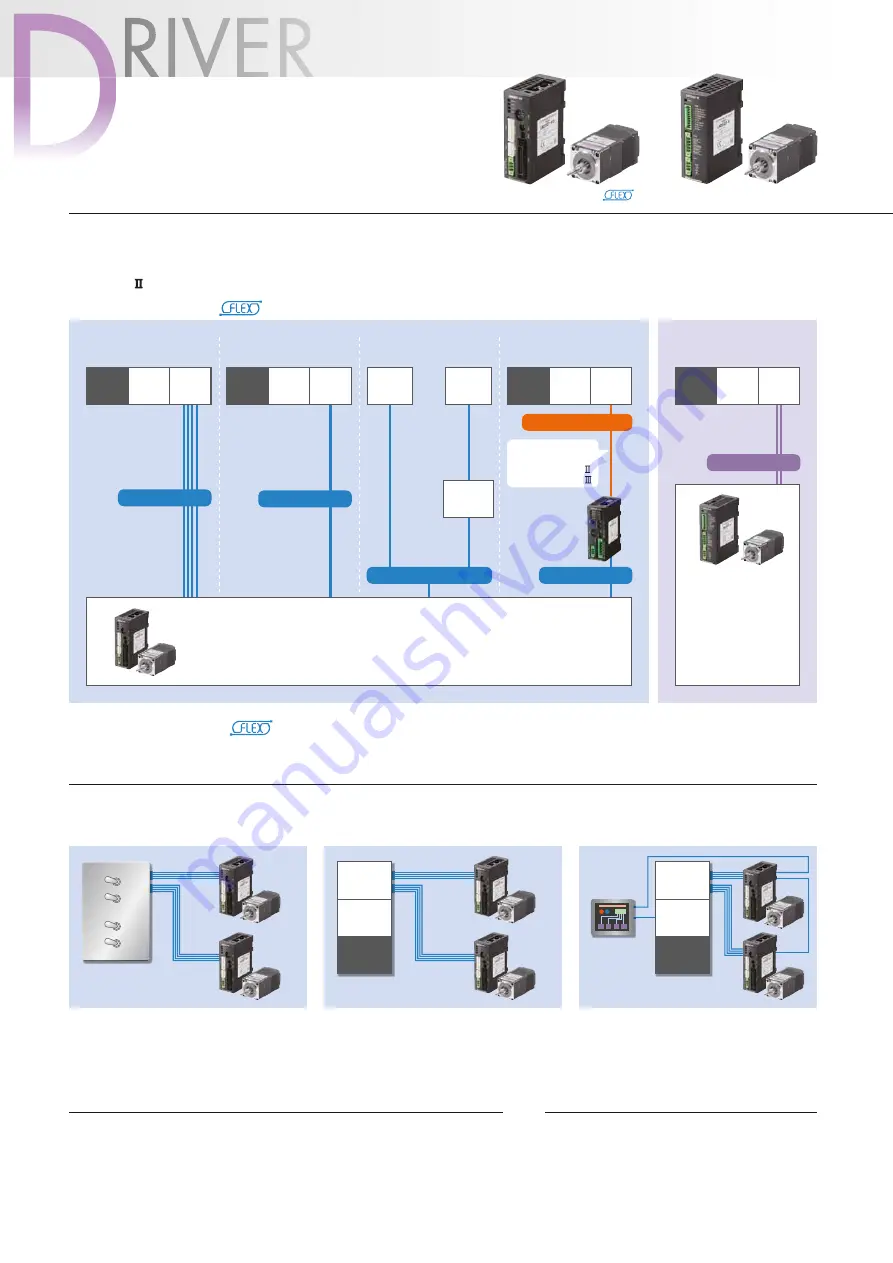
6
Driver Features [1]
2 Driver Types Selectable by System Confi guration
For the
DRL
Series driver, you can select from 2 driver types according to your host system.
Built-In Controller Type
■
Connecting Method
①
I/O
Because the positioning unit (pulse generator) function is built in to the driver, you can build an operation system using I/O by directly
connecting to a switch box or PLC. Because a positioning unit is not necessary on the PLC side, space is saved and the system is simplified.
②
Modbus (RTU)/RS-485
③
Industrial Network
Operating data and parameters can be set and operation commands can be input using RS-485
communication.
Up to 31 drivers can be connected to each serial communication unit.
Also, there is a function that enables the simultaneous start of multiple axes. The protocol supports
Modbus (RTU), enabling connection with devices such as touch-screen panel computers and PCs.
Using a network converter (sold separately) enables support
with EtherCAT communication, CC-Link communication,
and MECHATROLINK communication. Operating data and
parameters can be set and operation commands can be
input using various communication methods.
●
Example of Using PLC and a Touch Screen
Normally, the actuator is started and stopped with I/O.
Changing the operating data settings and displaying the monitors and alarms
is performed with the touch screen using Modbus (RTU) communication.
When there is a lot of setup work, changes can be easily performed on the
touch screen, and the burden of creating ladders is reduced.
●
Example of Using PLC
When using PLC, you can build an operation system by
connecting directly to an I/O unit. Because a positioning unit is
not necessary on the PLC side, space is saved and the system
is simplified.
●
Example of Using a Switch Box
Because operating data is set in the driver, the actuator can be
started and stopped simply by connecting a switch you have on
hand. Control can be performed easily without using PLC.
<Built-In Controller Type
>
<Pulse Input Type>
Built-In Controller Type
Pulse Input Type
●
When Controlling with
I/O
●
When Controlling with
Serial Communication
●
When Controlling with
an Industrial Network
Power
Supply
Unit
CPU Unit I/O Unit
Power
Supply
Unit
CPU Unit
Serial
Communication
Unit
Power
Supply
Unit
CPU Unit
Industrial
Network
Unit
Power
Supply
Unit
CPU Unit
Positioning
Unit
③
Industrial Network
②
RS-485
①
I/O
②
Modbus (RTU)
Pulse Input
Network
Converter
EtherCAT
CC-Link
MECHATROLINK-
MECHATROLINK-
Type that executes
operation by inputting
pulses into the driver.
Controls the actuator using
a positioning unit (pulse
generator) that you have
obtained yourself.
●
When Controlling from a
Computer or Touch-Screen Panel
or
Touch-
Screen Panel
Computer
Computer
Serial
Communication
Board (RS-485)
②
Modbus (RTU)
Type where the operating data is set in the driver, and the operating data is selected and executed from the host
system.
Host system connection and control is performed with
①
I/O,
②
Modbus (RTU)/RS-485 or
③
Industrial network.
When controlling with the Modbus (RTU)/RS-485 or Industrial Network, operation data etc. can be rewritten as necessary.
STRT
STOP
CCW
CW
STRT
STOP
CCW
CW
Switch Box
Power
Supply Unit
CPU Unit
I/O Unit
Power
Supply Unit
CPU Unit
I/O Unit
Touch Screen