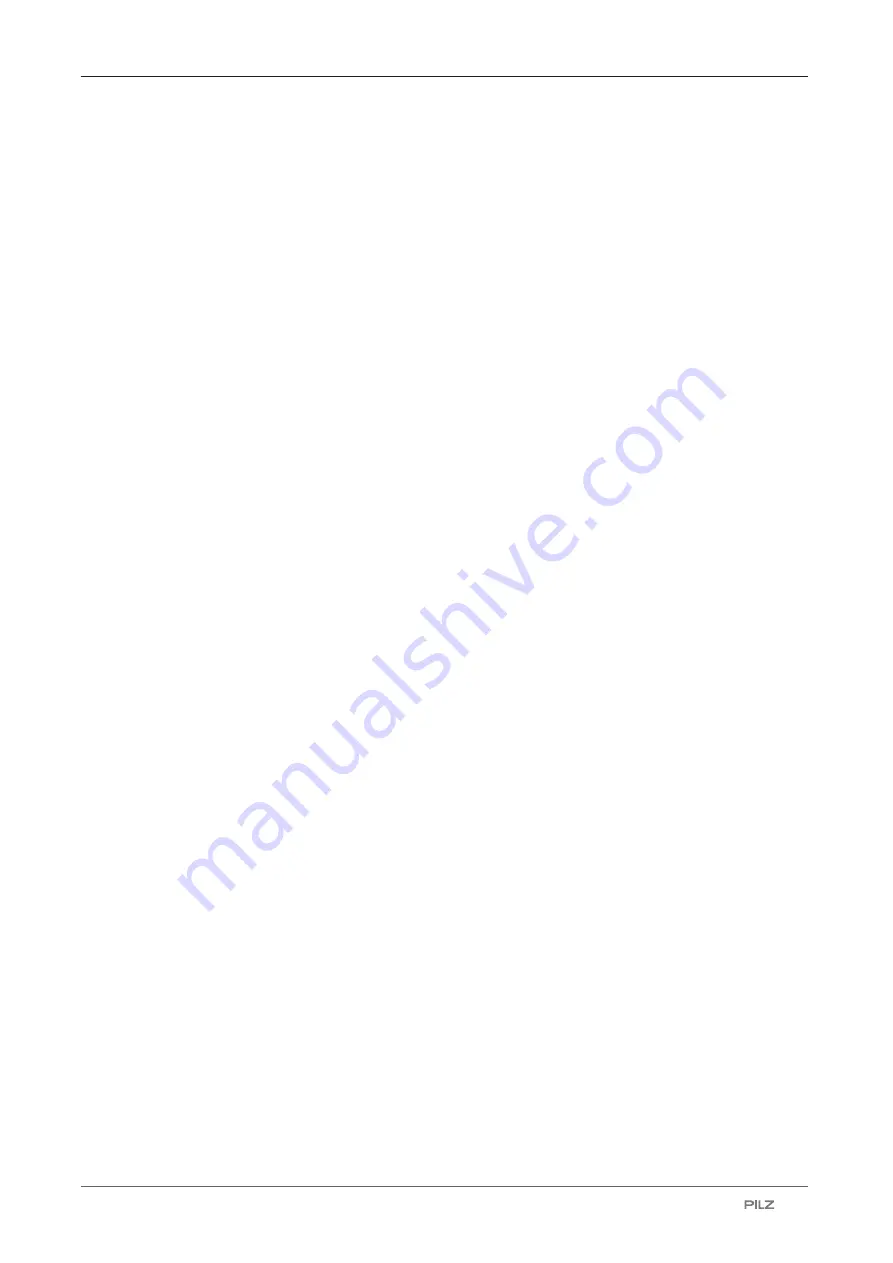
Safety
Operating Manual PSENvip R, PSENvip R LR,PSENvip E
1003449-EN-06
| 10
3
Safety
3.1
Intended use
The PSENvip is exclusively designed for stationary use on press brakes. As electrosensit-
ive protective equipment (ESPE), PSENvip meets the requirements of a type 4 ESPE in ac-
cordance with EN 61496-1.
PSENvip safeguards the danger zone below the moving upper tool.
Danger zones outside of the protected field are not protected. Hazards in the area of the
lower tool and above the protected field must be protected by the press manufacturer with
appropriate measures. Please refer to the guidelines given in the "Tool shapes" section in
this chapter.
Base version
}
A control system PSSu PLC from the automation system PSS 4000 from Pilz must be
used for safety-related evaluation of the PSENvip signals. The control system must have
the FS resource system section. The special module PSSu K F FAU B must be used for
signal evaluation.
}
The control system PSSu PLC may mute the protective function of the PSENvip if there is
a slow closing speed v ≤ 10 mm/s (creep speed mode).
}
The upward movement of the press is assumed as a safe movement.
}
The press brake must observe a max. overrun of 14 mm.
Productive version
}
Danger zone is monitored either by
– Using the fixed muting end point
The productive version of PSENvip operates as standard with the fixed muting end
point of 4 mm. With the fixed muting end point of 4 mm, the protected field monitors
the danger zone between upper tool and workpiece up to a remaining gap of 4 mm.
The control system PSSu PLC may mute the protective function of the PSENvip from
the muting end point of 4 mm (4 mm point) (muting).
Please note: The protective function of the PSENvip may be muted from a remaining
gap of 6 mm, depending on the requirements of the country in which the PSENvip is
operated and the requirements of the appropriate regulatory body.
or
– Using a configured muting end point
The protected field monitors the danger zone between the upper tool and workpiece
up to a configured remaining gap. A value between 4 mm and 1.6 mm must be con-
figured for the muting end point. The control system PSSu PLC may mute the protect-
ive function of the PSENvip from the configured muting end point (muting).
}
The upward movement of the press is assumed as a safe movement.
}
The press brake must observe a max. overrun of 14 mm.
}
A control system PSSu PLC from the automation system PSS 4000 from Pilz must be
used for safety-related evaluation of the PSENvip signals.
The control system must have the FS resource system section.