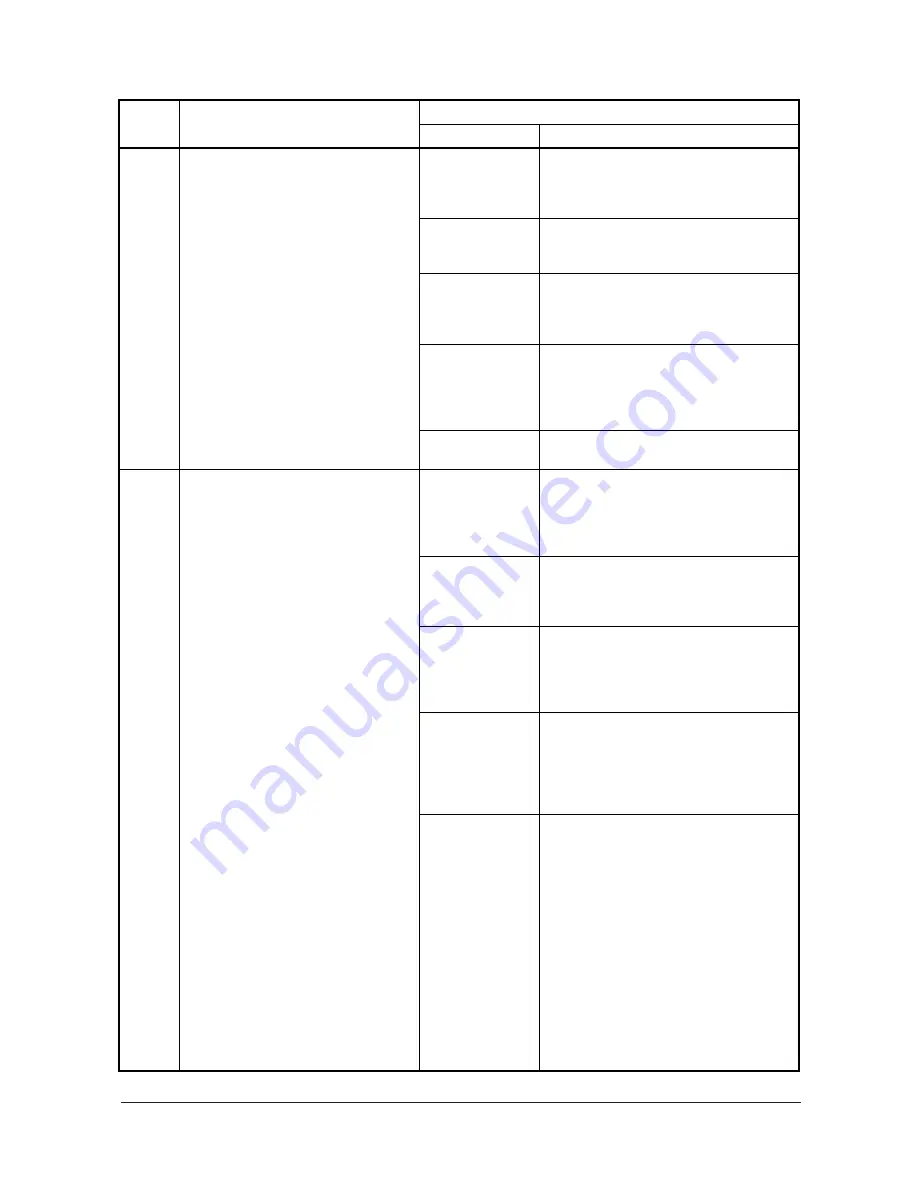
1-5-40
C8150
Document finisher* multi job tray
problem
• When the multi job tray is not detected
by the multi job tray upper limit detec-
tion sensor within 15 s from the
moment it starts ascending.
• During multi job tray descent, the multi
job tray upper limit detection sensor
does not turn off within 500 ms after it
turns on.
Loose connection
of the multi job tray
elevation motor
connector.
Reinsert the connector. Also check for conti-
nuity within the connector cable. If none,
remedy or replace the cable.
Malfunction of the
multi job tray ele-
vation motor.
Replace the multi job tray elevation motor
and check for correct operation.
Malfunction of the
multi job tray upper
limit detection sen-
sor.
Replace the multi job tray upper limit detec-
tion sensor and check for correct operation.
Loose connection
of the multi job tray
upper limit detec-
tion sensor con-
nector.
Reinsert the connector. Also check for conti-
nuity within the connector cable. If none,
remedy or replace the cable.
Defective finisher
main PWB.
Replace the finisher main PWB and check
for correct operation.
C8170
Document finisher* front upper side
registration guide problem
• During initialization, the front upper
side registration guide is not detected
in the home position within 1.5 s after
the guide returns to the home position.
JAM87 is indicated the first time this
problem occurs. If the problem occurs
after initialization when the front cover
is opened and closed, the problem is
in the front upper side registration
guide.
• When the front upper side registration
guide is operated from the home posi-
tion, the front upper side registration
home position sensor does not turn off
within 500 ms.
Loose connection
of the front upper
side registration
guide motor con-
nector.
Reinsert the connector. Also check for conti-
nuity within the connector cable. If none,
remedy or replace the cable.
Malfunction of the
front upper side
registration guide
motor.
Replace the front upper side registration
guide motor and check for correct operation.
Malfunction of the
front upper side
registration guide
home position sen-
sor.
Replace the front upper side registration
guide home position sensor and check for
correct operation.
Loose connection
of the front upper
side registration
guide home posi-
tion sensor con-
nector.
Reinsert the connector. Also check for conti-
nuity within the connector cable. If none,
remedy or replace the cable.
Defective finisher
main PWB.
Replace the finisher main PWB and check
for correct operation.
Code
Contents
Remarks
Causes
Check procedures/corrective measures
Service Manual Y104350-7
Summary of Contents for d-Copia 600
Page 1: ...d Copia 600 d Copia 800 Color Printer SERVICE MANUAL Code Y104350 7...
Page 4: ...This page is intentionally left blank iv Service Manual Y104350 7...
Page 10: ......
Page 34: ......
Page 83: ...This page is intentionally left blank...
Page 314: ...This page is intentionally left blank...
Page 454: ...UPDATINGSTATUS DATE UPDATEDPAGES PAGES CODE 02 2006 1ST EDITION 454 Y104350 7...