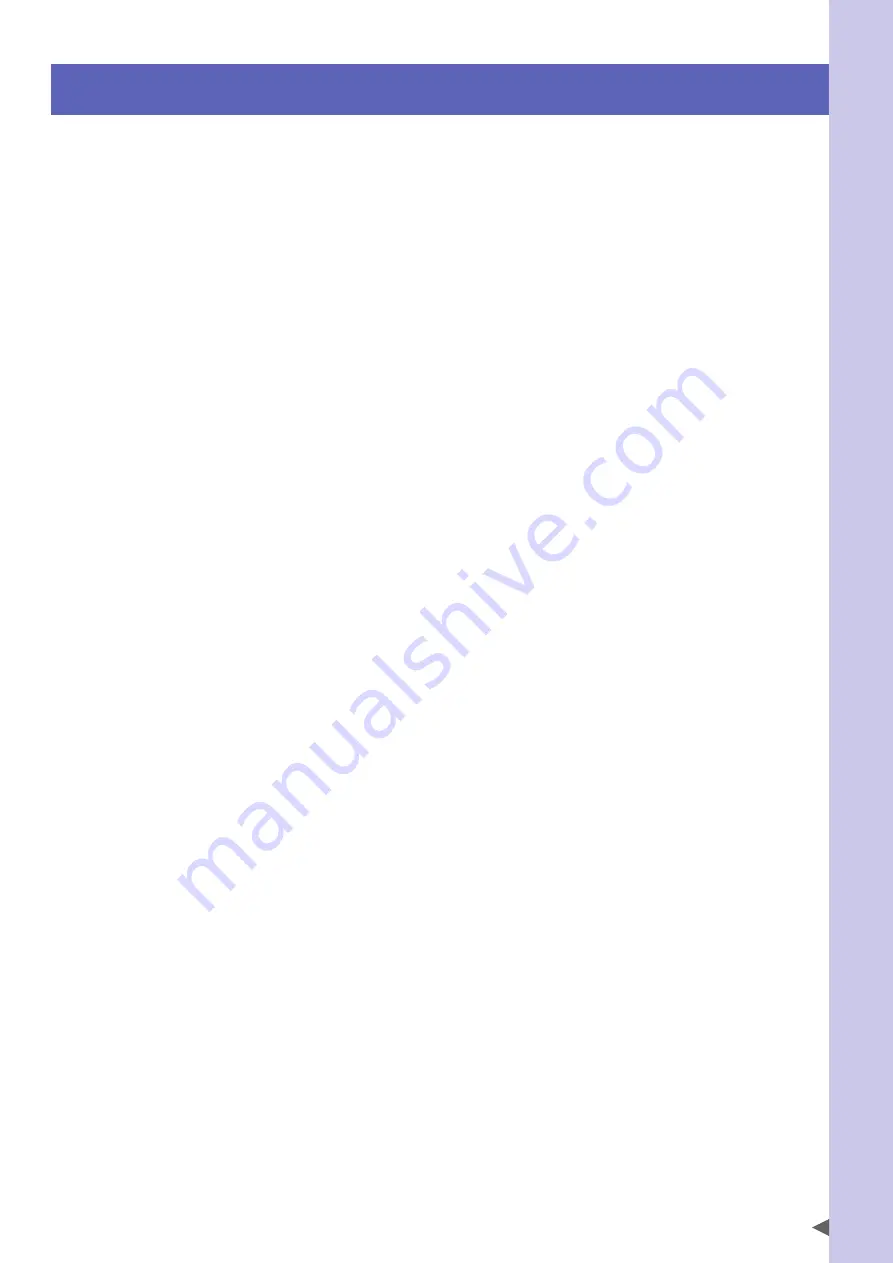
Introduction
i
Before using the robot (Be sure to read the following notes.)
Thank you for your purchase of this oMRoN Delta robot.
1.
Before using the robot, first perform the following checks and procedures.
If the following procedures are performed, it will not be possible to set the robot origin position to the same position as the default
factory setting. Consequently, it will be necessary to adjust the origin position and the robot may operate abnormally (vibration,
noise) or malfunction. Sufficient caution is therefore advised.
• Arm removal (arm position change)
The Delta robot origin position is adjusted at the factory beforehand using the jig (calibration tool) provided.
Perform the following procedure if the arm position is changed for such reasons as bending the arm when installing the robot in
order to pass through the factory.
• Adjust the arm position to the origin position with the calibration tool.
(Refer to "2. Adjusting the origin" in Chapter 3 of this manual.)
2.
Repetitive positioning accuracy
"Repetitive positioning accuracy" is not guaranteed under the following conditions.
[1] Factors related to absolute accuracy
• If accuracy between the coordinate positions (command positions) inside the robot controller and the real space positions
(moving positions) is required.
[2] Motion pattern factors
• If a motion approaching the teaching point from a different direction is included during repetitive operation.
• If the power is turned off or the robot is stopped before completing the motion or the moving speed is changed even when
approaching the teaching point from the same direction.
[3] Temperature factors
• If the ambient temperature environment changes significantly.
• If the temperature of the robot body changes.
[4] Load variation factors
• If load conditions vary during operation (the load varies depending on whether or not the workpiece is present, etc.)
3.
If the α-axis, β-axis, γ-axis or θ-axis rotation angle is small
If the α-axis, β-axis, γ-axis or θ-axis rotation angle is smaller than 5° so that it moves to almost the same position, it will be
difficult for an oil film to form on the reduction gear, possibly leading to shortened gear lifetime. With this type of operation, add
a movement so that the joint moves through 120° or more about 5 times a day.
4.
α, β and γ-axis arm rotation range and tool movement area
The robot TCp (tool center point) movement area is larger than the actual movement area. Always set the robot movement area at
the controller.
Furthermore, when the robot is making its maximum movement (including arm maximum rotation range), a sufficient space must
be secured to avoid interference with user units.
If the above points are not observed, the robot may malfunction and collide with user units, resulting in possible damage to the
robot.
Furthermore, the shafts, moveable base, or end effector may drop out, or be damaged and go flying.
(Refer to "7. Working envelope and maximum movement range" in Chapter 2 for details.)
5.
Shaft and moveable base collision prevention
The robot may be damaged if the shaft and moveable base collide. Take care to ensure that they do not collide.