system uses the data entered in the mix design to determine the required flow rates. The flow is
monitored by the Commander computer to ensure flow is maintained and is also variable when the belt speed changes.
Since material flow measurements are the key to achieving the correct proportions it’s important that all feedback
devices are reading properly. The Commander system monitors the devices continuously during operation and will stop
the mixer if the required feedback is not correct.
Summary of Contents for P Series
Page 1: ...1 PROALL Mobile Mixer Service Manual P Model MX04703 August 2020 Rev 1 0 ...
Page 20: ...20 has been removed and not replaced then the charge pressure will drop to zero C ...
Page 85: ...International Manufacturing Inc P P1 OUT IN OUT IN 2 1 3 IN S1 S2 2 1 3 OUT IN ...
Page 100: ... ADMIX 1 ADMIX 2 WORK LIGHTS ...
Page 101: ... COOLER 1 VIB1 SPARE VIB1A SPARE VIB2A VIB2 VIB3 VIB4 VIB5 ...
Page 105: ... BATTERY V BATTERY V ...