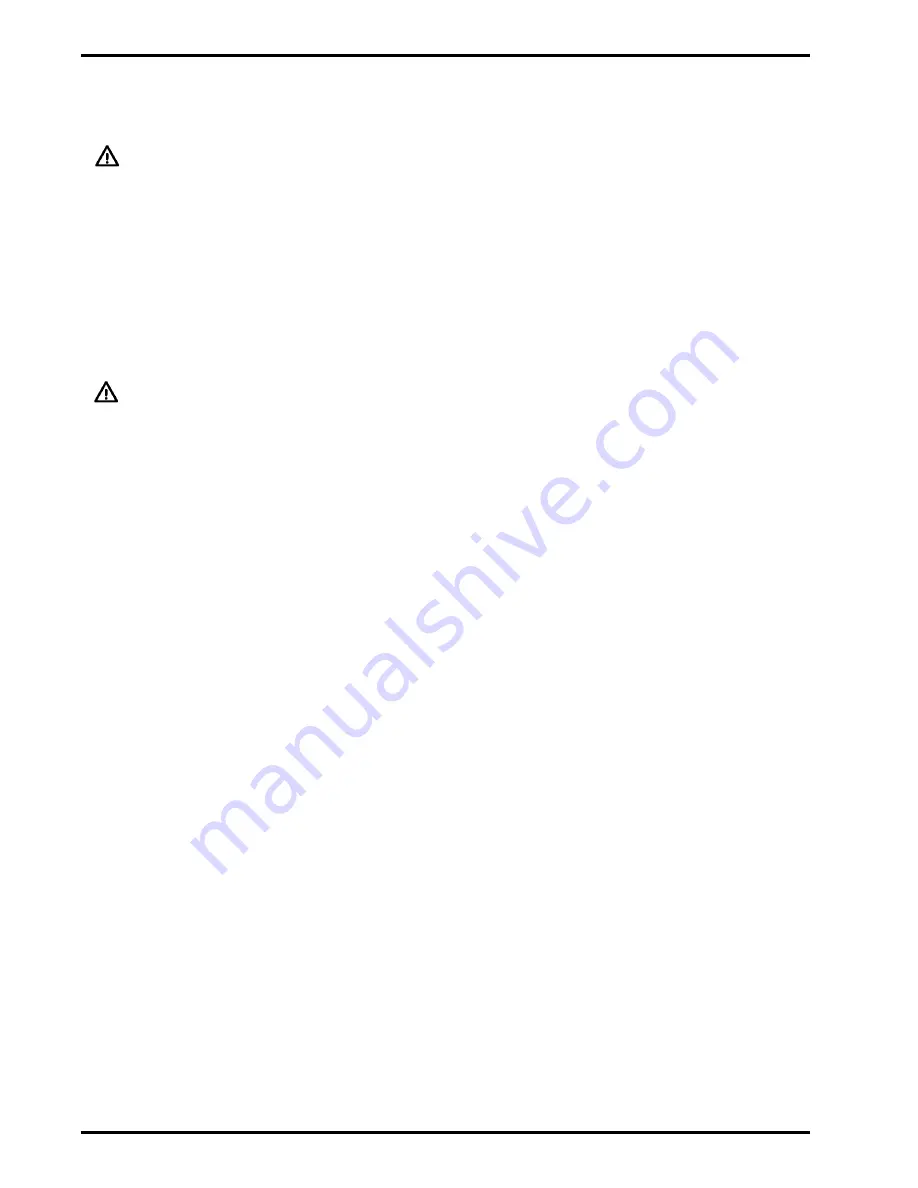
26 - FORM NO. 56043042 / Whirlamatic
™
2700 / BHS 7014
ELECTRICAL SYSTEM
________________________________________________________________________________________________________________________________________________________________________________________________________________________________________________________________________
BATTERIES
WARNING!
DISCONNECT BATTERIES BEFORE SERVICING.
Use extreme caution when working with batteries. Sulfuric acid in batteries can cause severe injury if allowed to contact the
skin or eyes. Explosive hydrogen gas is vented from inside the batteries through openings in the battery caps. This gas can
be ignited by any arc, spark or flame.
WHEN SERVICING BATTERIES...
•
Remove all jewelry.
•
Do not smoke.
•
Wear chemical goggles, rubber gloves and a protective apron.
•
Work in a well-ventilated area.
•
Do not allow tools to touch more than one battery terminal at a time.
CAUTION!
Acid can spill onto the floor if the batteries are overfilled.
To avoid damage to floor surfaces, wipe water and acid from the top of the batteries after charging.
Electrical components in this machine can be severely damaged if the batteries are not installed and connected properly.
Batteries should be installed by your local Nilfisk-Advance Distributor or by a qualified electrician.
Avoid short circuiting the charged stand-by battery pack. Keep any metal conductor(s) from making direct contact with the
battery cables and connectors. Use a non-conductor such as cardboard or plastic to protect the tops of the batteries.
________________________________________________________________________________________________________________________________________________________________________________________________________________________________________________________________________
LOW VOLTAGE CUTOUT THRESHOLD SELECTION MODE:
FACTORY DEFAULT: STD
The 2700 / BHS7014 is equipped with a low voltage cutout feature to prevent over-discharging the batteries. This feature will automatically
shut down the pad motor when the battery voltage falls to the selected threshold. The cutout level is adjustable. The standard setting
is 30.6 volts (1.70 volts per cell) and the alternate setting is 33.12 volts (1.84 volts per cell). The standard setting should be used unless
the battery manufacturer specifies the higher cutout voltage. Note: the standard cutout level is set at 1.70 volts per cell instead of 1.75
volts per cell due to the high discharge rate. This will not harm the batteries.
It is important to note that some maintenance free batteries
(including some gelled electrolyte cells) are capable of safely being used with the standard setting.
To select between the two types:
1
Press and hold pad down switch while turning the key switch on.
2
Continue holding the pad down switch until the status display is scrolling the word “SELECT”.
3
Release the pad down switch.
4
Press and release the pad down switch twice. The status display should now be scrolling “BATTERY TYPE”.
5
Press and release the pad up switch to enter the battery type selection mode.
6
The status display will now show either “STD” or “ALT”. The standard setting has a cutout level of 1.70 volts per cell and the alternate
setting has a cutout level of 1.84 volts per cell.
7
To select the desired option, press and release the pad down switch. This will alternate between the two options.
8
To save the setting and exit this mode turn the key switch off.
revised 2/02