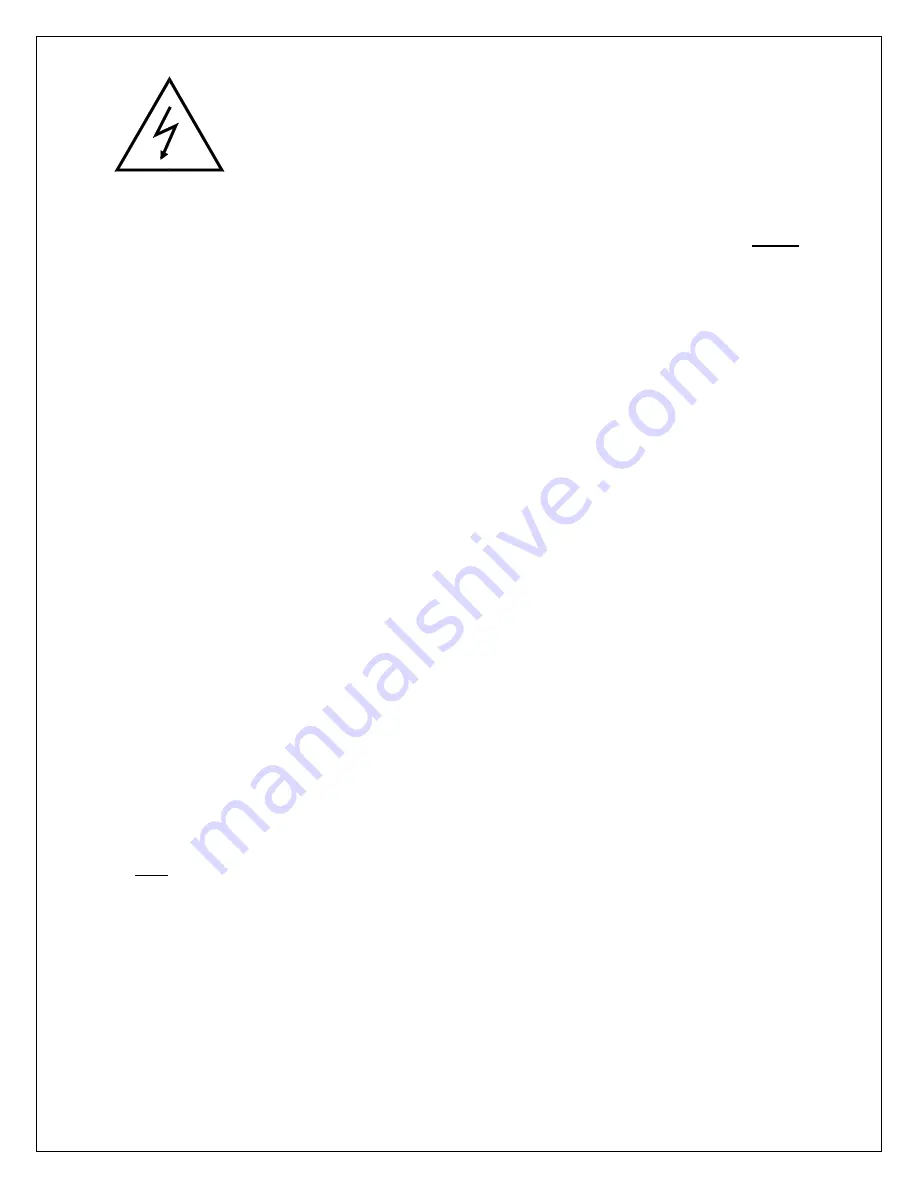
19
The electrical power should be wired to the terminal block (labeled-X1)
mounted at the rear left side on the base. Use minimum 6 AWG (16 mm²) wire for 63
Amps/phase service, 3 AWG (25 mm²) wire for 85 and 100 Amps/phase service and 2
AWG (35 mm²) wire for 140 Amp/phase service. Be sure to make connections that
comply with all appropriate electrical and safety codes.
Two different electrical configurations are also available: 4 wire system - consisting of 3
phase lines and a ground connection, and 5 wire systems - consisting of 3 phase lines, a neutral line
and a ground line. Please be aware of your requirements and wire the machine accordingly.
NOTE:
Oven may not have over current device & customer is responsible to provide it.
IV. Lighting Requirements
Keep work area well lit.
V. Exhaust Requirements
The exhaust ducting for the Asymtek oven should be designed and installed by a qualified HVAC
(heating, ventilation, and air conditioning) technician capable of calculating air flow from suction
blowers and flow losses in upstream and downstream ducting. Refer to enclosed facility install
drawing for appropriate exhaust requirements.
The latitude for exhaust airflow is quite wide and tolerant of variations in exhaust blower
efficiency. As a general guideline, exhaust volume is insufficient if an odor comes out of the oven. If
the heaters in the Cure zones are operating above 70% power during production processing, there is
too much exhaust flow.
VI. Leveling the Machine
Use a Precision bubble level with each division equal to 0.0005 inch per 10 inches, or 0.05 mm per
meter, or 10 seconds per division. Before starting, check the accuracy of your level. Set it on the
conveyor on the X-axis and record the reading. Then turn it 180
o
and the reading should be the same.
If it is not, the level is out of calibration and should be adjusted before continuing.
Screw the four leveling screws (for TCM-2200 series and two additional middle leveling screws for
TCM-3300/TCM-4600 series) at the corners until the base is 2 1/2” to 3” above the floor (or in plane
with upstream equ 0.0/ - 0.2 mm). The jam nuts on the leveling screws will be tightened at
the end of the leveling procedure.
Lower the middle leveling screws (for TCM-3300/TCM-4600 models) so that pads just make contact
w/ the floor.
Note
: These leveling procedures can be completed more efficiently by using two levels, one along the
X-axis and one along the Y-axis. Check that both levels are properly calibrated before continuing.
Leveling:
1. Place the precision bubble level on the center of the conveyor perpendicular with the product
flow (Y-axis). Level can be put on rails or conveyor belt.
2. If the bubble goes to the front of the level, then the front end of the machine is high.
Conversely, if the bubble goes to the rear, it means that the rear end is high. Raise the two
front or back leveling screws evenly until the bubble is centered. Check Y-axis first at
entrance and exit locations as in the picture. Also check middle for TCM-3300/TCM-4600
models.
Summary of Contents for TCM-2200
Page 5: ...1 Introduction ...
Page 6: ...2 ...
Page 18: ...14 ...
Page 19: ...15 Facility Installation ...
Page 20: ...16 ...
Page 26: ...22 ...
Page 27: ...23 Operating System Software Guide ...
Page 28: ...24 ...
Page 55: ...51 ...
Page 56: ...52 ...
Page 57: ...53 ...
Page 58: ...54 ...
Page 64: ...60 ...
Page 65: ...61 Standard and Optional Equipment Operating Guide ...
Page 66: ...62 ...
Page 71: ...67 Troubleshooting Guide HC1 X or HC2 controller ...
Page 72: ...68 ...
Page 74: ...70 ...
Page 95: ...91 Figure 12 ...
Page 107: ...103 Maintenance Procedure ...
Page 108: ...104 ...
Page 110: ...106 ...