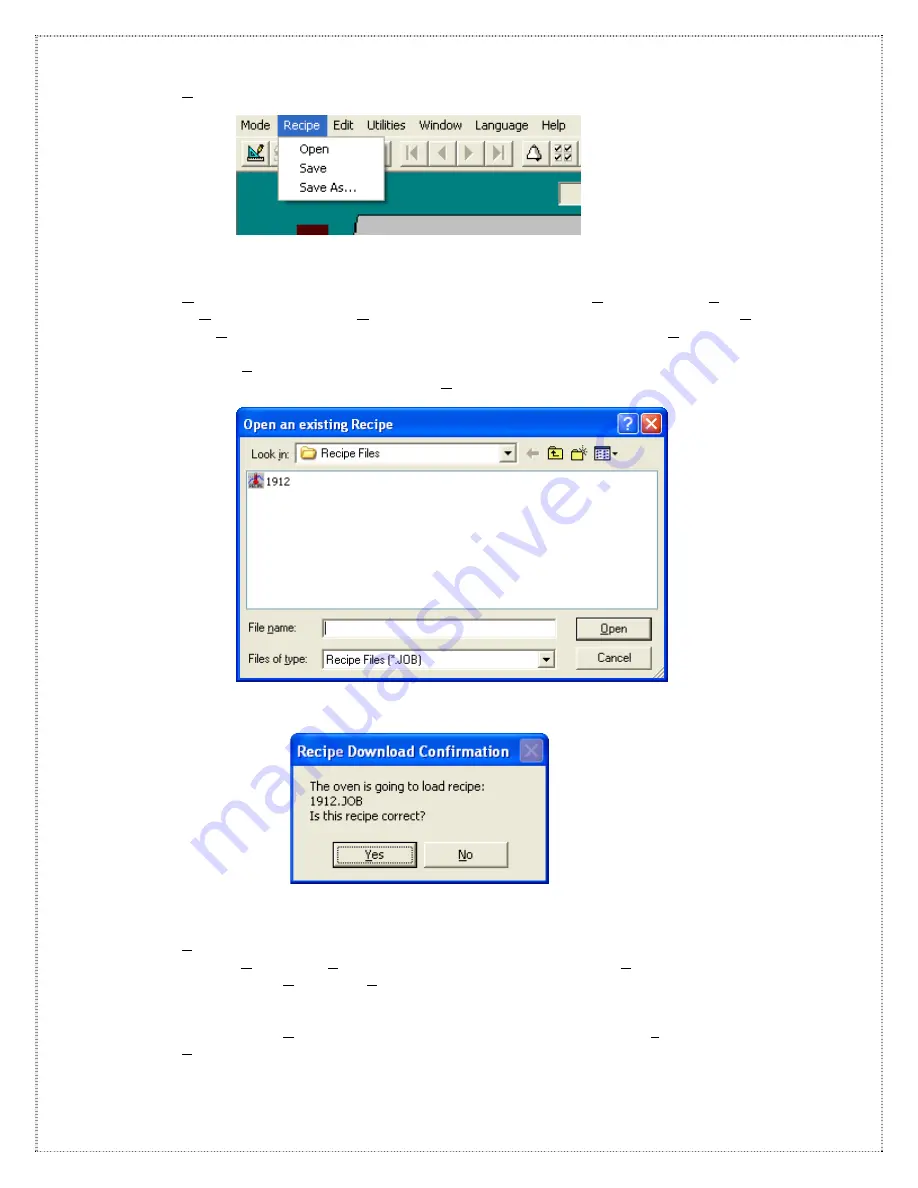
33
2. Recipe
Figure 17
a. Open recipe will prompt to open an existing recipe only in the Operate mode or Edit mode.
In Operate mode click the Open icon on the main toolbar or from the menu bar click Recipe
then Open. Select desire recipe to operate or type recipe name and click Open (
See
Figure
18
). A prompt to ensure that the selected recipe confirmation will display (
See
Figure 19
).
Clicking ‘Yes’ will allow loading an existing recipe from the recipe menu. This recipe will now
control and monitor the oven. Clicking ‘No’ will return to the recipe selection window screen.
Figure 18
Figure 19
b. Save recipe will save an active recipe under the same file name with no further prompting in
both the Operate and Edit modes. From the main toolbar click the Save icon or from the
menu bar click Recipe then Save.
c. Save As… recipe will save an active recipe under a new / different file name. From the
menu bar click Recipe then save as… Type a new recipe name in File name: and click Save
As or depress the Enter key (
See
Figure 20
).
Summary of Contents for TCM-2200
Page 5: ...1 Introduction ...
Page 6: ...2 ...
Page 18: ...14 ...
Page 19: ...15 Facility Installation ...
Page 20: ...16 ...
Page 26: ...22 ...
Page 27: ...23 Operating System Software Guide ...
Page 28: ...24 ...
Page 55: ...51 ...
Page 56: ...52 ...
Page 57: ...53 ...
Page 58: ...54 ...
Page 64: ...60 ...
Page 65: ...61 Standard and Optional Equipment Operating Guide ...
Page 66: ...62 ...
Page 71: ...67 Troubleshooting Guide HC1 X or HC2 controller ...
Page 72: ...68 ...
Page 74: ...70 ...
Page 95: ...91 Figure 12 ...
Page 107: ...103 Maintenance Procedure ...
Page 108: ...104 ...
Page 110: ...106 ...