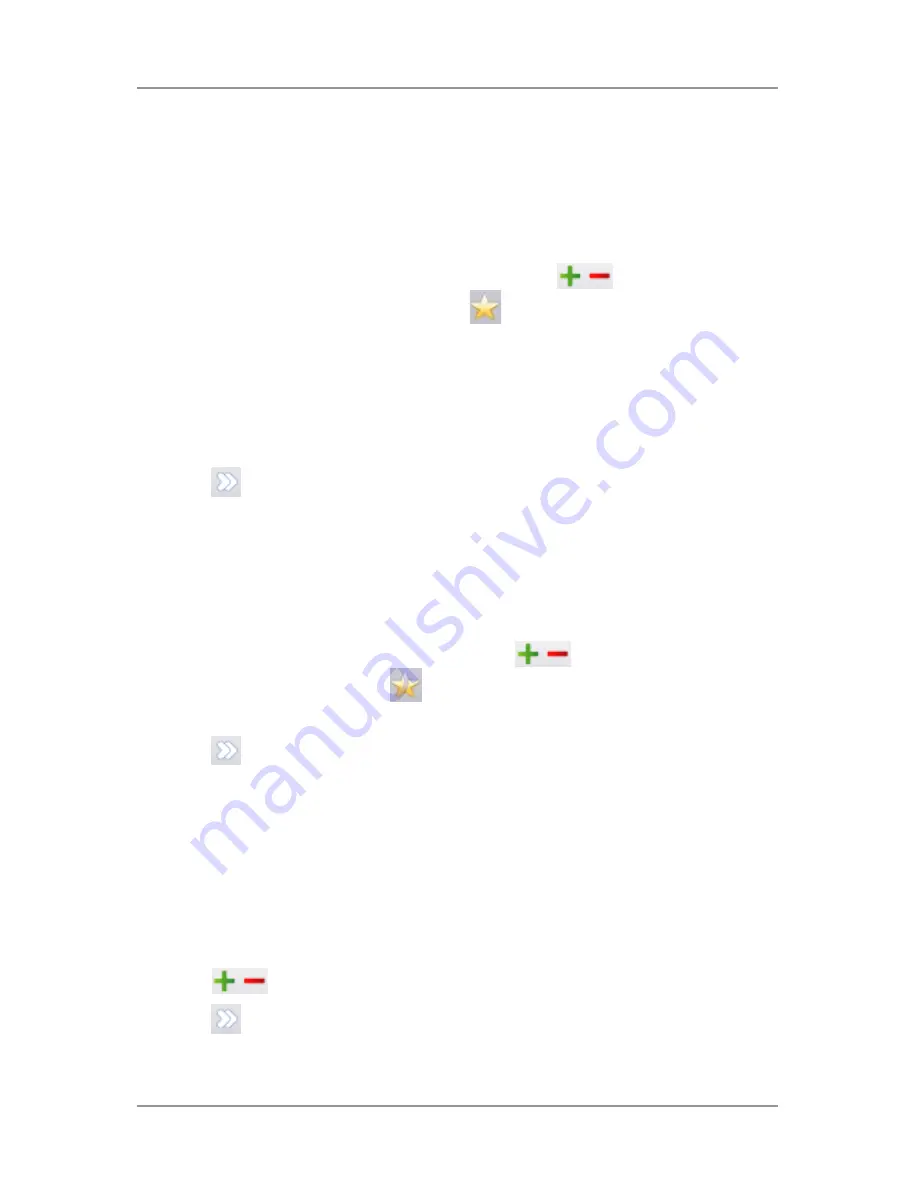
2 ● Program a Job
2-20
SV63138 Rev. A
Set Fold A
1. Select the size of the first fold required.
NOTE: Depending on the settings you made earlier for fold type and paper
length, the inserter suggests the correct dimension for the first fold. Most of
the time this setting will prove satisfactory.
2. To change the standard fold setting, tap
the
icons until the
length of required fold displays. A
icon displays next to the fold
panel you are setting.
NOTE: The inserter automatically limits your options to available specifications
on your inserter. (As you change the length of fold A, the dimension of fold
B changes automatically to keep within the correct paper length and inserter
specifications.)
3. Tap
to accept the fold value and advance to the next setting.
Set Fold B
1. Select the size of the second fold required.
NOTE: Similar to setting fold A, the inserter suggests the correct dimension
for fold B.
2. To change the standard setting, tap
the
icons
until the length of
fold required displays. A
icon displays next to the fold panel you
are setting.
3. Tap
to accept the fold value and advance to the next setting.
•
Inserting jobs
- continue to the
Set the Envelope Depth setting
.
•
Fold-only job
- there are no more job settings, skip to
Confirming
the Job Setup.
Set Envelope Depth
1. Use the scale on the front cover to measure the depth of your
envelope.
2. Tap
to scroll through the measurements (displayed in mm).
3. Tap
to accept the value and advance to the next setting.
Summary of Contents for relay 3000
Page 10: ...This page is intentionally blank ...
Page 26: ...This page is intentionally blank ...
Page 28: ...This page is intentionally blank ...
Page 50: ...This page is intentionally blank ...
Page 52: ...This page is intentionally blank ...
Page 66: ...This page is intentionally blank ...
Page 80: ...This page is intentionally blank ...
Page 82: ...This page is intentionally blank ...
Page 86: ...5 Barcode Scanning 5 6 SV63138 Rev A The diagram below is for an A4 sheet ...
Page 94: ...This page is intentionally blank ...
Page 100: ...This page is intentionally blank ...
Page 110: ...This page is intentionally blank ...
Page 112: ...SV63138 Rev A This page is intentionally blank ...
Page 119: ...This page is intentionally blank ...